This article will be expanding on the different types of feedback devices in VFD (Variable Frequency Drives) and Servo applications, as well as some of the typical applications in which they are utilized.
An Introduction to Feedback Devices for VFD and Servo Applications
Jeff Kardell | KEB
One question that often comes up when designing closed-loop applications is, Which type of feedback should I use on my motors? This article will be expanding on the different types of feedback devices in VFD (Variable Frequency Drives) and Servo applications, as well as some of the typical applications in which they are utilized.
KEB’s S6 Servo Drive and F6 VFD both have multi-function encoder cards that have the ability to support many of the different types of feedback. The good news is KEB drives support all these encoders from one standard hardware.
What is Motor Feedback?
Let’s start by looking at an open-loop system that has no feedback. The VFD is given a speed command and attempts to run the motor at that speed by adjusting its output frequency. The advantage of this system is its low complexity and low cost. A control diagram would look like this:
Diagram of Open-Loop Motor Control.
The problem is the drive has no way of knowing if the motor’s actual speed is deviating from the intended speed. This can easily happen as the motor is loaded or if the rotor becomes locked.
We can improve speed regulation performance and even add torque control and positioning functionality by adding feedback to the motor shaft. The feedback goes back to the VFD, where the actual speed is compared to the command speed. The drive looks at the difference between these signals and tries to reduce the error to 0 by adjusting its speed controller. A basic closed-loop control diagram looks something like this:
Diagram of Closed-Loop Motor Control.
Types of Motor Feedback
Commonly used motor feedback devices can be grouped into several common categories.
Analog Feedback
Analog feedback channels are sine wave feedback signals where the analog voltage represents the shaft position. Evaluating the shaft position over time will give velocity and direction information.
Resolvers
A resolver is an electromagnetic transducer that is utilized in a wide range of position and velocity feedback applications. The main design is that it has two windings: one in the stator (non-rotating part) and rotor (attached to the motor shaft and rotates). This creates a type of rotational transformer when excited with a carrier frequency. This rotation induces two voltage signals on the stator windings 90° out of phase with each other (called sine and cosine). These signals can be read by a KEB VFD to determine the position of the motor shaft.
Resolver block diagram.
Resolvers are “old tech”, but they are often preferred because they are very robust. Resolvers are tried and true and have proven to be capable in many servo motor applications. The inductors used are epoxied into the housing, so they are very tolerant to wide temperature ranges and extreme vibration. They require no extra electronics or on board signal processing.
Sin/Cos Encoders
Sin/cos encoders are analog feedback devices that provide two signals: a sine wave track and a cosine wave track. Similar to incremental encoders, they are commonly provided with 1024 or 2048 ppr. These tracks provide position and direction information in the form of 1 Volt peak-to-peak (1Vpp) analog sine waves (typically referred to as “A” and “B”) in quadrature. The sine and cosine tracks can be sampled at high frequency, so they provide much more information than their incremental counterparts.
The high ppr and ability to sample the signal means that Sin/Cos encoders can provide over a million unique positions in one revolution of the motor shaft. For this reason, encoders in this family are preferred for precision applications.
- Sin/cos encoders are typically used on servomotors, where the higher feedback resolution is a benefit for both the velocity and position loops.
- They are available in both single-turn and multi-turn absolute variants, making them a common option for absolute position applications.
Incremental Motor Feedback
An incremental encoder provides a digital pulse for each pre-determined angular rotation of the shaft. The resolution of incremental encoders varies widely, and there are often two offset signal channels which help to establish the direction of shaft rotation.
Incremental Encoders (TTL & HTL)
Incremental encoders typically have a glass disc with a black/clear etching pattern for through-beam LEDs that become the on/off pulses as the disc rotates. In one rotation of the encoder, an incremental encoder delivers a specific number of pulses, which enables the movement value to be deduced along with the speed. Common voltage levels are 5V (TTL) and 24V (HTL). The signals consist of three tracks, track A, B, and Z (Zero signal). The A and B tracks have a 90° phase shift to indicate the rotation direction, while the zero signal (Z) track gives the number of revolutions and is useful for homing routines. Its resolution is the max number of pulses that it sends per revolution.
- Incremental encoders provide position feedback, but the absolute position is not retained when the drive/encoder is powered down.
- VFDs can evaluate the rising and falling edge of the signals to determine the direction of rotation. Monitoring the rising and falling edges effectively doubles the position information for each of the 2 tracks. Therefore, these are often called quadrature encoders.
