The manufacturing industry is undergoing a profound transformation driven by the advent of Industry 4.0 technologies. This article examines the key technologies underpinning Industry 4.0 and their transformative impact on manufacturing.
Manufacturing in the Age of Industry 4.0
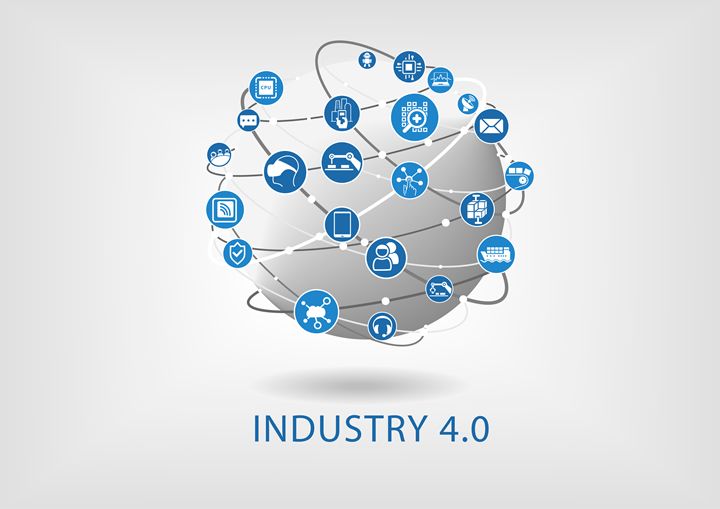
Choon-Hin Chang, Product Marketing Manager | Keysight Technologies
The manufacturing industry is undergoing a profound transformation driven by the advent of Industry 4.0 technologies. Industry 4.0 revolutionizes traditional manufacturing processes by introducing automation, data exchange, and advanced analytics. Industry 4.0, the fourth industrial revolution, leverages interconnected systems, real-time data, and smart technologies to create more efficient, flexible, and innovative manufacturing environments. This article examines the key technologies underpinning Industry 4.0 and their transformative impact on manufacturing.
The Evolution of Industry
The evolution from Industry 1.0 to Industry 4.0 represents a transformative journey in manufacturing and industry, as shown in Figure 1.
Figure 1. The four industrial revolutions
Industry 1.0 (late 18th century): The original industrial revolution, this era marked the advent of mechanization, using water and steam power to transition from manual labor to mechanical production. Key innovations, such as the steam engine, revolutionized the industry by enabling machines to take over tasks previously performed by hand.
Industry 2.0 (late 19th century): The second industrial revolution introduced mass production with electricity and assembly lines. This era revolutionized manufacturing processes, significantly boosting productivity and scale.
Industry 3.0 (late 20th century): Also known as the digital revolution, Industry 3.0 introduced automation through electronics and IT systems, leading to computerized automation that greatly enhanced manufacturing efficiency and precision. This phase saw the integration of computers into the workforce, with the advent of programmable logic controllers, robots, in-circuit test (ICT) electronics, and other information technologies. Additionally, this era marked the beginning of internet access and the use of renewable energy, sparking a new wave of industrial innovation.
Industry 4.0 (21st century): Industry 4.0 expands on the digital revolution by integrating cyber-physical systems, the Internet of Things (IoT), artificial intelligence (AI), big data analytics, and other cutting-edge technologies into manufacturing processes. This phase focuses on interconnectedness, real-time data exchange, and intelligent decision-making, ushering in a new era of automation, efficiency, and customization in production.
Each industrial revolution represents a significant leap forward in the production of goods, leveraging increasingly advanced technologies to drive efficiency, productivity, and innovation across industries.
Navigating the Era of Industry 4.0 in Technologies
Industry 4.0 marks a revolutionary phase in manufacturing, characterized by the seamless integration of cutting-edge digital technologies into production processes, as shown in Figure 2. Industry 4.0 technologies transform the manufacturing landscape, significantly enhancing efficiency and productivity and fostering innovation. It highlights the pivotal role of key technologies such as IoT, AI, big data analytics, robotics, and additive manufacturing, examining their profound impact on industry.
Figure 2. Industry 4.0
IoT connects machines, systems, and sensors, enabling real-time data collection and communication across the manufacturing ecosystem. This connectivity facilitates predictive maintenance, reduces downtime, and optimizes production processes. AI leverages machine learning algorithms to analyze vast amounts of data, enabling smarter decision-making, process automation, and quality control. Big data analytics harnesses the power of data to uncover insights, drive strategic decisions, and enhance operational efficiency.
Robotics transforms manufacturing by automating repetitive tasks, improving precision, and increasing production speed. Collaborative robots, or cobots, work alongside human operators, enhancing flexibility and productivity on the factory floor. Additive manufacturing, also known as 3D printing, enables the creation of complex, customized products with reduced material waste and shorter production cycles.
While the benefits of Industry 4.0 are substantial, manufacturers face challenges in adopting these technologies. Integrating legacy systems with new digital solutions, ensuring cybersecurity, and managing the skills gap in the workforce are critical considerations. Additionally, significant investment in technology and infrastructure is necessary to fully realize the potential of Industry 4.0.
Despite these challenges, the future of manufacturing in the age of Industry 4.0 is promising. As companies continue to adopt and integrate these technologies, industry will witness unprecedented levels of efficiency, innovation, and competitiveness. The convergence of IoT, AI, big data, robotics, and additive manufacturing is set to redefine traditional manufacturing paradigms, paving the way for a smarter, more agile, and more resilient industrial landscape.
