One of Industry 4.0’s key drivers is data integration. By expanding the scope of data collection and making information readily retrievable, computers on the production floor have evolved to facilitate a higher level of collaboration and innovation.
Data Integration is a Key Driver for Industry 4.0 in Polymer Manufacturing
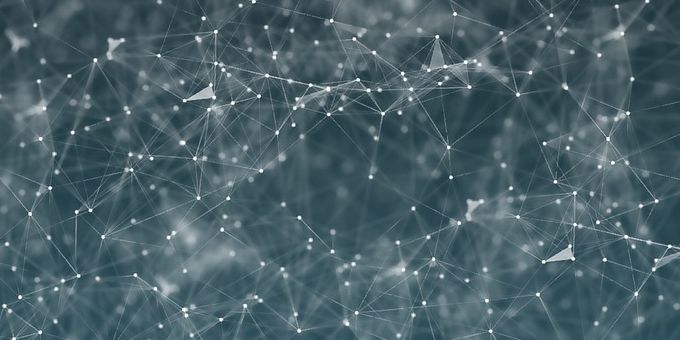
Fernando Torres, Senior Manager of Global Manufacturing Strategy | Greene Tweed
Manufacturers of high-performance polymers and components for critical applications in the energy, aerospace, life sciences, and semiconductor markets are currently adapting to leverage the new technologies of what has been dubbed the Fourth Industrial Revolution, also called Industry 4.0. One of Industry 4.0’s key drivers is data integration. By expanding the scope of data collection and making information readily retrievable, computers on the production floor have evolved to facilitate a higher level of collaboration and innovation. For example, Greene Tweed’s Industry 4.0 initiative, The Right FITT™, or Factory Innovation and Technology Transformation, creates data dashboards accessible to relevant experts at all sites.
Data integration enables collaboration
The Fourth Industrial Revolution, aka Industry 4.0, has been described as the advent of “cyber-physical systems” involving entirely new capabilities for people and machines. [1] Before Industry 4.0, computers revolutionized manufacturing in the 1970s and 1980s. Where pen-and-paper calculations and hands-on machinery had reigned since the advent of the Industrial Age, computers streamlined and transformed factory operations, providing previously unimagined levels of efficiency and precision.
Early industrial computers boosted product repeatability and production capability, but on a limited scale. Computers guided the production process, but for the most part technology controlled individual systems rather than entire networks. By contrast, the hallmark of Industry 4.0 is connectivity. Indeed, Industry 4.0’s greatest benefit to companies and their customers is that it allows all of an organization’s systems to communicate.
Data integration is considered one of the most important facets of Industry 4.0. Computers are now expanding the scope of data collection to include detailed information about all elements of each discrete step in the production process, including manufacturing and inspection, and make that information readily available to end users. With this information, computers on the production floor have evolved to provide insight and recommendations about the production process.
No longer do computers simply allow workers to perform their day-to-day tasks. Integration changes an organization’s relationship to its data in important ways. Data is easily sorted and manipulated, so patterns are more discoverable, and quickly collected for timely insights. Perhaps most importantly, data can be shared within and across teams.
This data sharing essentially equips a broader group of professionals at more layers of an organization with tools to identify and remedy inefficiencies. All employees can now predict and monitor quality and process – and seamlessly collaborate with others to make changes. Will a batch be late? Does it meet equivalency to the previous run? By revealing data in real time, Industry 4.0 capabilities replace the reactive with the proactive.
With digital inventory controls and cloud computing, for example, Greene Tweed employees can access data at any time to easily identify any equipment on the verge of developing an issue before that issue results in unintended downtime. Employees can then perform preventative maintenance to ensure maximum efficiency. Fast data about quality also allows for in-line changes during a manufacturing run.
Accessible digitalized data facilitates collaboration not only on one project at one site, but throughout an organization’s multiple locations. Many manufacturers produce similar products at separate facilities, resulting in a real risk that physical separation could impede effective communication. Greene Tweed’s Industry 4.0 initiative, The Right FITT™ or Factory Innovation and Technology Transformation, creates data dashboards accessible to relevant experts at all sites, so peers can quickly share best practices and innovations. In the context of these open channels, innovation no longer has to start and grow in a silo. Accessible, shared data allows innovative engineers working on similar projects to collaborate in real time to develop new capabilities. This, in turn, accelerates product development.
Digital data collection also aids cross-functional collaboration. In a well-designed Industry 4.0 system, the exact production history of each product is available to engineers, along with real world testing results from customers and engineers in the field. This trove of information can be used to refine manufacturing processes for the next run and for future products.
This vast and sharable manufacturing data also benefits collaboration with customers. For example, a customer may require a specific sealing solution for a new piece of equipment or a new process. Manufacturing data from previous products offers an excellent resource for communicating about requirements and capabilities. It also enables manufacturers to provide up-to-the-minute tracking of customer orders.
Data flow empowers collaboration and innovation
An updated Industry 4.0 smart factory enables not only flow of data from the floor to problem-solvers, but also quick implementation of changes – innovations flowing from the problem-solvers to the floor. With the precision and programmability of automated technology, innovations shared across teams and across facilities are much easier to implement at new sites. This advances both speed and efficacy of product development goals. Automated elements of the manufacturing floor can simply be reprogrammed with slight modifications. Then, data from the changes can be analyzed as part of an ongoing, circular process of optimization. Working in this fashion means that manufactures can quickly scale to meet their customers’ needs if production demands increase.
Forward-thinking manufacturers use Industry 4.0 to collaborate and innovate
As manufacturers of high-performance goods for strict specifications continue to embrace emerging industrial technologies with programs like The Right FITT™, the implications of Industry 4.0 for collaboration and innovation will lead to increased product repeatability and production capability. At Greene Tweed, our tradition of innovation facilitates these changes. Regardless of the specific concept guiding an organization through to Industry 4.0, leadership must clearly demonstrate vision and purpose—and trust employees at all levels to collaborate.
[1] What is the fourth industrial revolution?, World Economic Forum, https://www.weforum.org/agenda/2016/01/what-is-the-fourth-industrial-revolution/ , retrieved 7/30/19.
If you like this article you may like "Advanced Metrology Tools Enable Reliable Engine Light-Weighting"
The content & opinions in this article are the author’s and do not necessarily represent the views of ManufacturingTomorrow
Comments (0)
This post does not have any comments. Be the first to leave a comment below.
Featured Product
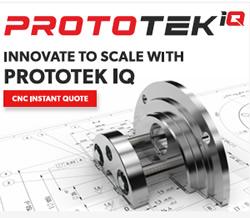