Harnessing the full potential of these next-generation solutions demands a robust communication network capable of transporting vast amounts of data from the factory floor to the data center's IT infrastructure.
Combining the Best of Both Worlds: Laying the Hybrid Network Foundation for a Smart Factory
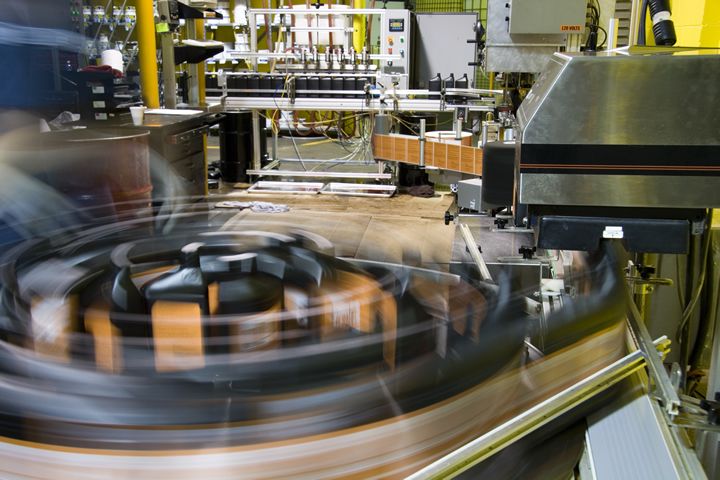
Giovanni Prinetti, Solutions Marketing Manager | Allied Telesis
Production lines have used computer-controlled equipment for decades. Now, fueled by advancements in the Internet of Things (IoT), we're witnessing a rapid shift towards "smart factories." Technologies like robotic cells, smart sensors, drones, and autonomous guided vehicles are transforming production lines, boosting efficiency, and reducing manual labor costs. It also leads to environmental benefits like the reduction of waste and the optimization of energy usage.
Harnessing the full potential of these next-generation solutions demands a robust communication network capable of transporting vast amounts of data from the factory floor to the data center's IT infrastructure. In sprawling manufacturing complexes, spanning acres of buildings and land, establishing such a network presents a unique challenge.
Using wireless technology in the production line adds complexity, making reliable communication more challenging.
Multi-Channel vs. Single Channel
Historically, achieving industrial-grade Wi-Fi with high-density coverage and seamless roaming required a choice between multi-channel and single-channel architectures.
- Multi-Channel: This predominant architecture utilizes different radio channels on each access point (AP). While effective in most scenarios, it struggles in dynamic environments like warehouses, where radio interference from moving objects can reduce throughput. Roaming in large facilities can also be disruptive due to the need to re-establish security credentials.
- Single-Channel: This architecture employs a single radio channel for all APs, eliminating interference and simplifying deployment. If coverage was poor in one location, additional APs could be easily deployed without worrying about introducing bandwidth-destroying interference. However, although the single-channel architecture solved one of the biggest challenges of Wi-Fi network design, it too had some limitations, the main one being that its total network throughput was usually lower than multi-channel.
The Emergence of True Hybrid Networks
Attempts to combine both architectures were often costly and complex, requiring separate systems or cumbersome workarounds. A true hybrid solution, however, now offers the best of both worlds: the throughput of multi-channel with the easy deployment and seamless roaming of single-channel. This is achieved by configuring both architectures simultaneously on the same hardware, tailoring the network to the specific application.
Kingsland Drinks Puts On a Hybrid Blanket
Let’s look at one example of how a hybrid solution changed everything for a UK-based major manufacturer.
Kingsland Drinks is a premier independent UK supplier of bulk wine and spirits. It has evolved into an employee-owned business with more than 400 staff members and has seven automated production lines with extensive capability operating 24/7.
Kingsland’s production environment has a high reliance on the IT infrastructure to monitor and manage the movement of stock within the enormous facility. The company installed a Wi-Fi system a few years ago with the intention that all forklift drivers would have a handheld scanner and be able to move stock around by scanning it in from one location to another. Not unlike many factory operations, however, the Kingsland cavernous warehouse facility has conditions that are usually detrimental to reliable wireless network connectivity including four-foot thick walls, outdoor areas for loading and unloading trucks, office and meeting spaces, as well as regular temperature fluctuations throughout the area. As a result, their existing WLAN, despite being relatively new, suffered from dead spots, hindering their inventory management system.
Brian Polkinghorne, the IT Manager at Kingsland Drinks, explains, “Plain and simple, the Wi-Fi failed us. As a result, forklift drivers had to dismount to find a PC and enter information manually. That cost us a crazy amount of time in manhours just moving stock about the site.”
The solution was a single/multi-channel true hybrid network concept that acts as a highly resilient “blanket” providing seamless roaming for clients. The multi-channel side of the network uses all available channels which are carefully managed to avoid interference, whereas a single-channel solution uses one wireless channel to create a single ‘blanket’ of wireless coverage across every area, thereby eliminating interference and resulting in a powerful solution that enables the best of both architectures.
All APs in the network appear as if they are a single AP, so the mobile client only sees that it is connected to one large AP. When the client moves, the Wi-Fi assigns it to a new AP, so the client is unaware of the “roam” and needs no special features to support it (e.g. fast-roaming protocols). Not only does this simplify the client, but it means the Wi-Fi connection is not interrupted by the move, and no latency is introduced, or data lost.
Polkinghome says this approach has yielded significant increases in productivity and efficiency, and a smoother experience for employees using handheld scanners and forklifts.
Smart Factory Approach = Smart Decision
In today's rapidly evolving manufacturing landscape, networks must be agile and adaptable. The complexity of modern applications and service delivery models demands a flexible foundation. True hybrid networks offer that foundation, providing the performance, reliability, and scalability required to support the smart factories of the future.
Investing in a true hybrid network is not just an upgrade; it's a strategic decision. It's a decision that will empower smart factory initiatives, enhance productivity, and unlock new possibilities for innovation and growth.
Giovanni Prinetti, Solutions Marketing Manager: With over 15 years of experience at Allied Telesis and a lifelong commitment to the ICT industry, Giovanni Prinetti specializes in network solutions for various vertical markets, promoting them within global markets. His extensive background in ICT enables him to simplify complex topics, making them accessible to corporate figures without specific expertise. Giovanni holds a degree in Electrical Engineering from the Politecnico di Milano. He began his career in June 1993 at the Research and Development Laboratories of Italtel, focusing on IP and ATM transmission system architectures in collaboration with the CSELT research center and CEFRIEL. In 2001, Giovanni joined STMicroelectronics, where he worked on integrated VoIP solutions within the Telecom division. During this period, he also dealt with hardware and software system-on-chip architectures for xDSL and wireless applications.
The content & opinions in this article are the author’s and do not necessarily represent the views of ManufacturingTomorrow
Comments (0)
This post does not have any comments. Be the first to leave a comment below.
Featured Product
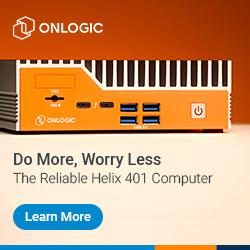