Signode to Showcase New Advancements and Integrated Packaging Systems at ProMat 2025
Signode, a leading global manufacturer of a broad range of transit packaging equipment, tools, consumables, automation and support solutions, is highlighting its integrated automation systems and industry-leading packaging technologies at ProMat 2025.
Tampa, FL (February 18, 2025) - Signode, a leading global manufacturer of a broad range of transit packaging equipment, tools, consumables, automation and support solutions, is highlighting its integrated automation systems and industry-leading packaging technologies at ProMat 2025. Held at McCormick Place in Chicago, Illinois from March 17-20, visitors to booth S-1947 will experience how Signode solutions work seamlessly together to create cohesive systems that address the unique challenges of modern supply chains.
"ProMat is a great platform to connect with other industry leaders and have real conversations about their operational goals," said Shawn Semer, Vice President of Global Automation for Signode. "We're excited to share the recent additions to our innovative portfolio and demonstrate how we combine our technologies to deliver integrated solutions to meet our customers' demands."
Signode Automation Technologies in Action
Among the booth highlights will be a fully integrated system, running live to showcase how seamlessly Signode technologies work together to deliver a complete end-of-line packaging solution. By bringing together advanced robotics, innovative strapping and wrapping technologies, and consumables, manufacturers can streamline operations while maintaining load integrity throughout the transit journey.
Signode will present the enhanced capabilities of its SimplimaticⓇ Autonomous Mobile Robot (AMR), working in tandem with the Simplimatic robotic palletizer and depalletizer, to handle diverse loads with speed and accuracy. Engineered for optimal throughput, service life, and versatility, these systems provide flexible options for loading single or multiple pallets, and integrate effortlessly with most material handling lines.
As a palletized load moves down the line, the TP-12 strapper uses advanced strap tension technology to enhance load stability. The integrated packaging system incorporates the Octopus® S Series stretch wrapper with its unique "S" wrap pattern to further optimize load containment and minimize film usage without sacrificing speed or strength. Capable of wrapping over 100 loads per hour, this system balances efficiency and performance to meet the demands of high-volume operations.
Streamlined Solutions for Reliable Load Containment
In late 2024, Signode introduced the BXT4 plastic strapping hand tool, SGP-5330 bundler, and Dylastic® Pro strap, and ProMat attendees will have the opportunity to experience these new innovations in the booth. Signode specialists will be onsite to guide hands-on demonstrations of the ergonomic BXT4 with EasyTrigger™ technology, designed to simplify the strapping process while enhancing operator efficiency. Alongside it, the fully automated SGP-5330 features IoT integration and a smart touchscreen interface, providing real-time insights for proactive maintenance and enhanced productivity. When paired with the new Dylastic Pro strap, these solutions create a powerful combination for securing loads efficiently and effectively.
Signode will also showcase an integrated case packaging system, combining case forming, packing, and sealing into a seamless, automated solution. The SP-304 case former easily prepares boxes for filling, forming cases and tapes the bottom with minimal manual intervention. Once formed and packed, the LD-16 case sealer, a fully automatic system designed to handle multiple box sizes within pre-programmed dimensions, finishes the job. Together, this duo delivers precision and adaptability to meet diverse packaging demands.
Packaging Solutions Beyond the Equipment
Signode's comprehensive approach is further strengthened by a diverse portfolio of protective packaging, dunnage, and transit packaging solutions, all designed to elevate customers' operations and reinforce the commitment to their ongoing success. These and all Signode offerings are backed by industry-leading service and support, including the Packaging Plus Reliability Services program. Customizing solutions to meet transit packaging needs, Signode leverages IoT capabilities for remote monitoring and service, alongside on-site support from the Customer Experience Center and Packaging Lab in Roselle, IL.
To learn more about integrated Signode solutions and the benefits of long-term partnership, visit booth S-1947 at ProMat, or visit www.signode.com.
###
About Signode
With over $2B+ in revenue, 80+ manufacturing facilities across 6 continents, and over 7,000 employees worldwide, Signode is a leading manufacturer of a broad spectrum of transit packaging consumables, tools, software, and equipment that optimize end-of-line packaging operations and protect products in transit. Signode brings this extensive product portfolio together under a family of trusted brands to offer optimized and complete transit packaging solutions to its customers.
Featured Product
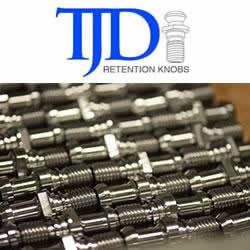