They aimed to adopt a “hub and spoke” architecture to collect OT data, analyze it locally to make improvements, and share it with centralized enterprise and cloud systems for advanced analytics, machine learning, and AI across the business.
Glass Manufacturer Modernizes Plants to Extract Value from OT Data from Edge to Cloud
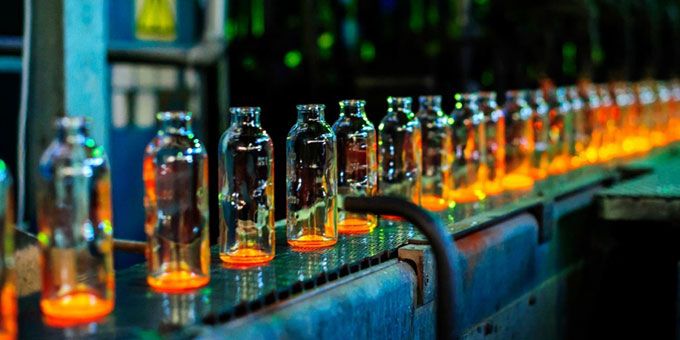
Case Study from | Cirrus Link
A leading manufacturer of packaging and glass products set out to adopt an Industrial IoT solution to modernize and standardize over 50 factories. They aimed to adopt a “hub and spoke” architecture to collect OT data, analyze it locally to make improvements, and share it with centralized enterprise and cloud systems for advanced analytics, machine learning, and AI across the business.
Project Goals and Challenges
The customer had a mix of technologies on the shop floor to start, making it difficult to collect, move, manage, and extract value from OT data. In addition to a varied technology stack at each plant, they had many different types of OT devices, sensors, and systems, with no standardized way to collect and share that data. The data they could access lacked context, so they struggled to perform any advanced analytics or data modeling which limited their ability to use data to improve operations.
The primary project goal was to adopt a “hub and spoke” architecture across all 50+ factories, which refers to a topology where data is collected centrally, in a hub, which acts as a central point of control and communication for multiple spokes to access the data. Other goals included the ability to collect OT data seamlessly, and send it to both local systems and centralized IT systems with the contextual information needed to perform advanced analytics.
The customer aimed to roll out to a minimum number of factories first, ultimately deploying the same foundational technology stack at every one of the more than 50 factories across the globe within a few years. They hoped to achieve the following benefits with the project:
- Adopt a standard IoT protocol
- Build a data standard for naming convention and modeling
- Enable the sharing of data from OT to IT
- Scale easily as use cases expand
- Ensure the security of data throughout
Implementation
The customer chose the Ignition SCADA platform as the hub, or the central control system for the deployment, due to its high-availability and robust toolset for data acquisition, real-time status and process controls, optimized HMIs, alarms, and analytics.
The chose to standardize on the MQTT protocol and Sparkplug B specification. MQTT is a lightweight publish-subscribe messaging protocol designed for efficient communication between IoT devices. MQTT is proven in Industrial IoT and met the needs of the glass and packaging manufacturer because it ensures reliable message delivery, is efficient to optimize network bandwidth, enables bi-directional communications from device to cloud and back, is secure by nature, and can scale to connect any number of data producers and consumers.
Sparkplug B is an open-source software specification that defines how to use MQTT in a mission-critical, real-time environment. The Sparkplug B specification provides the data model needed to define a tag value for use with OT, also providing data to IT, making it 100% self-discoverable and easy to consume.
With Ignition at the base of each factory, the customer needed some additional components to enable MQTT communication. They adopted Cirrus Link Modules for Ignition including MQTT Engine, Distributor, and Transmission, which enable bidirectional communication between MQTT-enabled edge devices, into MQTT infrastructure and ultimately to IT systems.
Results
With Ignition and Cirrus-Link, the customer can now push data anywhere, which in the early stages of the projects means to multiple clouds. They are testing both Microsoft Azure and AWS and considering Snowflake and other data warehouses and analytics tools.
The manufacturer rolled out to the initial factories, where each factory is running Ignition for SCADA control of manufacturing processes locally at the plant, with MQTT Modules from Cirrus Link to achieve local MQTT connectivity.
They are also using MQTT Sparkplug to send data to a central, corporate data center, then testing sending it on to cloud services for advanced data management and analytics. Sparkplug is providing them with the contextualization and modeling that will ultimately feed into cloud systems for AI and Machine Learning.
The customer is seeing early results finding datadriven insights from operational data, with plans to continue to increase efficiency and improve operations across the business as the project expands.
The content & opinions in this article are the author’s and do not necessarily represent the views of ManufacturingTomorrow
Comments (0)
This post does not have any comments. Be the first to leave a comment below.
Featured Product
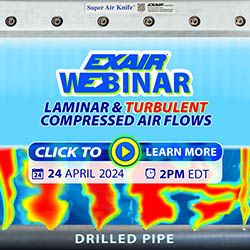