- Incremental encoders are typically used on induction motors with indexing applications, cut to feed applications, and any speed and position type control.
- The glass disc can be a failure point in applications with vibration. Steel disc options are commonly available as an alternative.
Serial Feedback Devices
Serial feedback devices measure shaft position with analog or incremental means but then transmit the information to the VFD via a serial connection. This can reduce conductor wires in the encoder cable and susceptibility to electrical noise. Furthermore, the serial feedback devices can transmit much more information, including OEM encoder/motor parameters, error codes, and encoder diagnostic information.
BiSS Encoders
BiSS encoders are an open-source feedback interface for digital absolute encoders that was designed and developed by IC-Haus in Germany. It is capable of transmitting the position value of the encoder—and of reading or updating the information stored in the encoder. Like other digital feedback encoders (Hiperface, EnDat), BiSS comms link can be used to carry information other than position value. Additional information such as encoder resolution, manufacturer information, and temperature can be stored in a non-volatile memory area in the encoder. KEB drives can read and write to the encoder memory without interrupting real-time operations. Due to their high transfer rate, BiSS encoders can be limited on the permissible encoder cable length.
- BiSS encoders do not require additional license fees, so they provide a good value for price and performance.
Hiperface Encoders
Hiperface encoders are a proprietary hybrid feedback interface that SICK Stegmann developed in 1996. It consists of a bidirectional interface for absolute encoders, combining a digital channel for absolute position information and an analog channel for incremental position and speed feedback. The encoder also features a memory area, which is read or written to by KEB drives through a communication channel. With asynchronous serial transmission, only two lines are needed to transmit the encoder position data. The serial link requires terminal resistors to operate, along with pull-up and pull-down resistors to increase interference immunity.
EnDat Encoders
EnDat encoders are a proprietary feedback interface developed by the Heidenhain Company in the 1990’s. It consists of a bidirectional digital interface for absolute encoders. It can transmit position values from incremental and absolute feedback, transmit or update information stored in the encoder, and save new data.
EnDat 2.2 offers serial transmission; only four lines are necessary for transmitting the encoder position data synchronously with the clock delivered by the electronics. The type of transmission (position values, parameters, diagnostics, etc.) is determined by mode commands sent to the encoder (By KEB VFDs, for example).
BiSS, Hiperface, and EnDat encoders are all available in single and multi-turn absolute formats, making them ideal for applications that require absolute positioning. Typical uses of these encoders include applications such as robotic manufacturing, motion control with multiple axis, lifts, and CNC machines. When paired with a KEB drive, safety functionality with SIL3 standards is possible in applications for speed and position.
Absolute Position Feedback
Some feedback devices offer absolute position feedback in the form of single or multi-turn variants.
Absolute encoders provide a unique position value at every point of rotation, representing the “absolute” position of the encoder. From right when you switch the drive on, the absolute encoder can tell you the exact position of the shaft that it is measuring. If your machine were to lose power, absolute feedback would tell the system where it is at without having to re-home the machine. This is especially important in critical applications where re-homing procedures might take too long or lead to expensive scrap material.
Single-turn absolute feedback measures displacement over 360 degrees of shaft rotation, with the output being repeated for each revolution of the encoder’s shaft. Multi-turn encoders use a special term for each position and number of revolutions to measure the degree of rotation (within 360 degrees) and track the number of total revolutions of the encoder’s shaft. Absolute types are options within the encoder family. For example, a user could specify a single-turn BiSS absolute encoder—or a multi-turn absolute Hiperface encoder.
KEB Drives Support All These Encoder Types
Are you looking for a VFD to pair with your motor/feedback system? KEB generation 6 drives have multi-functional encoder cards that can support all of these formats. Contact an Application Engineer today to learn more about KEB’s product scope, including controls, VFDs, motors, feedback cabling, and more.
About Jeffrey Kardell
Jeffrey Kardell graduated from the University of Iowa in 2019 with a degree in Mechanical Engineering. He then joined KEB America’s application department in 2020 where he specializes in the application of KEB drive and motor technology.
The content & opinions in this article are the author’s and do not necessarily represent the views of ManufacturingTomorrow
Comments (0)
This post does not have any comments. Be the first to leave a comment below.
Featured Product
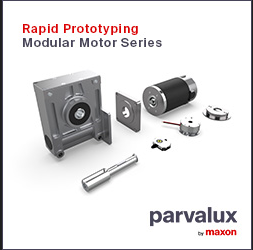