NORD DRIVESYSTEMS to Showcase Innovative Supply Chain Solutions at ProMat 2025
NORD’s supply chain system solutions focus on high-efficiency, reliability, and versatility to power a wide range of applications.
NORD DRIVESYSTEMS will be attending ProMat 2025 with their latest supply chain technology, equipment, and system solutions. This year's exhibition is being held March 17 - 20 at the McCormick Place Convention Center in Chicago, Illinois and is one of the best opportunities to see leading solution providers in-person, gain insights on leading trends, and foster strong industry partnerships. NORD's modular product design delivers versatility with over 20,000,000 unique configurations of gear boxes, electric motors, and electronic control products - enabling the ideal drive system for nearly every application. Their specialized supply chain solutions focus on high-efficiency, reliability, low maintenance, and long service life.
NORD will be showcasing the following industry solutions at ProMat Booth S2312:
IE5+ Permanent Magnet Synchronous Motors
The new generation of NORD IE5+ synchronous motors feature permanent magnet technology for reduced energy loss, consistent high-efficiency even at partial loads and low speeds, and high-power density. Their constant torque over a wide speed range enables fewer system variants as well as provides a fast Return on Investment (ROI). A smooth surface, non-ventilated variant (TENV) is available for hygienic wash-down environments while a ventilated variant (TEFC) offers optimized heat dissipation for applications with heavy traffic.
NORDAC ON/ON+ Variable Frequency Drives
NORDAC ON/ON+ variable frequency drives were developed to meet the special requirements of horizontal conveyor technology. NORDAC ON drives are designed for compatibility with IE3 asynchronous motors and NORDAC ON+ drives are optimized for combination with IE5+ synchronous motors. Both versions are characterized by an integrated multi-protocol Ethernet interface, full Plug-and-Play capabilities for fast commissioning, and dynamic PLC functionality for drive-related functions in a compact, reliable design for IIoT environments.
LogiDrive® Complete Drive Solution
LogiDrive is a complete drive solution that utilizes a standardized, service-friendly system to significantly reduce planning and commissioning time. There are basic and advanced versions available for adaptation to a variety of applications. Basic versions include a gear unit, efficient IE3 electric motor, and variable frequency drive with a focus on cost effectiveness. Advanced versions feature a compact gear unit, high-efficiency IE5+ synchronous motor, and variable frequency drive that address issues such as energy efficiency, variant reduction, and reduced Total Cost of Ownership (TCO).
NORDBLOC.1® Helical Bevel Gear Units
NORDBLOC.1 two-stage helical bevel gear units feature efficient operation in a compact, modular design ideal for conveyor and processing systems. They are made from high-strength aluminum alloy and offer a large speed range, quiet operation, and high axial and radial load capacities. Two housing styles, open for optimized heat dissipation in heavy traffic areas and closed for hygienic, wash down areas, along with flexible input and output options ensure complete application and environmental versatility.
NORDBLOC.1® Helical Inline Gear Units
NORDBLOC.1 helical inline gear units are made from high strength, low weight aluminum alloy UNICASE™ housings, ensuring long service life with increased stability and safe operation. Their smooth surfaces do not have bore plugs or assembly covers to prevent the pooling of liquids and solids, making them extremely easy to clean. High output torques paired with efficient operation reduce system costs for a lower TCO and a fast Return on Investment (ROI). Additionally, both foot and flange mounting options are available for flexible installation.
Condition Monitoring for Predictive Maintenance
Condition Monitoring for predictive maintenance utilizes a status-based maintenance approach to extend the service life of components and machines, increase system availability, and reduce service and material costs. With this method, drive and status data are recorded periodically or continuously to optimize the operational safety and efficiency of systems. The data analysis results enable the machines to be proactively maintained and downtimes to be planned. Condition Monitoring additionally can determine the optimal time to change the unit's oil, ensuring systems always operate at their highest ability.
www.nord.com
Meta title: NORD DRIVESYSTEMS to Feature Next-Generation Drive Technology at ProMat 2025.
Meta description: NORD will have their modular gear units, high-efficiency motors, and intelligent variable frequency drives on display at ProMat Booth S2312.
Keywords: NORD, NORD DRIVESYSTEMS, drivesystems, drive systems, gear units, gear box, gearboxes, intralogistics, supply chain, logistics, ProMat, exhibition, NORDAC, IE5+, electric motors, asynchronous motors, PMS motors, permanent magnet, electronic controls, control products, variable frequency drive, frequency inverter, inverter, VFD, LogiDrive
Featured Product
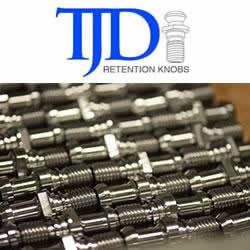