Coined by Gartner to describe one of the biggest automation trends of 2020, the concept of hyperautomation has rapidly spread across the industry. But how does it differ from regular automation.
What’s the Hype in Hyperautomation?
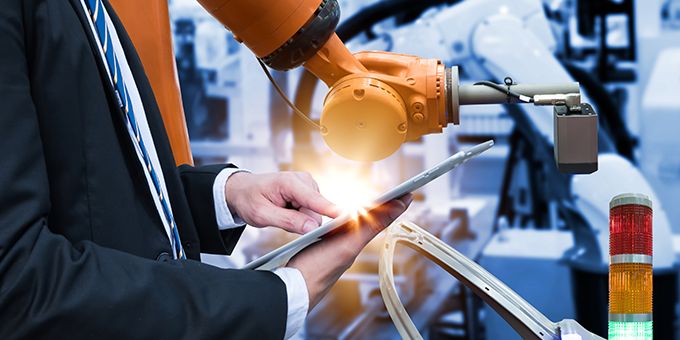
Claudia Jarrett, US Country Manager | EU Automation
In its 2019 report Move Beyond RPA to Deliver Hyperautomation, Gartner pointed out a lack of guidance in how organizations should integrate robotic process automation (RPA) with other tools. The report also highlighted that business managers experience pressure to focus on automating simple routine procedures but lack a strategy to extend automation processes to the whole factory.
The solution, according to the global research company, is hyperautomation, defined as end-to-end automation that combines complementary technologies such as deep learning, advanced analytics, machine vision, natural language processing, RPA and artificial intelligence to augment business processes.
Automation or hyperautomation?
The main difference between traditional automation and hyperautomation is that the first tends to focus on automating individual tasks — such as deploying a cobot rather than a human worker for repetitive pick and place applications — while the latter aims to optimize the whole production process with a holistic approach.
Gartner predicted that hyperautomation would be one of the top strategic technology trends from 2020 onwards, but that doesn’t necessarily mean that manufacturers must buy into the hype. To understand whether end-to-end automation can deliver substantial business value, it can be useful to create a roadmap that clearly aligns business goals with the automation tools needed to reach them.
Gartner suggests considering three key objectives — revenue, costs, and risks. With these parameters in mind, manufacturers might want to think about which technologies can drive revenue by enhancing customer engagement, increasing output, and automating repetitive tasks. They should then redesign processes to reduce the cost of poor quality and streamline production. Finally, they might need to consider the compliance risks of inefficient processes — for example, feeding parts to a machine manually might be not only inefficient but also risky, and it might therefore violate safety regulations.
What about legacy equipment?
Hyperautomation is based on the latest automation technologies available, so manufacturers might think that it is not a viable business approach for factories that use legacy equipment for critical applications.
Machines that form the backbone of factory automation, such as programmable logic controllers (PLCs), might last several decades, and there’s no reason to replace them if they still perform adequately and comply to the most recent guidelines. However, legacy equipment usually lacks the communications capabilities required to implement a hyperautomation strategy.
Luckily, if plant managers develop a solid business case for hyperautomation, there are ways to retrofit older equipment with smart sensors. In this way, the machines can be connected the to the Industrial Internet of Things (IIoT) and send valuable data that can be used to streamline operations, reduce costs, and increase productivity. An automation parts supplier that specializes in obsolete equipment can easily provide manufacturers with the hardware they need to retrofit their machines and make them fit for Industry 4.0.
Another thing to consider is whether IoT-connected machines will speak the same language. For example, the factory’s PLC needs a communication protocol that is compatible with the field devices. Manufacturers don’t necessarily need a protocol from the same brand of their PLC — for example, ProfiBus can connect with all PLCs from the Allen Bradley family, but some protocols do not play well with others. This means that to implement hyperautomation, manufacturers will have to research the best protocols to make sure that all their equipment can communicate.
When possible, developing systems based on an open-source architecture — such as the Robot Operating System (ROS) — rather than proprietary software, can help minimize frictions and ensure interoperability.
To find out more about the latest trends in automation and manufacturing, visit EU Automation’s online Knowledge Hub.
The content & opinions in this article are the author’s and do not necessarily represent the views of ManufacturingTomorrow
Comments (0)
This post does not have any comments. Be the first to leave a comment below.
Featured Product
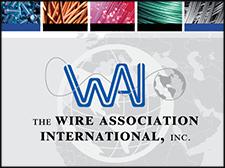