3D PEOPLE CHAMPIONS NEXT-LEVEL POST-PROCESSING FOR FLAWLESS ADDITIVE MANUFACTURING
As manufacturers push AM to production-grade levels, 3D People, a leading UK-based subcontract 3D printing bureau, is taking a stand on why surface finish is the real game-changer in AM for production applications.
(4th March 2025, London, U.K.) In today's race for innovation, where additive manufacturing (AM) is reshaping industries, one often-overlooked factor separates cutting-edge from cut-rate — surface finish. As manufacturers push AM to production-grade levels, 3D People, a leading UK-based subcontract 3D printing bureau, is taking a stand on why surface finish is the real game-changer in AM for production applications.
"In additive manufacturing, a part's journey doesn't end when the printer stops," says Felix Manley, Co-Founder of 3D People. "It's what happens next that determines whether it's an exceptional, high-performance component."
Surface finish can directly improve part aesthetics, mechanical performance, and end-use functionality and add significant value. Due to the nature of polymer powder bed fusion (PBF) processes, unfinished parts can have unwanted roughness, which can affect friction and sealing capabilities for some applications. In industries like aerospace, automotive, and medical, where tolerances are razor-thin, the difference between a good part and a great one can be measured in microns.
With AM increasingly competing with traditional manufacturing, the demand for flawless, repeatable, and scalable finishing processes has skyrocketed. That's where 3D People's expertise comes in.
"We've invested heavily in process control for finishing technologies like vapour smoothing, vibro-polishing, and precision dyeing," says Sasha Bruml, Co-Founder of 3D People. "Our customers don't just need parts — they need parts that look and perform like they belong in the real world. And that means next-level surface refinement."
Performance and durability are key factors in determining the success of AM parts. Smoother surfaces reduce friction, wear, and failure rates, making them critical for moving parts and high-stress applications. For some applications, it is not only about functionality as aesthetics and branding can play a huge role in the demand for advanced finishing — especially in consumer products where visual perfection sells. A rough, unfinished AM part is simply not acceptable. Additionally, some industries require stringent regulatory compliance, where tight tolerances and superior surface quality ensure safety and functionality.
"People often assume AM produces a ready-to-use part straight from the printer," adds Bruml. "The reality? Some post processing is always necessary, but raw, cleaned parts are often just the beginning. Without superior finishing, many AM applications won't meet industry standards, and they definitely won't meet customer expectations."
As AM adoption grows, 3D People is leading the charge in industrial-grade post-processing and finishing, proving that quality is a product of more than just a layer-by-layer process — it's an end-to-end commitment.
For companies looking to elevate their AM production activities, 3D People offers finishing solutions that turn good parts into great ones, because as Manley says, "Surface finish is never just a detail. It's the difference that matters."
www.3dpeople.uk
Featured Product
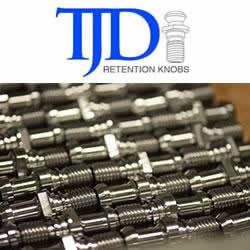