Identifying tools and techniques to eliminate Gray Work is the main objective of implementing lean manufacturing processes. The benefits for companies that successfully implement lean processes extend beyond just eliminating waste.
Lean Manufacturing and Low-Code: How to Eliminate Waste and Increase Efficiency
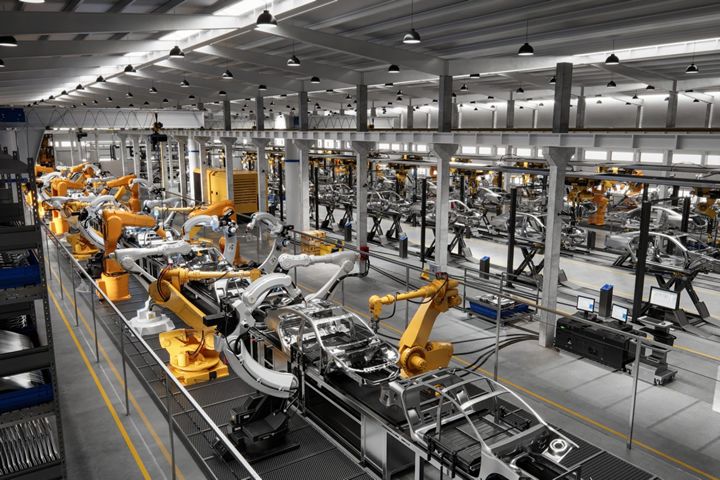
Peter Rifken | quickbase
The rapidly changing environment within manufacturing is forcing businesses to constantly deal with new challenges and complexities. In order to survive and succeed companies need to be able to find ways to increase efficiency and optimize workflow to provide the most value to customers.
However, companies that are struggling to become more proactive spend much of their time dealing with waste like defects in production, overproduction, and misused time that can lead to inefficient processes and increased costs. These instances of waste are often the result of slow, largely manual processes that bog down efficiency. We refer to this at Quickbase as Gray Work.
Identifying tools and techniques to eliminate Gray Work is the main objective of implementing lean manufacturing processes. The benefits for companies that successfully implement lean processes extend beyond just eliminating waste and can include reduced costs, improved production, and improved employee morale.
It is all too common for companies to unsuccessfully implement lean into their organization. Failed implementations can occur for many reasons including a lack of understanding of lean, a fragmented approach, and resistance to change, among others.
Low-code platforms have become more prevalent within manufacturing companies as they move ahead in their digital transformation. When deployed properly, they can help with the implementation process and pinpoint areas to improve upon from an efficiency standpoint.
In order to stay competitive, increase profits and sustain in a changing business environment, implementing lean manufacturing processes must become a strategic priority.
More Than Just the Tools
For manufacturing companies struggling with waste, decreased production, and an increasingly competitive global workforce, there needs to be a focus on optimizing workflows. Lean production emphasizes using a set of tools to identify can eliminate Gray Work and other waste from manufacturing processes in order to increase efficiency.
The framework for lean manufacturing processes is derived from the Toyota Production System which was created by the Japanese automotive company in the 1950’s and which focuses on removing unevenness in workflows.
To jumpstart implementing lean processes, manufacturing companies can start with a simple set of tools and methodologies, like value stream mapping (VSM), that are quick to implement and are able to scale. Accomplishing small wins can snowball into large cultural shifts within an organization.
But it’s not just about the techniques. Only a small fraction of lean processing is comprised of tools, technology and infrastructure. The bulk of the work with lean is in creating a mindset and company culture around it. It’s crucial that there is buy-in from the top-down in order to ensure successful implementation
Achieving buy-in requires listening to employee’s concerns and keeping them up to date on the planned changes. Some ways to achieve this are through employee pulse surveys, team meetings, and the ability for workers to submit their own questions that they have. This will ensure a smoother rollout, getting everyone on the same page before addressing areas of waste.
The most common types of waste I have observed while working with manufacturing companies are:
-
Energy, or better understanding plant assets like compressors, heaters and boilers which can be an enormous source of cost savings
-
Scrap, or material that has been tossed because of a defect or is overproduced
-
Time, or employees not working efficiently
Ultimately though, all waste leads to additional work that provides no value to the customer.
Reap Benefits with Lean Principles
While looking to implement lean processes within manufacturing there are five key lean principles that are often utilized to jumpstart the process.
According the Lean Enterprise Institute, the five principles are:
-
Identify value from the viewpoint of the customer
-
Identify the steps in the value stream, eliminating any that don’t create value
-
Develop value-creating steps that ensure smooth production
-
Establish pull so that customers are seeking out the product, rather than waiting for it, or pushing it to them
-
Continuously evaluate and assess upon these processes to continue to eliminate waste and improve
Building a continuous improvement culture in order to regularly examine processes and identify areas for further improvement is a crucial ongoing process because organizations are either improving continuously or becoming more disorganized.
Small, incremental changes, like Kaizen events or implementing a Kanban board, over the long term will only help to significantly improve processes and management. Implementing lean processes with a focus on continuous improvement can also help to determine the root cause of inefficiencies.
Successfully implementing lean processes can lead to multiple benefits beyond eliminating waste and optimizing workflow. The benefits of successful lean process implementation are well-documented; increased product quality; improved response to fluctuations in demand; and increased profits associated with improving key performance indicators (KPIs) like scrap eliminated per cycle and how long it takes to complete a specific task, among others.
There are also cultural benefits, like a sense of ownership over processes, increased productivity and engagement at the front lines.
Implementing Lean with Low-Code and Dynamic Work Management
As the digital transformation continues within manufacturing, companies are turning to low-code platforms as one way to identify and eliminate waste and improve quality. The nature of low-code tools gives anyone, regardless of their technical ability, to help directly solve the challenges they face on a daily basis.
Dynamic Work Management platforms that leverage low-code technology , like Quickbase allow users to quickly build custom software solutions to address their companies’ unique processes and challenges. Dynamic Work moves away from structured, linear workflows to a way of working that is multi-stakeholder and adaptable.
These platforms allow organizations to be more flexible and agile to respond to a constantly evolving industry in order to meet customer demand at a lower cost in a shorter amount of time.
Platforms like Quickbase play a part in helping manufacturing companies implement lean processes.
Automating key processes, centralizing data and aggregating insights via dashboards can help to reduce waste by saving time that would otherwise be spent transcribing information from paper, pencil, and spreadsheets. Simply put, a process that previously spanned 10 man-hours over three days might be reduced to two man-hours over a single afternoon.
Additionally, Quickbase allows you to track the impact of lean initiatives through features like defect tracking, inventory management, and people, skills and training management. It also helps companies continuously improve by identifying the root cause of sources of waste and managing projects to implement the countermeasure.
Utilizing Dynamic Work Management platforms like Quickbase can not only help manufacturing companies identify and eliminate waste within their organization, but also continuously improve upon those lean processes to ensure they are providing the most value to employees and customers.
The content & opinions in this article are the author’s and do not necessarily represent the views of ManufacturingTomorrow
Comments (0)
This post does not have any comments. Be the first to leave a comment below.
Featured Product
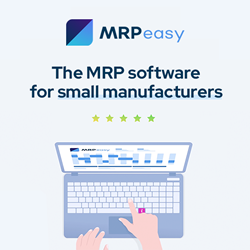