A leading plastic injection molding factory was experiencing unusually high defect rates in a specialty plastic bottle designed for the healthcare industry. They were unable to identify or determine the root causes associated with these unusually high defect rates.
Business Case for Artificial Intelligence in the Plastic Injection Molding Business
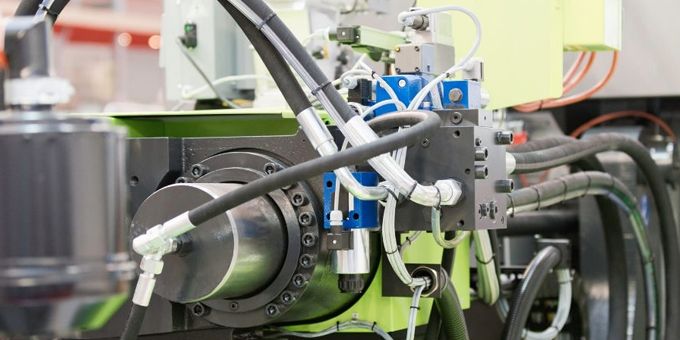
Chitta Ranjan, Ph.D., Director of Science, | ProcessMiner, Inc.
Quality Control and High Scrap Rates for an F500 Plastic Injection Molding Manufacturer.
BACKGROUND
A leading plastic injection molding factory was experiencing unusually high defect rates in a specialty plastic bottle designed for the healthcare industry. They were unable to identify or determine the root causes associated with these unusually high defect rates.
RECOMMENDATION
ProcessMiner AutoPilot™ – In June 2020, during the height of the first wave of COVID-19 infections, a well-known manufacturer of plastic bottles agreed to pilot ProcessMiner’s turn-key AI platform for their plastic injection molding operations.
IMPLEMENTATION
Positioned as a proof-of-concept, this pilot was conducted to determine whether Artificial Intelligence could help monitor, predict and prevent several common defects that were driving scrap rates upwards of 20 percent which is higher than the company average.
ProcessMiner quickly got to work studying data from more than 300 sensors on the plastic injection molding machine.
During the first 90 days of the pilot, [we] successfully gained a deep understanding of the different data parameters and the relationship they had on product quality for the bottle identified for the pilot period.
An agreement was reached to focus on two specific defect types that were driving 80 percent of the scrap for the specialty bottle being manufactured.
SOLUTION
The project began with some offline data analysis that was shared with the customer to quickly identify the relative health of data quality for the pilot machine. After learning about the manufacturing process and the importance of dominant parameter control settings, the platform quickly delivered measurable value.
Through artificial intelligence, operators were given recommendations on ideal process control settings for dominant parameters, including temperature, pressure, and dryer settings. The AI-powered ideal parameter control recommendations and the pilot were successful in a 25 percent reduction in scrap rates.
At the end of the first phase of the pilot, the manufacturer had access to real-time monitoring, predictive analytics, and prescriptive parameter control recommendations that were automatically and securely sent to the machine control system.
Next, ProcessMiner deployed AutoPilot™ – an autonomous control feature of the platform that allows parameter control changes to be made automatically on the injection molding machine using IIoT technologies.
This closed-loop approach of machines operating machines delivered improved productivity, fewer defects, better productivity, and higher first-pass yield. This reduction in defects combined with the improvement in yield drove an annualized six-figure operational savings to the manufacturing operation.
Over the course of the pilot, the platform was also successful in autonomously driving the proper center-line parameters on the machine at the beginning of each new manufacturing shift. This helped to drive down the variability that was being captured during the earlier phases of the pilot and helped the manufacturer operate in a more predictable environment.
The content & opinions in this article are the author’s and do not necessarily represent the views of ManufacturingTomorrow
Comments (0)
This post does not have any comments. Be the first to leave a comment below.
Featured Product
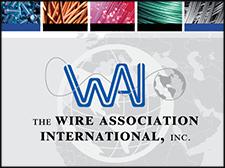