Regardless of where you are on the ISO journey – compliance, awareness only, registration, or simply trying to maintain your QMS after a successful audit - it is necessary to ensure that competence and awareness are kept at the forefront.
Competence and Awareness: How to Get Started
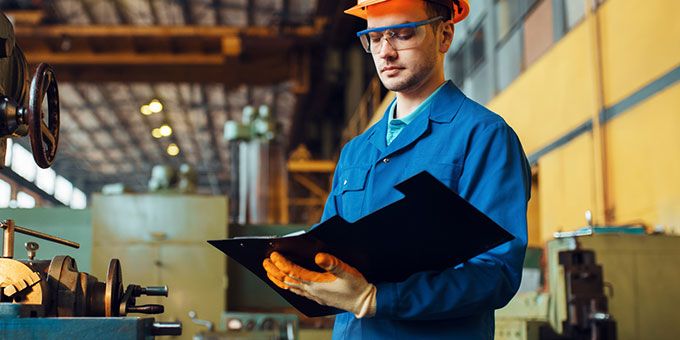
Teresa Whitacre | isoTracker QMS
ISO requires that training and competence be documented, but the standard does not give any specifics as to how do it. Not everyone in your organization needs to know every word of the ISO 9001 standard. In addition, some schools of thought suggest that not everyone even needs to read the standard. I would begin with an implementation training session. How can I expect to achieve compliance unless everyone has at least a basic understanding?
Maintaining competency, awareness and recurrent training needs
Regardless of where you are on the ISO journey – compliance, awareness only, registration, or simply trying to maintain your QMS after a successful audit - it is necessary to ensure that competence and awareness are kept at the forefront. As stated previously, there is no prescribed way to do this. You need to consider what is best for your organization.
Communication is the key. I have sent out regular companywide emails or newsletter type mailings with updates throughout the process. Something like “Congratulations to the Calibration Department on their internal audit netting zero findings.” Also “Procedures 123, Training, and Procedures 456, QMS, have been revised. You are required to read and select “read receipt” to serve as evidence of training”. I have also done this through monthly meetings with the entire staff reviewing any changes that we have had, or discussing anything new. Daily production meetings are another good communication vehicle. I have used these meetings to bring up auditor findings, corrective actions that we need to put into place, production issues, upcoming training, customer complaints or satisfaction reports.
Make it fun! Create a simple 5 question sheet to test their ongoing knowledge of a certain area. Place all the ones with correct answers aside to have one at random pulled for some sort of recognition. Put the winners name on a bulletin board or give them a front parking space for a week – anything that your organization can do to stress the importance of competence and awareness. Making it fun makes it less like work and more likely that employees will participate. I have had leadership take part in this as well. One example is a summer picnic lunch where the company leadership quizzed staff on QMS related items and rewarded them with fun things like ice cream or gas cards. We culminated the event having the highest scoring quiz “winner” get to throw a “pie in the face” of our plant manager. Adding fun to the QMS activities encourages more participation.
I have used visual displays – bulletin boards, electronic communications, and charts/graphs – anything appropriate to the organization to test knowledge. One example, I wrote the quality policy out in different colors/fonts, leaving out one word. I would ask employees what word is missing. This served as a test of their awareness. Another example involved the General Manager giving each employee a “puzzle piece: with a letter or a word from the mission statement”. Each employee would then figure out where in the puzzle their respective word would go. The employee would added the last puzzle piece or solved the “new mission statement puzzle” was awarded lunch with the senior management. This activity, coupled with the involvement of the leadership team, really helped drive home the goal and mission statement.
Leadership needs to be involved in backing the competency and awareness. There are many things that they can do to help in this endeavor. I have had leadership take the same training courses and quizzes right alongside the employees. Showing that training and competency comes from the top down helps tremendously. Leadership needs to be involved in the communications. Invite the senior staff to talk about the importance of the QMS – why it matters to them and to the business. Have them help in showing appreciation for employee competence, like some of the examples I have described herein.
Most importantly, make sure to record evidence of training, competency and awareness. ISO does not tell you how to do this, so use your creativity and ideas to make this fit your organization. I have used ranking matrices, a simple spreadsheet listing employee name, their job title, what training requirements there are, and whether the employee has met them or not. There are some training management software packages available as well to assist with this.
For competency checks, I have used quizzes, tests, or even “games” as described above. When planning and executing this, make sure to demonstrate that this competency is reviewed on a regular basis. While ISO does not specify how often, annually is a good minimum to consider.
You will be able to estimate what measures need to be taken to ensure that competence and awareness are at acceptable levels, depending on your own knowledge of your organization. Again, when there are any changes, ensure that the details are communicated, any questions answered, and training evidence recorded.
Evidence required – or it didn’t happen
If you are going through the efforts of ensuring that competence and awareness are at an acceptable level, then you will need to take credit for your work. Be able to provide evidence of the work you have done to facilitate this, as mentioned above. There is no set way that ISO requires, just that you can prove competency. Providing the auditor with documented evidence as discussed previously is vital. But outside of satisfying an audit, it will become evident fairly quickly as to the staff’s knowledge, just by observing the overall quality of the products and services you offer.
It is important that you provide guidance and knowledge to ensure that the workforce are educated and focused on the important aspects of the QMS and the 9001 standard. Given that knowing the objectives, expectations, and requirements of the standard are the fundamental starting point, there can be no continuous improvement without competence and awareness, and remember – no continual improvement means no compliance at all.
Teresa Whitacre, who writes for isoTracker QMS, is a principal at Marketech Systems and has more than three decades of experience in the world of quality management. She has worked in automotive, medical devices, electro mechanical devices and high voltage power products. She is an ASQ Fellow and a CQA, CQE, CQM/OE and CSSGB.
The content & opinions in this article are the author’s and do not necessarily represent the views of ManufacturingTomorrow
Comments (0)
This post does not have any comments. Be the first to leave a comment below.
Featured Product
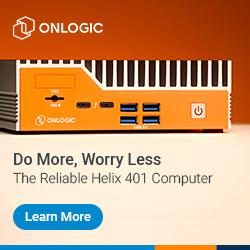