When you buy the best equipment, you want the best components, too. That's why Community Beer Company uses an EPC encoder in their brewing equipment.
Motion feedback really is everywhere – Here's how encoders help make beer
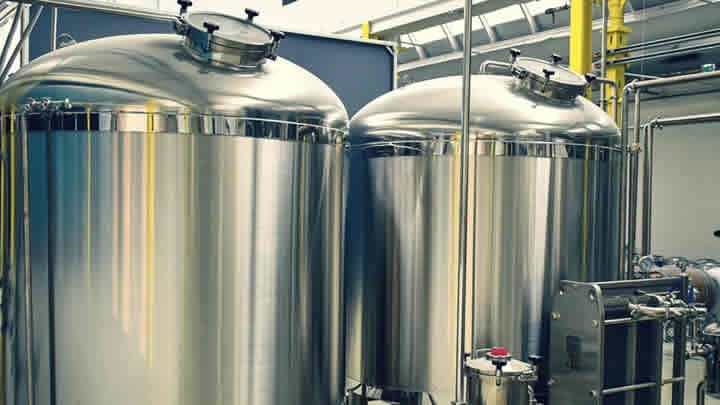
Case study from | Encoder
Background 
Community Beer Company in Dallas, Texas, is an award-winning craft beer business committed to quality. Known for growing their own yeast in-house and for their top-notch equipment, Community Beer Company has "invested in the finest, most sophisticated brewing and packaging equipment made."
When you buy the best equipment, you want the best components, too. That's why Community Beer Company uses an EPC encoder in their brewing equipment.
The Problem 
To understand where an encoder is needed in the beer brewing process, we need to understand a little about the process itself.
Part of beer-making involves mashing, where grains move through the mill, into the grist hopper, and are transferred via flex auger to the mash tun. Hot water is added at specific temperatures to convert the starches in the barley into simple sugars.
Then there's lautering, which takes place in the lauter tun. It's in this vessel where precise motion is needed to get the taste of the beer just right. You see, the lautering process is where the liquid solution known as "wort" is separated from the solid grains, forming the foundation for the beer's flavor.
The wort is then pumped into the boil kettle where the hops are added, contributing to the bitterness, flavor, and aroma of the finished product. From there, the liquid gets ready for fermentation, the final stage of the brewing process before bottling.
Automating beer-making improves production efficiency and the quality of the beer, particularly during the lautering stage. Inside the lauter tun, a motorized rake gently breaks up the grain bed, allowing for the highest quality wort to be extracted. The grains are sprayed with hot water during this phase to recover all of the remaining sugars. On top of the lauter tun is the motor and gearbox which drive the screw jack, raising and lowering the rake inside as the liquid level changes. Community Beer was having trouble positioning the rake inside the lauter tun, resulting in poor sweeping of the grains, slowing wort extraction, and inhibiting the entire brewing process. Community Beer reached out to EPC to see if we could help them better control the motion of the screw jack and rake inside the vessel.
The Solution
After understanding where the encoder would fit into the brewing process, Zac Zacharias, Central Regional Sales Manager, knew exactly which encoder was the perfect fit: EPC's Model 716 Cube encoder.
We discovered that by putting the Model 716 on the gearbox driving the screw jack, it would correctly raise and lower the rake inside the lauter tun, loosening the grains and effectively extracting the wort. With such a precise process, reliable motion feedback is a must to ensure the equipment functions efficiently so that each batch is exactly what the brew master was aiming for.
After the Model 716 was installed and testing completed, Community Beer reported that the rake was sweeping the grains effectively and eliminating the bottleneck in the lauter tun.
The content & opinions in this article are the author’s and do not necessarily represent the views of ManufacturingTomorrow
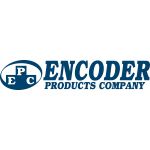
Encoder Products Company
At Encoder Products Company, we specialize in the encoders that provide you with motion feedback. EPC has been a leading designer and manufacturer of motion sensing devices for more than 50 years, we understand that each industrial automation application is different, and you need encoders that fit the needs of your applications. Our encoders are highly configurable, offer an array of shaft or bore sizes, output types, connector types, mounting options, and resolutions as high as 65,536 CPR.
Other Articles
Considerations for Choosing the Right Encoder for Your Application
Supply Chain Success in Idaho
SCARA Robot Sorts Recyclables Using a Simple Conveyor Speed Feedback System
More about Encoder Products Company
Comments (0)
This post does not have any comments. Be the first to leave a comment below.
Featured Product
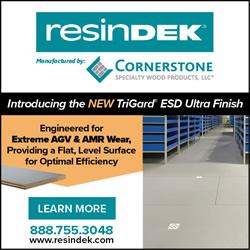