Evolving to smart manufacturing operations is not just about retooling facilities to support new equipment, systems, data and processes. It’s also very much about retooling the workforce to support digital transformation initiatives today and tomorrow.
Retooling Tomorrow’s Manufacturing Workforce for a Safer, Digital Future
Mark Brant, Head of Logistics & Retail Business Development | Nokia Enterprise
The manufacturing industry has evolved considerably in the last few years. Robots, automated guided vehicles (AGVs), IoT devices, artificial intelligence (AI) and machine learning are just a few technologies taking smart manufacturing from vision to reality. As manufacturers continue to advance towards the 5G smart factory of the future, these and other Industry 4.0 solutions will play an even greater role in manufacturing operations across industries.
But evolving to smart manufacturing operations is not just about retooling facilities to support new equipment, systems, data and processes. It’s also very much about retooling the workforce to support digital transformation initiatives today and tomorrow. With many tedious, labor-intensive tasks now automated and new systems to learn, their jobs are changing.
The good news is the wireless networks and digital technologies that drive Industry 4.0 transformation also bring key opportunities to help employees adapt to their new tasks and work in more efficient, productive and informed ways. Manufacturers that take full advantage of these opportunities will be in the best position to:
-
Increase employee safety
-
Ease employee concerns about digital transformation
-
Provide more enriching work experiences
-
Ensure employees are fully prepared to support ongoing transformation
A private wireless network powers all Industry 4.0 applications
An industrial-grade 4G or 5G private wireless network is the foundation for all manufacturing digital transformation initiatives. These networks are the only way to achieve the reliability, speed, capacity, security and low latency Industry 4.0 applications demand. Even the latest generations of Wi-Fi technology can’t meet these requirements.
Here are just a few examples of the many ways operators can leverage a private wireless network and digital solutions to help employees embrace – and benefit from – smart manufacturing transformation.
Improve situational awareness
With more vehicles, including automated guided vehicles (AGVs) and driverless forklifts, operating in manufacturing facilities, technologies that help avoid collisions with objects and people are crucial.
Adding proximity sensors and cameras to all automated and operator-driven vehicles reduces the risk of accidents. Vehicles automatically stop when they detect an object or a person. Additionally, they can use real-time video streams from mounted cameras to automatically change their route within the facility when they “see” blocked pathways ahead.
These same technologies can also be applied to wireless robots on the production line. They’re particularly beneficial for collaborative robots that interact with employees and can help reduce reluctance to partner with machines.
Accelerate detection of hazardous situations
Adding sensors to personal protective equipment (PPE) helps employees become aware of a hazardous (or potentially hazardous) situation before it affects their health. For example, a high-visibility vest could incorporate gas sensors that alert the employee wearing it to the presence of carbon monoxide or other gases before they can detect it themselves.
In manufacturing facilities that store hazardous materials, robots and drones can be used to visually inspect materials with real-time image analysis to identify anomalies. These remote inspections can be automatically executed on a more frequent schedule than manual inspections. They also allow employees to focus on lower-risk and value-added tasks.
IoT sensors that continuously monitor smart factory equipment for temperature, pressure, speed and other key performance indicators (KPIs) also accelerate awareness of potentially hazardous situations. With the real-time data these sensors deliver, employees can be immediately alerted when measurements pass pre-defined thresholds. Advanced analytics can also be applied to large volumes of KPI data to enable predictive maintenance that helps to prevent equipment faults and breakdowns.
Advanced push-to-talk (PTT) and push-to-video (PTV) services with features such as a panic button ensure employees can almost instantly share insights into any type of dangerous situation and request emergency assistance.
Manage and track access to restricted areas
A geofence creates a virtual boundary around a specific area of a manufacturing operation. Geofences can be set up for long-term use to ensure only authorized employees can enter restricted areas of manufacturing operations. Cameras at entry points can be used to automatically verify that authorized employees are wearing the appropriate PPE — a hard hat and safety boots, for example — when they enter the area.
Geofences can also be dynamically set up to restrict access to areas undergoing equipment maintenance or repair activities, or areas where a spill, leak or other hazard has been detected.
If an issue occurs within a geofenced area, operators always know who has entered and exited the area so they can be quickly located, notified and assessed for potential impact.
Enhance employee training
No matter how a digital transformation journey unfolds, operators will need to train their workforce to safely operate new equipment and systems, and follow new processes. To encourage employee engagement in new ways of working, training must be user-friendly, compelling and informative.
Virtual reality (VR) and augmented reality (AR) technologies are excellent tools to help employees visualize and adapt to their new work environment. AR and VR technologies take employees into an immersive environment that makes learning more intuitive, interactive and memorable. The military has long recognized the value of AR and VR for training soldiers. With 5G private wireless and new extended reality (XR) technologies, manufacturers can leverage these state-of-the-art training experiences to accelerate employee understanding and teach new skills.
A safer, digital manufacturing future starts today
Neither digital transformation nor employee transformation happens overnight. To ensure operations and the workforce are fully prepared for tomorrow’s manufacturing, operators should start exploring the potential for their facility and introducing employees to the opportunities and benefits now.
All of the private wireless networking and digital solutions operators need to start their journey are available today. The right technology partner can deliver the solutions, expertise and experience operators need to smoothly evolve from wherever they are today to a more efficient, flexible and productive digital future.
About Mark Brant, Head of Logistics & Retail Business Development – Nokia Enterprise
Mark Brant heads the Logistics and Retail sectors within Nokia Enterprise for the North American market. He is responsible for the identification of new business opportunities, application of Nokia’s vast technology portfolio and evangelizing the advent of Private LTE/5G technology.
The content & opinions in this article are the author’s and do not necessarily represent the views of ManufacturingTomorrow
Comments (0)
This post does not have any comments. Be the first to leave a comment below.
Featured Product
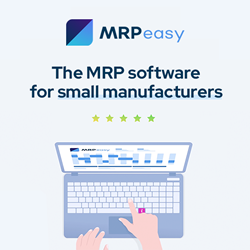