Advantages and disadvantages of stamping process
Stamping technology is widely used in the current mechanical processing industry. Let us understand the difference between stamping technology and traditional technology.
What are the advantages and disadvantages of stamping compared with traditional machining?
Compared with traditional machining, stamping has the following advantages:
1. High material utilization rate: The stamping process uses quantitative cutting of the mold, which can cut the required materials to the maximum extent, causing almost no waste, and the material utilization rate is higher than that of traditional processing.
2. High processing precision: The stamping machine uses high-precision CNC equipment for operation, with high precision and strong repeatability, which is suitable for the production of high-precision parts, complex structures and other high-quality requirements.During stamping, the mold ensures the size and shape accuracy of the stamped parts, and generally does not damage the surface quality of the stamped parts. The life of the mold is generally long, so the quality of stamping is stable.
3. High production efficiency: The stamping process is simple to operate and has a high degree of automation. This is because stamping relies on dies and stamping equipment to complete the process. The stroke frequency of an ordinary press can reach dozens of times per minute, while high-speed presses can reach hundreds or even thousands of times per minute, and each stamping stroke may produce a stamped part.It can process workpieces quickly, is suitable for large-scale production, and greatly improves production efficiency.
4. Lower cost: Due to many factors such as high material utilization, high processing precision, and high production efficiency, the cost of stamping processing is lower and suitable for large-scale production.
5. Wide range of applications: Stamping processing is not limited by materials and is suitable for the processing of various materials such as metals and non-metals. It is suitable for production in the fields of automobiles, agricultural machinery, electrical appliances, construction, etc.
6. Environmental protection and energy saving: Stamping generally does not produce cutting edge materials, consumes less raw materials, and does not require other heating equipment. Therefore, it is an environmentally friendly and energy-saving processing method.
7.Stamping can produce parts with a large size range and complex shapes, such as stopwatches as small as clocks, longitudinal beams and covering parts of automobiles, etc. In addition, the cold deformation hardening effect of the material during stamping makes the strength and rigidity of stamping relatively high.
Disadvantages of stamping compared to traditional machining:
1. High mold requirements: Stamping processing requires high-quality molds, and the manufacturing of molds is complex and has a long cycle.Stamping processing must have corresponding molds, so it is most suitable for large-scale production, and is subject to certain restrictions for single-piece and small-batch production.
2.High equipment cost: Stamping equipment is usually expensive and requires a large initial investment.The molds used for stamping are generally more complicated.
3.Die design focuses on classical theory and experience, requires strong imagination and creativity, and places high demands on mold designers and manufacturers.
4.Stamping is usually done with a mechanical press, which has a fast operating speed and is more labor-intensive when operated manually.
Application fields of stamping processing:Stamping processing is widely used in the manufacture of automobile bodies, chassis, fuel tanks, radiators, boiler drums, container shells, motors, electrical core silicon steel sheets and other products. In addition, there are also a large number of stamping parts in products such as instruments and meters, household appliances, bicycles, office machinery, and daily utensils.
Featured Product
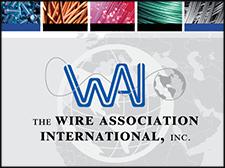
The Wire Association International (WAI), Inc.
The Wire Association International (WAI), Inc., founded in 1930, is a worldwide technical society for wire and cable industry professionals. Based in Madison, Connecticut, USA, WAI collects and shares technical, manufacturing, and general business information to the ferrous, nonferrous, electrical, fiber optic, and fastener segments of the wire and cable industry. WAI hosts trade expositions, technical conferences, and educational programs.