Advantages of Adopting Industry 4.0 in Manufacturing
Manufacturing in the age of Industry 4.0 offers numerous advantages over traditional production processes. By integrating advanced technologies and data-driven systems, companies can unlock new growth and efficiency opportunities. Key advantages of Industry 4.0 in manufacturing include the following:
- Improved operational efficiency and productivity: Industry 4.0 enables manufacturers to optimize operations through automation and real-time data analysis. Smart machines and interconnected systems streamline processes, minimize downtime, reduce errors, and increase overall productivity.
- Enhanced product quality and customization capabilities: Industry 4.0 empowers manufacturers to produce high-quality products with greater precision. Advanced sensors, robotics, and AI enable companies to monitor and control production variables, resulting in improved product quality. Additionally, Industry 4.0 technologies offer flexibility for customized production, catering to individual customer needs and preferences.
- Optimized supply chain management and logistics: Industry 4.0 provides real-time visibility and control over the entire production process. With IoT devices and data analytics integration, manufacturers can track inventory levels, monitor equipment performance, and optimize logistics operations. These capabilities lead to reduced costs, enhanced inventory management, and improved delivery timelines.
Industry 4.0 Use Cases and Success Stories
Industry 4.0 is transforming the manufacturing sector by leveraging advanced technologies to optimize processes, increase efficiency, and drive innovation. This section explores use cases and success stories that showcase the transformative impact of Industry 4.0.
Smart factories are prime examples of Industry 4.0 in action. These digitally connected factories use technologies such as IoT, AI, robotics, and big data analytics to automate and optimize operations. By integrating machines, devices, and systems, smart factories enable real-time monitoring, predictive maintenance, and efficient resource allocation. The result is increased productivity, reduced downtime, and enhanced quality control.
Industry 4.0 has applications across industry sectors. For instance, in the automotive industry, manufacturers are implementing connected car technologies, enabling vehicles to communicate with each other and with infrastructure, improving safety and efficiency on the roads. In healthcare, Industry 4.0 is transforming the manufacturing of medical devices, leading to personalized healthcare solutions and improved patient outcomes.
Real-world success stories of companies embracing Industry 4.0 abound. For instance, a leading electronics manufacturer adopted advanced robotics and automation to streamline its production line, resulting in a significant reduction in manufacturing costs and increased product quality. Another company implemented IoT-enabled sensors and analytics to optimize energy consumption, leading to substantial savings and reduced environmental impact.
Sustainability Opportunities in Industry 4.0
One key aspect of sustainable manufacturing in the age of Industry 4.0 is the integration of these advanced technologies. By leveraging IoT devices, manufacturers can collect real-time data on energy consumption, production processes, and resource utilization. This data enables them to identify energy-intensive areas and implement energy efficiency measures, reducing environmental impact.
Energy efficiency is crucial for sustainable manufacturing. Industry 4.0 technologies enable manufacturers to monitor energy use in real time, optimize equipment performance, and identify potential energy-saving opportunities. By implementing smart controls and predictive maintenance, manufacturers can reduce energy waste, lower carbon emissions, and achieve greater sustainability.
Waste reduction is another area Industry 4.0 can significantly impact. By leveraging AI and big data analytics, manufacturers can optimize production processes, minimize material waste, and improve resource utilization. Real-time monitoring and predictive analytics enable manufacturers to identify inefficiencies, reduce scrap, and optimize material usage, resulting in a more sustainable manufacturing process.
Additionally, Industry 4.0 promotes circular economy principles, aiming to minimize waste and maximize resource efficiency through reuse, repair, and recycling. Industry 4.0 technologies enable manufacturers to track and trace products throughout their life cycle, facilitating efficient reverse logistics and adopting circular economy practices.
By integrating advanced technologies, reducing environmental impact through energy efficiency and waste reduction, and embracing circular economy principles, manufacturers can drive sustainable manufacturing practices and contribute to a greener future.
Conclusion
Industry 4.0 technologies are reshaping the manufacturing landscape, enhancing efficiency, productivity, and innovation. By adopting these technologies, manufacturers are more adept at meeting the demands of a dynamic and competitive market. The potential benefits of Industry 4.0 outweigh the challenges, promising a smarter, more interconnected, and more sustainable future for manufacturing. This ongoing digital transformation marks a new era in which technology and human creativity merge, opening unprecedented opportunities in the manufacturing sector.
The fusion of Industry 4.0 and smart manufacturing is ushering in a new era of production characterized by agility, efficiency, sustainability, and profitability.
About the Author
Choon-Hin Chang
Product Marketing Manager
Keysight Technologies
Chang has 30 years of experience in project management and engineering leading new product introductions as well as business, manufacturing, process improvement, supply chain management, strategic sourcing, and operations. He is currently Product Marketing Manager for manufacturing and power products. Chang received his B.Eng (Hons) in Electrical and Electronics Engineering from the University of Aberdeen.
The content & opinions in this article are the author’s and do not necessarily represent the views of ManufacturingTomorrow
Comments (0)
This post does not have any comments. Be the first to leave a comment below.
Featured Product
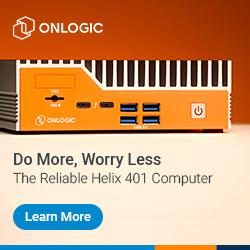