Companies will need to quickly find ways to sustain their business, mitigate all supply chain risks, and be more flexible to the new environment. These requirements will drive a need for greater visibility and control over operations.
Improving Manufacturing Operations in Response to the Pandemic
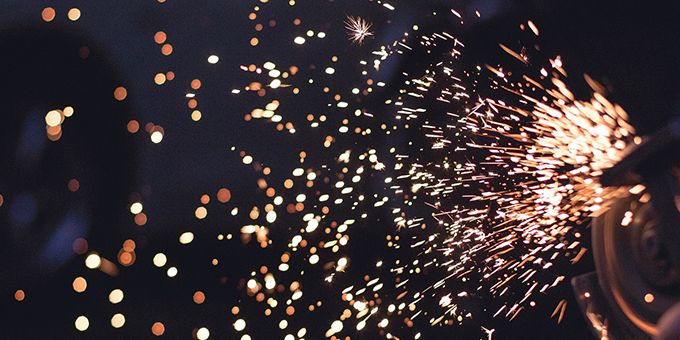
Q&A with Kenzo Takai, Director of Innovation | iBASEt
Please tell us about yourself and your role with iBASEt.
My role as Director of Innovation at iBASEt is to identify new technologies and strategies that manufacturers operating in complex, discrete industries can take advantage of to improve performance. The iBASEt Solumina platform is an ideal “enabler” to effectively deploy and maintain these innovative technologies as part of a manufacturer’s overall operations management strategy. Our most recent announcement, the partnership with Proceedix, is a great example of easing access to Smart Glasses and Augmented Reality on the shop floor.
What are some of the top challenges that manufacturers will face as they reopen operations and supplier relationship as part of the Pandemic recovery?
It seems reasonable to assume that until there is an effective vaccine identified and made widely available, manufacturers must learn how to operate with a reduced staff in order to safely maintain social distancing requirements. Employee safety has always been a top concern – no reason to suggest that will change anytime soon!
The challenges are not only the people, but all of the resources that constitute their supply chain. Companies now face unprecedented levels of supply chain disruptions. They will no longer have access to the same resources – materials, machines, and labor (including contractors, outsourcing, etc.) as originally planned.
Companies will need to quickly find ways to sustain their business, mitigate all supply chain risks, and be more flexible to the new environment. These requirements will drive a need for greater visibility and control over operations, with a much higher coordination capability over manufacturing operations across their supply chain.
How can technology be used to help overcome these operational challenges relative to social distancing and other safety measures within the factory?
Technology will be relied upon to both improve productivity of the staff that is working on site while enabling other work to be done remotely. Full staffing models might be done as a mixture of those on site, and those remote. Only then can pre-coronavirus output and productivity levels then be safely achieved. For example, investing in new automation strategies coupled with IIoT and predictive analytics could reduce repetitive, non-value-added tasks. This action could also enable other work to be done remotely, such as monitoring machines and equipment performance.
How should manufacturers begin to understand and embrace wearable technology to drive better efficiency?
Wearable technologies such as smart glasses can be an effective approach to help enforce social distancing guidelines. Employees can work more autonomously. All the work instructions support they need can be instantly available without moving. By avoiding frequent trips to and from workstations and PCs, close contact to other co-workers can be avoided. In addition, as future issues arise requiring outside expertise, this assistance can be more readily provided through virtual interfaces from subject matter experts. These actions can make sure things are correct on the spot and right the first time. This will reduce rework, maintain higher output levels and quality standards, ultimately impacting productivity and throughput.
Describe the current landscape as it relates to technology adoption and what has changed pertaining to the need for manufacturers to be nimble in the face of today’s challenges?
Manufacturers have been investing in data collection, analytics and artificial intelligence to improve data-driven decision support. In a coronavirus environment with fewer workers physically present, any technology that can ease how operations intelligence is gathered, shared, and acted upon will be highly sought after. Further, if you look at the challenge of deploying new technology, more of this will need to be done remotely. One option is for IT to start taking a role to ensure corporate compliance and to provide future support is provided, as needed.
Another change that is gaining momentum is the use of microservices, RESTful APIs, and containerizations as part of an Agile MES strategy. These technologies all help manufacturers to be nimble and respond faster to change. An Agile MES can have new features added in minutes – turned on as needed – representing a big change when compared to legacy, monolithic applications.
Has the role of analytics changed in managing through Pandemic and post-Pandemic challenges? What are some lessons learned?
The role of analytics has not changed in today’s pandemic environment. But greater reliance will be required, given that manufacturers will likely be operating with a reduced staff on site. Those employees that are “on premises” will be responsible for completing more tasks, with even less tolerance for mistakes. There will be pressure to maintain profit margins in an environment where it is harder to scale operations with fewer staff. Here the value of quick insights to support better decision making should increase over time.
From the overall supply chain view, analytics can help companies gain greater visibility and control. On the day to day operational level, it can help reduce on site people monitoring progress, letting more resources work remotely.
How might cloud technologies improve manufacturing operations in response to the pandemic?
Cloud technologies offer a way to deploy, execute, and maintain enterprise applications by remote employees. The importance of this capability might soon overcome any previous concerns over using this technology in a manufacturing environment.
Cloud technologies also offer a way to easily outsource ever-increasing complexity across operations for less cost, and with greater flexibility. Long gone are the days of having a large IT team administrating a whole set of infrastructures anymore. Cloud technologies offer not only cost reduction, but also flexibility to adjust to new business environments while optimizing the IT infrastructure landscape much easier than on premises.
About Kenzo Takai
As Director of Product Innovation at iBASEt, Kenzo Takai has a wealth of product management and solution sales experience within the discrete manufacturing industry. Previously, Kenzo has worked in a variety of high-stress, dynamic work environments where innovation and change are the only constants.
The content & opinions in this article are the author’s and do not necessarily represent the views of ManufacturingTomorrow
Comments (0)
This post does not have any comments. Be the first to leave a comment below.
Featured Product
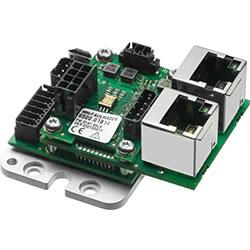