Corrosion management must move beyond its traditional maintenance strategies – corrective maintenance and periodic maintenance.
Corrosion Management is Not Rocket Science With Machine Learning
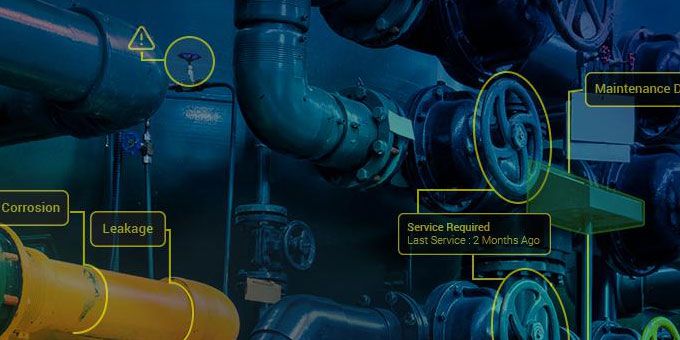
Ripal Vyas, Founder and President | Softweb Solutions Inc – An Avnet Company
Whether it’s infrastructure (bridges, railroads, pipelines), utilities (gas distribution, sewer systems, electrical utilities), transportation (ships, aircraft, cars), production and manufacturing (oil & gas, mining, food processing), or government (defense, nuclear waste storage) – corrosion management is a big problem. In corrosion management, the figure speaks for itself. Every year, it costs more than two trillion dollars across all the industries and this figure, of course, is going to increase as assets get older. In fact, the irony is, according to our world in data, the economic cost of damages from global natural disasters is 0.7 trillion dollars in the years from 2000-2018.
Corrosion management must move beyond its traditional maintenance strategies – corrective maintenance and periodic maintenance. Effective corrosion management, rather cost-effective condition-based corrosion management, is directly linked with the ability to gather and analyze a high-volume of data. Such a data-driven technology enables timely and cost-effective decision-making and this is exactly what traditional human-driven methods fail to address.
Corrosion |
|
If not detected in advance |
If detected in advance |
High frequency of production shutdown |
Reduce downtime |
Loss of product |
Improve reliability |
Loss of efficiency |
Avoid opening up of engineered systems at fixed intervals |
High maintenance costs |
Achieve overall low maintenance costs |
Loss of product quality |
Prioritize actions to maintain consistent product quality |
Reduce assets life |
Increase assets life |
Currently, non-destructive test techniques are used extensively to monitor corrosion. No production shutdown, quickness, safety and reliability are some of the advantages these techniques offer. There are various practices in non-destructive test techniques, including visual testing, enhanced visual testing, ultrasonic testing, eddy current testing, radiographic testing, infrared and thermal testing, magnetic particle testing and liquid penetrant testing. Each of these techniques has its own merits and demerits so they must be weighed carefully.
We see that enhanced visual testing is economical to perform on large areas like ships, electric poles and metal bridges as it employs digital image processing-based approaches. Various image processing techniques – principal components analysis, image restoration, linear filtering, pixelation, self-organizing maps – are used to get the base functions, such as image enhancement, noise removal, edge detection, texture analysis, color analysis, morphological functions, clustering and pattern recognition which could be combined to detect corrosion on metal articles.
The typical flow for corrosion detection using image processing is as per the following:
- Image acquisition
- Image pre-processing
- Image segmentation
- Feature extraction
- Machine learning
- Image classification
Image acquisition
The very first phase of image processing is to capture images with high resolution using a suitable camera. The images obtained can be microscopic or regular ones from drones or CCTV cameras. Here, by applying binary classification, all the rust and non-rust images are grouped as two separate sets. Although the images are grouped, such regular images can only provide gross visual characteristics such as size, depth and color and cannot tell about how severe the corrosion is. For such detailed visual inspection, it is still necessary to reduce environmental noise and unwanted reflections. Image enhancements are therefore encouraged after image acquisition is completed.
Image pre-processing
In this phase, several software filters are employed, from easy median filters to complicated filters, to determine the optimum image enhancement technique. Once the enhancement filters are decided, use a neural network method to optimize them. Following that, they are stored into a database for image processing so when the image is captured next time, it can pre-process automatically.
- Image acquisition
- Apply software filters
- Neural network
- Install filters to capture image
-
Store into database for image processing
Image segmentation
In image processing, the process of dividing an image into pieces is called segmentation. The goal of this step is to classify an image better and determine the areas that are meaningful to image characteristics and properties. Some image segmentation methods are:
Edge-based:
Apply edge extraction techniques, like Laplacian, canny edge detector, threshold the edge image and know which edges are significant, thus reducing the false hit ratio.
Threshold-based:
To extract the useful information encoded into an individual pixel – thresholding algorithm should minimize background noise, separate each peak, look for the relative size of objects and background, and the uniformity of the illumination and reflectance.
Region-based:
It groups similar components, such as pixels in an image, to obtain a compact representation using thresholding, k-means clustering. If pixels in the region are sufficiently similar in terms of intensity, color, or some other property – it suggests the presence of rusting there.
Feature extraction
It is about the ability to select key aspects of the data to produce a structured result. Decide which features to extract for further image analysis. The characteristics can be linked to color, texture, shape.
Primarily, feature extraction is based on filtering, morphology or edge-based thresholding. Widely used methods are:
Color-based:
Corroded images have an elevated red color presence compared to green and blue. However, as the color gets impacted through lighting conditions, other parameters like hue, peak value and saturation are commonly used.
Texture-based:
At distinct stages of corrosion development, the metal surface demonstrates different roughness. Corroded area pattern or texture may differ in a different region of images. Texture assessment can be used to segment corroded and non-corroded parts.
Machine learning
Based on collected image attributes, we use AdaBoost, artificial neural network and deep learning techniques to develop a machine learning model from scratch. Apart from this, we also employ pre-trained models like VGG-16, Inception v3 and more if you need results in significantly less amount of time than the models which need to be built from zero.
Image classification
Classification is the final step of image processing. Classifiers are normally categorized based on features, patterns of the corroded area or learning model to identify corroded images. Once corrosion type is spotted, the complete corrosion area is calculated to predict if the picture is partly or fully corroded to take suitable actions.
The goal here is to showcase how effortlessly and accurately a machine learning algorithm can work to monitor corrosion.
About Ripal Vyas
Ripal Vyas is the Founder and President of Softweb Solutions Inc – An Avnet Company. He has been instrumental in bringing the latest technologies to the Midwest over the last 12 years with his firm in Chicago. Vyas is now raising awareness on the importance of IoT, deep learning, AI, advance data analytics, and digital experiences across the U.S. via his new base in Dallas.
The content & opinions in this article are the author’s and do not necessarily represent the views of ManufacturingTomorrow
Comments (0)
This post does not have any comments. Be the first to leave a comment below.
Featured Product
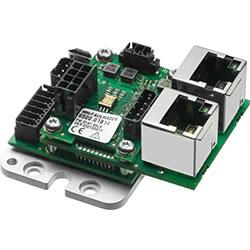