Despite the maturity of the machine tool industry, allowing for many advancements in engineering design over the span of decades, a machine is still limited by what the builder is able to implement.
The 6 Latest Trends in Direct Drive Motor Technology
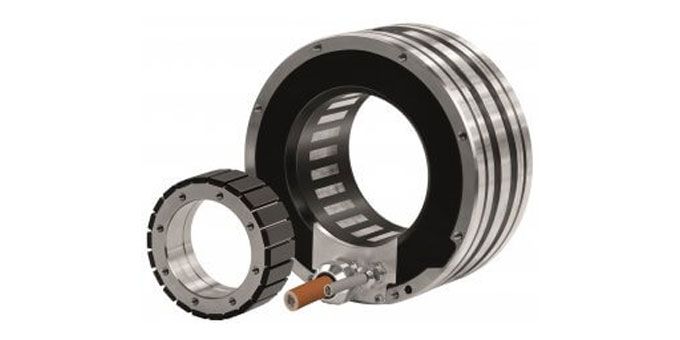
Article from | Heidenhain
Direct drive motors have always been seen as a technological step up from standard transmission devices, with torque and linear motors being seen as the higher end alternative to gearboxes and ball screws, respectively. Although the base design—permanent magnets on the rotor and copper coils on the stator—has been around for a long time, motor makers are still working on fine tuning different aspects to increase the overall performance and quality of the product. Below are six advancements that direct drive motor builders are taking to ensure the customer gets the most out of their capabilities.
1. Increases in force density
One of the key advantages of direct drive motors is the high performance they deliver relative to their footprint. Torque and force, for torque and linear motors respectively, allows the machine to take up less space overall without having to sacrifice power; and outside of the size profile, this is the most important consideration when selecting a motor. Technological advancements, a competitive environment that demands efficiency and ever-more complex parts have the machine tool industry, and in turn motor manufacturers, looking into how to maximize the force density within a volume.
A common approach is looking for ways to fit more copper coils within a volume, either with unique shapes or different proprietary manufacturing methods. The more densely packed the copper coils are, the more strands can fit, leading to an overall stronger magnetic flux. Outside of the motor itself, heat dissipation is also an area that affects a motor’s performance as the more effectively the motor is cooled the better it’ll perform. As this is a key value that’s reviwed for selecting a motor, it’s an aspect that motor designers will always work on improving through state-of-the-art designs and materials.
2. More size options
Direct drive motors are key components used in the machine tool both from a performance and product quality point of view because they need to provide the optimum power within a certain volume. Increasing geometrical variation in motor design is providing machine builders more flexibility to fit the optimum motor for a particular application in the space available while still minimizing the footprint.
For torque motors, you have the variables of diameter, length and power. But it’s not as challenging as it once was to find the ideal mix. For example, if the outer diameter of a motor is limited, then there are often many height options available to the machine manufacturer that still maximize torque.
The variety of sizes available also offers cost flexibility. For example, the ability to increase the length of a linear motor can reduce width and, in turn, the amount of costly magnet material along the length of travel. Having a large variety of sizes allows a machine maker to more easily maximize the space and efficiency of the machine, so much so that it may start to feel like the motors are made just for the machine and not the other way around.
3. Simplified integration
In-machine tool liquid cooling has become standard, and it’s not difficult to see why. Properly dissipating the heat can essentially double the torque capabilities of a motor and allow for working with a much smaller size. Still, working with liquid can be intimidating in certain applications. To help ease these concerns, motor manufacturers now often provide the option of standalone, built-in closed-cooling jackets. These all but eliminate coolant leakage and the challenge of designing optimum cooling channels. More so than ever, the responsibility to provide solutions for these issues is shifting from the machine builder to the motor manufacturer.
For linear motors, one way to simplify integration is to keep the magnetic way consistent. Things become very complex when, for instance, a builder works with different sizes of linear motors across their machine and the linear motor tracks don’t have a consistent bolt hole pattern or width increments. This becomes especially complicated if an engineer wants to upgrade the motor and she has two parts she needs to adjust. If a similar magnetic way track can be used across multiple motor models, as is possible with ETEL’s magnetic way-compatible LMG and LMS motors, it allows for easier adjustments as the motor changes. The benefit is even greater if a next-generation model can still use the original tracks, as it allows the customer to upgrade their machine with minimal effort.
4. More winding options
Although a motor may have a torque or force (e.g. continuous and peak values), it may still be limited by how much of that value is available at different speeds. Due to back-EMF voltage, Eddy currents and other factors, the greater the speed a motor runs, the lower its torque capabilities become. A common way of reducing these effects is by adjusting the winding of the copper coils to raise the speed threshold at the cost of requiring more current. This is an aspect that can be adjusted with minimal impact on the motor’s torque/force capabilities. Most motors have at least two options, but there is the possibility of having up to four, as with ETEL’s size range offering, which allows more flexibility in terms of what can be done within a fixed motor size. The idea is to propose several torque vs. speed profiles within each motor footprint in order to satisfy as many operating ranges as possible.
5. New ways of integrating
Direct drive motors have had their standard applications for a while, but as machine makers have gotten more familiar with the technology, they’ve come up with ways to take advantage of direct drive. One example of this in the traditional configuration of a linear motor, moving along a magnet track, is having the magnet piece move rather than the motor. This configuration is used to get either short, quick strokes with the magnetic way or have a single magnetic piece move across a track of linear motors. This allows a payload that is not only lighter, but also not attached to a cable, allowing freer reign when it moves.
One can also take a linear motor and adjust the magnetic way to move on a curve rather than a straight line for moving a payload in either a circle or “stadium configuration”. This not only takes up less space than a torque motor, but it’s also a more economical solution since users can avoid paying for a large torque motor with unnecessarily high torque capabilities. Combine that with the modularity of a separate linear motor that can be used in parallel, and it’s also a solution that’s easy to integrate and maintain.
6. Greater efficiency
An increase in demand for greater energy efficiency due to environmental concerns has many companies seeking out “greener” technology. Too meet these standards, motor makers have been looking into different novel design ideas to keep power losses as low as possible. This includes making the lamination stack, which the coils wind around, out of incredibly small layers (~0.1 mm) to reduce Eddy currents, utilizing Litz wires for the coil windings, and segmented magnets. Just like with increasing power density, motor makers are looking at all aspects of the materials and how they’re put together to get the most efficient performance out of the same basic design first conceived for direct drive technology.
The content & opinions in this article are the author’s and do not necessarily represent the views of ManufacturingTomorrow
Comments (0)
This post does not have any comments. Be the first to leave a comment below.
Featured Product
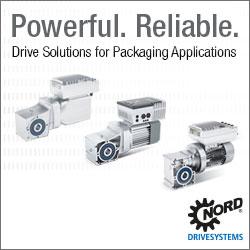