Variable Frequency Drives (VFDs) are the backbone of modern and legacy industrial systems, managing tasks from powering fans and compressors to enabling intricate robotic operations. For more complex industrial operations, the need for precise coordination between drives escalates.
Master-Follower Configuration: Precision Control with Encoder-Based VFD Synchronization
Matt Sherman | KEB America
Variable Frequency Drives (VFDs) are the backbone of modern and legacy industrial systems, managing tasks from powering fans and compressors to enabling intricate robotic operations. For more complex industrial operations, the need for precise coordination between drives escalates.
This article explains the differences between single-axis and multi-axis applications, with a focus on the “master-follower” configurations for synchronized motion.
Single-Axis Applications: Simplicity and Reliability
In single-axis applications, each drive operates independently to control its motor without synchronizing with other drives. A classic example is a pump drive, where a single motor provides all the necessary power. This setup is simple and reliable, making it suitable for applications where individual motor control is enough to meet operational requirements.
Multi-Axis Applications: Working Together
In more complex industrial scenarios, multiple drives must work in concert, giving rise to multi-axis applications. These setups require a higher degree of coordination to ensure all drives work together as a team. Coordination can range from simple discrete I/O to sophisticated synchronization that ensures precise movement alignment.
Master-Follower Configuration: Synchronized Motion
For applications where the motion of the drives must be completely synchronized, master-follower (or master-slave) configurations are the solution. In these systems, a master drive controls one or more follower drives, ensuring their motions are perfectly aligned. This approach is especially advantageous in applications involving belts, linkages, or other mechanical couplings where precise coordination is crucial.
**Note: The terms master-follower and master-slave are often used interchangeably. The term master-follower will be used here because it is more function-specific to synchronized motion.
Master-follower Configuration between two S6 Drives using TTL Encoder Feedback
Advantages of Master-Follower Systems
Master-follower systems offer a powerful combination of flexibility and control, making them a game-changer for many industrial applications. Here’s how they elevate your operation:
- Software Flexibility: Virtual gear ratios and rotation directions can be easily adjusted via software, eliminating the need for physical modifications.
- Scalability: Follower motors can be relocated or replaced without extensive redesign, unlike rigid mechanical systems requiring significant rework for minor changes.
- Load Distribution: Multiple motors share the torque load, allowing for a more efficient use of smaller motors rather than relying on a single large motor. This distribution can improve system resilience and reduce the risk of overloading individual components.
- Reduced PLC Load: When signals are transferred directly from drive-to-drive, like with encoder-based master-follower, the functionality can be offloaded from the PLC. This reduces PLC development time, code complexity, and even PLC cost.
Master-follower configurations emulate mechanical couplings using electronic synchronization, providing precise control without the physical limitations of gears and belts.
For instance, electronic gear ratios can be set so that a follower drive completes one revolution for every two revolutions of the master drive, offering the benefits of mechanical coupling without the associated spatial constraints or wear issues. Adjustments to these ratios and other parameters can be made through software, enhancing flexibility and scalability.
High-Speed Synchronization with Encoder Signals
A primary challenge in master-follower configurations is maintaining high cycle times to minimize following errors. Precise synchronization requires that setpoints be transmitted from the master to the followers at very high speeds. Encoder signals, processed on the order of microseconds, are ideal for this task, providing the necessary speed and accuracy.
By outputting an encoder signal from the master drive to the follower drives, the system ensures high-speed, accurate synchronization. Encoder signals provide a real-time reference that follower drives can use to match the master drive’s speed and position, ensuring seamless operation even in complex applications. For applications with more than one follower drive, it is recommended to use a Master-Slave-Repeater for each additional drive to ensure signal integrity.
KEB’s Master-follower Supported Solutions
KEB’s S6 and F6 drives support encoder-based master-follower configurations with the latest Application & Pro Control card firmware. These drives can output speed and position data from the master drive to the followers via incremental encoder emulation. This high-speed data transfer enables precise control and easy adjustments through software.
Master-follower Configuration with Servo Motors
KEB’s Master-follower Functionality
KEB’s master-follower functionality provides two synchronization options to perfectly align movements:
- Speed Synchronization: This method is simpler to implement and ideal for applications where maintaining a consistent speed ratio is sufficient. However, due to accumulated errors, it may lose positional accuracy over time.
- Angular Synchronization: This more advanced method corrects for positional discrepancies, ensuring precise coordination without accumulated errors. It is particularly ideal for applications requiring exact positional alignment like printing presses or multi-axis cutting machines.
Industrial Applications of Master-Follower Configurations
Master-follower configurations are used in various industrial applications where precise control and synchronization are critical. Examples include:
- Material Handling Systems: Synchronizing conveyors to ensure smooth and coordinated movement of materials.
- Winders: Ensuring multiple drives work in perfect harmony, preventing tears and breaks, and delivering flawlessly wound materials.
- Theater: Lifting heavy sets or complex stage structures requires a delicate balance. Master-follower distributes the load effortlessly across multiple drives, ensuring smooth and safe operation.
Conclusion: Master-follower Setup
The encoder-based master-follower configuration enables industrial operations to achieve high precision and efficiency with minimal development effort. With advanced solutions like KEB’s S6 and F6 drives, implementing these configurations becomes straightforward, ensuring robust and accurate synchronization tailored to your specific needs.
For more information or assistance with master-follower setups, contact a KEB applications engineer. By leveraging these technologies, you can enhance your system’s performance, reliability, and scalability, paving the way for more advanced and integrated industrial applications.
The content & opinions in this article are the author’s and do not necessarily represent the views of ManufacturingTomorrow
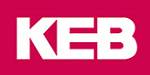
KEB America, Inc.
KEB America is a trusted manufacturer of industrial automation products in North America. We manufacture, assemble, and support our German-engineered suite of controls, drives, motors, brakes, and clutches at an ISO 9001:2015 certified, 150,000-square-foot facility in Shakopee, Minnesota.
Other Articles
Liquid-cooling VFD Increases Efficiency and Savings in Plastics Machinery
More about KEB America, Inc.
Comments (0)
This post does not have any comments. Be the first to leave a comment below.
Featured Product
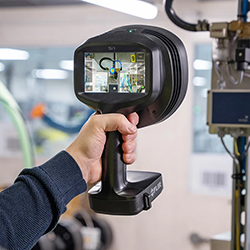