Promises of improved productivity, speed, and quality have industry leaders rushing to integrate automation, cloud computing, the Industrial Internet of Things, and other emerging technologies into workflows and supply chains.
How Machine Health Bridges Knowledge Gaps Between Automation and Aging Workforces
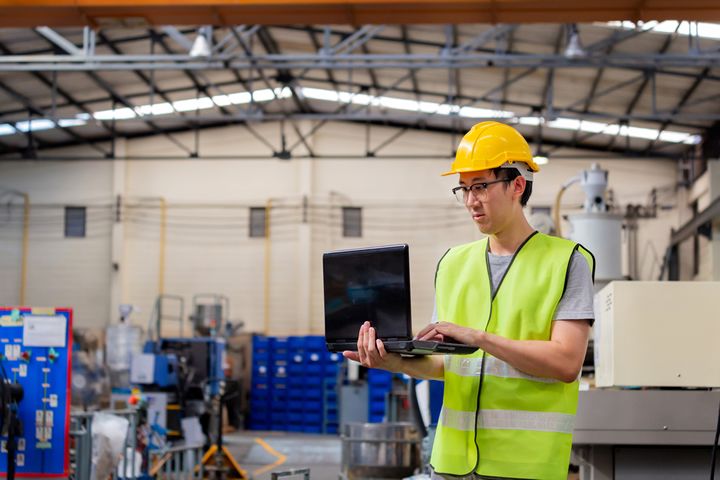
Saar Yoskovitz, Co-Founder and CEO | Augury
On the eve of the Fourth Industrial Revolution, digital machine transformation is the primary objective for many manufacturers. Promises of improved productivity, speed, and quality have industry leaders rushing to integrate automation, cloud computing, the Industrial Internet of Things, and other emerging technologies into workflows and supply chains. But as questions persist about the sector’s ability to sustain expansion, many companies are more worried about today, and rightfully so.
For an alarming number of these companies, digitalization isn’t about progress — it’s about proactive maintenance. Recently, executives from one of the world’s largest paper manufacturers told us they lose 12% of their staff each year due to retirement. They estimate that retiring employees take about 70% of their knowledge with them, which leaves knowledge gaps that must be filled.
The industry’s aging workforce is largely responsible for building the machines and processes manufacturers have relied on for decades, and artificial intelligence alone can’t replace that expertise. Manufacturing leaders must accept this reality before it’s too late.
Culture Clash
In this age of digital machine transformation, manufacturers experiencing a talent exodus face two key challenges. First, they must be able to pass on institutional knowledge so the next wave of workers can capitalize on the experience of their predecessors. Next, they must find ways to work more efficiently as staff sizes shrink. Technology can help solve both of these problems to an extent. But it also presents an additional challenge: Manufacturers hoping to implement cutting-edge automation technology need a workforce that looks dramatically different from the outgoing one.
The new age of manufacturing requires skill sets and roles that didn’t exist even a few years ago. Moreover, this shift means manufacturing leaders must focus on different metrics. Historically, leaders have maintained focus on lagging indicators that don’t allow for real-time improvements, such as overall equipment effectiveness. However, prioritizing these metrics actually creates a reactive culture. You’ve probably heard this cliche: “If it ain’t broke, don’t fix it.” That’s the modus operandi of a reactive maintenance culture — and in manufacturing, this mindset can lead to catastrophe.
Consider the following scenario: In 2017, New Orleans flooded after hours of relentless rainfall. The city is below sea level, so it relies on critical pumps to remove water from the streets and return it to the gulf. During this particular storm, eight pumps were either down for service or broken. As a result, thousands of residents faced damage to their homes and businesses.
In a reactive maintenance culture, machines work until they don’t; when the machine stops working, you know you must replace it. But as the above example demonstrates, this approach can prove costly.
Technology allows enterprises to develop a proactive maintenance culture, but they must be deliberate about it. A strong machine-health program that involves continuous monitoring enables greater agility and faster response times — things every manufacturer wants.
But how can manufacturers achieve this?
Seeing What’s Ahead
As new technology reveals important manufacturing indicators, those discoveries won’t be worth much without processes in place to track and act on them. To succeed in Industry 4.0, manufacturers must break down organizational silos and promote cross-functional teams. They’ll also need people with the skills to lead these teams — and those skills aren’t necessarily endemic to the manufacturing world.
In most modern organizations, a typical interaction between personnel from the maintenance and operations teams is tense at best.
A maintenance worker might declare: “You have to shut down. I hear a weird noise.”
The operations manager will respond: “Sorry. I have an order to fulfill. We can’t shut down until the planned outage next month.”
