No production or logistics operations function without the extensive use of containers or load carriers. Manufacturers rely on thousands of containers to push materials and products through the supply chain.
Optimizing Load Carrier Utilization in Production and Intralogistics
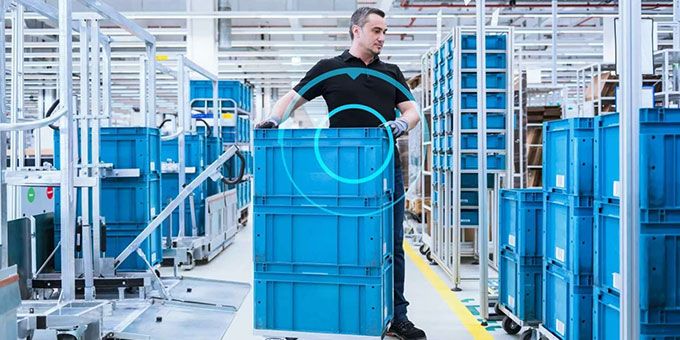
Article from | Kinexon
When a single container arrives at its destination late, at the wrong cycle, or carrying the wrong materials, it can bring the production line process to a standstill. Automated container management solutions overcome this challenge and benefit the entire intralogistics and assembly process — by guaranteeing an optimized and efficient material supply.
Leveraging location data and Real-Time Locating Systems (RTLS) creates transparency and traceability over container status and movements. This does not only optimize overall container utilization, but it prevents the all too common loss of expensive load carriers and the high-value materials they transport. The business case speaks for itself:
“By leveraging automated container management solutions, KINEXON customers were able to reduce search efforts by 35 hours per day, lower expenses for new load carriers by 22%, and reduce idle times by over 40%.”
What are the 3 key features of automated container management solutions for efficient production logistics?
- Location and status tracking:
As containers are moving through your facilities, various location technologies can track their movements in up to real time. Ultra-Wideband (UWB) tracking allows for positioning accuracy up to 10 cm, while Bluetooth Low Energy (BLE) grants precision up to 1 meter. To monitor container status, geofences can create zones in your plant’s digital twin and the application of process rules ensures automated updating of the container status as they move across the shopfloor. - Stock management:
Automated container management optimizes and monitors inventory levels in real time – in one convenient and user-friendly dashboard. Through APIs to 3rd party systems, previously manual work steps such as bookings can be executed automatically in WMS and ERP systems. This lowers overall cost because companies can lower the capital tied up in unnecessary surplus safety stocks. - Container replenishment:
Location-based process automation (LPA) can automatically trigger replenishment processes by combining position data and process rules like minimum or maximum counts of containers in defined replenishment geofences in the production or assembly area. Should quantities exceed or fall below predefined thresholds, transport orders are automatically generated and sent to employees for timely container supply.
“Your benefits through automated container management: Better processes, better customer relationships, and better bottom lines.”
Automated order management allows for end-to-end visibility in one central platform that seamlessly integrates with third-party systems. Learn more about optimizing efficiency, cost, and quality as well as implementing advanced documentation for full digital threads in intralogistics and production:
WATCH THE CONTAINER MANAGEMENT WEBINAR
The content & opinions in this article are the author’s and do not necessarily represent the views of ManufacturingTomorrow
Comments (0)
This post does not have any comments. Be the first to leave a comment below.
Featured Product
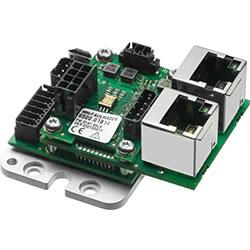