The subsequent conversation centers around gut feelings instead of data. And therein lies the key.
With trustworthy, straightforward, and consistent data, every department can speak a unified language. And when communication improves, companies become more agile, can practice continuous diagnostics, and gain the ability to do more with less — all things technology should enable. Toyota was perhaps the first manufacturer to adopt this way of thinking; after entering the technology space, it optimized lean production methodologies across the enterprise.
Toyota isn’t the only organization thinking smaller, though. One of our clients, a leading consumer packaged goods company, implemented its own version of a framework called “total productive manufacturing.” The approach relies on cross-functional teams and joint ownership among departments (such as maintenance, operations, and reliability). This company conducts daily standups where stakeholders open our machine analytics platform and ask: “What changed? What happened in the last shift? What can we do to ensure something happens — or doesn’t happen — in the upcoming shift?”
In short, this company found a way to continuously monitor machine-health data, which ensured proactive maintenance. But this didn’t happen merely because of our platform or any other technology — it required human action. Company leaders created a machine-health specialist role and hired an employee whose only responsibility is to monitor the data collected and insights generated by our platform. Additionally, that person ensures the company takes appropriate steps to address any maintenance recommendations.
Rise of the Robots (or Millennials)
Now that technology is ubiquitous in manufacturing, it’s time for TPM to become an industry standard. Before that can happen, however, an industrywide shift must occur. In order to lead cross-functional teams with data and analytics, leaders must understand that technology won’t replace those team members. Perhaps it’s no surprise that people who grew up with technology (and who aren’t inherently motivated to avoid it) are perfect candidates for these roles. They can fill the knowledge gaps left behind by an aging, yet experienced workforce.
Across the sector, we’re seeing a rise in Millennial employees who embrace technology and facilitate much-needed process improvements. The companies that attract young, tech-savvy employees pave the way toward Industry 4.0. Organizations that shy away from technological change continue to struggle with workforce turnover as the Baby Boomer generation retires.
Millennial manufacturing workers understand that humans still control the modern factory, mill, or plant. Still, in order to do this properly, humans need new skills and expertise. Before companies can recruit such talent, they should first look inward.
Considering What’s Inside
If a reactive culture still encumbers your organization, correcting that culture is key to attracting the right people.
For many organizations, you can find evidence of a reactive culture in machine maintenance processes. Companies that schedule equipment maintenance on a monthly, quarterly, or yearly basis are stuck in preventive maintenance mode, and that inevitably leads to problems. In our experience, the compliance rate for preventive maintenance tasks is under 40%. Sometimes, this is because employees lack discipline or the proper tools; other times, it’s because employees on the line are always putting out proverbial fires and don’t have time to perform prescheduled tasks.
Moreover, some prescheduled tasks aren’t necessary. For example, why replace a bearing that’s perfectly suitable for the job? Instead, you should assess machine health daily using a dedicated staff that conducts critical repairs and updates work orders as needed. Technology makes this possible.
Continuously monitoring machine health — rather than emphasizing preventive maintenance — gives employees time to make scheduled repairs or replacements. Ultimately, this approach sparks a positive ripple effect. When machines stop failing, workers can shift focus toward daily tasks. They also have more time to perform higher-impact work or to learn new skills that are necessary for the future.
When your best technician retires, you shouldn’t look for a replacement with the same skills and experience — and if you are, you probably won’t find that person. Instead, hire people with new skill sets who can help your organization move away from a reactive maintenance culture.
To attract and retain those people, you’ll need a culture that helps them grow. As you work to create that culture, evaluate core processes and pinpoint bottlenecks and communication barriers. Often, your approach to maintenance can provide a useful proxy for your overall company culture. If your focus is on machine health rather than predictive maintenance, you’re moving in the right direction. If you’re focused on maintenance, machines aren’t your problem — people are.
Saar Yoskovitz is co-founder and CEO at Augury, a digital machine-health company building a future where people can always rely on the machines that matter. Since co-founding Augury in 2011, he has worked with customers and partners to transform how they make products, deliver services, and improve lives through real-time insight into the health and performance of industrial equipment and systems. Saar holds a dual bachelor’s degree in electrical engineering and physics from Technion — Israel Institute of Technology. Before launching Augury, Saar worked at Intel as an analog architect.
The content & opinions in this article are the author’s and do not necessarily represent the views of ManufacturingTomorrow
Comments (0)
This post does not have any comments. Be the first to leave a comment below.
Featured Product
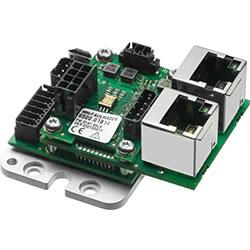