The hardware that makes up the IIoT is as varied as the data itself, and making decisions about what and how to deploy can be a significant challenge for manufacturers– especially when so much is riding on the decision.
The Role of Hardware in IIoT Deployment
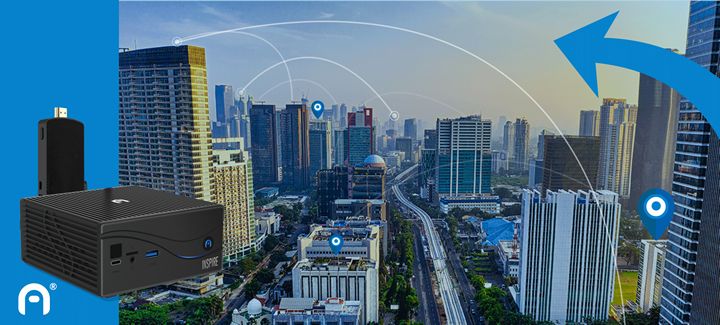
Alex Rodriguez | Azulle
Tell us about Azulle and your role with the company.
I’m the founder and CEO of Azulle, which is a leading manufacturer of mini PCs and mini PC sticks dedicated to developing and introducing practical innovations for homes and businesses. Our mission is to help customers reach their fullest potential through cutting-edge, affordable technology. All of small form factor PCs are integrated with passive cooling technology to provide a more efficient alternative to loud and easily damageable computer fans, and our PC sticks enable users to easily integrate programs and applications through technology that fits in the palm of your hand. While we work in a variety of industries, IoT is our largest growing sector.
Generally, when we discuss IIoT we talk about AI, Big Data and 5G, why is choice of Hardware equally as important in the IIoT?
Most people are focused on the software programs to create the data but gathering that data in the first place is still not completely perfected. The hardware that makes up the IIoT is as varied as the data itself, and making decisions about what and how to deploy can be a significant challenge for manufacturers– especially when so much is riding on the decision.
Deciding on the right hardware not only impacts your IoT product’s cost, application capabilities and user experience, but it also requires a different skillset to manage hardware versus the software that goes into them. You also need to make sure you’re asking the right questions to get the right type of product. For example, what type of tasks do you want the device to perform? That will then determine not only the best piece of hardware to use, but the number of sensors, the amount of processing power and the size constraints. Is the data you’re pulling sensitive and requires higher security? Then you may need hardware that is hardwired as opposed to cloud-based. A hardware specialist is imperative in helping with these types of questions and answers.
What are some of the biggest perceived barriers for those interested in an IIoT application implementation?
One of the biggest perceived barriers when it comes to implementing IIoT is cost: It’s a common misconception that IIoT can be an expensive addition to manufacturing. The reality is, there are affordable hardware options on the market in the IoT space. We believe that the key to a long-term and cost-effective solution for maintaining hardware is choosing a fanless option: warehouses and manufacturing facilities tend to be harder on hardware solutions that have fans by collecting and coating them with dust a debris. Using fanless technology in these types of scenarios will keep costs down in the long run without needing to be replaced.
Another common concern with IIoT is that it’s complicated to deploy. Many hardware options are easily customizable and connect to existing infrastructure that facilities are already using; these options mean that anything can be brought online with ease.
What are some of the most basic, yet important, qualifications to look for when considering IIoT hardware?
There are three key qualifications I would look for when deciding on hardware:
-
Flexibility: Working with companies that can adapt their hardware to your needs could be extremely important down the line. For example, if inserting a Trusted Platform Module (TPM) chip can add an extra layer of protection to your IoT platform, communicate with your supplier to see how easily this can be achieved for your business. In the IoT industry, it’s best to work with a company that can be both quick and nimble when it comes to adjusting hardware.
-
Fanless technology: Hardware that is integrated with passive cooling technology provides a more efficient alternative to loud, delicate computer fans in industrial settings. Fanless technology also requires better components that deal with variations of temperature, thus enabling the units to work better and live longer.
-
Affordability: Whether the application need is large or small, hardware cost doesn’t have to break the bank.
What are some examples of negative effects of choosing the wrong hardware in a manufacturing setting?
Some companies move forward with a massive deployment without forethought on evolution and expansion, which may mean costly replacement of hardware when you need to change a function. Before issuing deployment, you should first adopt a small-scale “test and learn” approach with hardware, so you can quickly deploy and measure the effectiveness of your program before adopting it at a broader scale.
One other negative effect not using a form factor that fits the needs for the environment in which they’re going to work, for example, not going fanless in a manufacturing setting. That means you’ll need to replace the hardware frequently, which will hurt not only your budget, but your bottom line
Finally, lots of companies put in hardware that is much more powerful than needed. Some IIoT solutions require robust hardware, however, many IIoT solutions do not require much power, they require a small amount of power and high quality devices that have a longer life span and can endure different environments. In these cases, choosing the correct hardware for the job can is the important part of this solution.
How are your products used in the Manufacturing industry?
Our products have been deployed in many industrial and manufacturing environments, and our fanless technology, form factory and customizability mean there are many creative and custom deployments for an IIoT environment: being used on robotic arms in factories, displaying real-time information on a factory floor or tracking products as they come off the line.
Can you share some use-case examples in the IIoT industry?
Azulle products have been used in the manufacturing industry in various ways:
-
To create fully-autonomous lathe machines by being the “brain” within
-
In manufacturing plants to display real-time data on the manufacturing floor
-
To connect many manufacturing machines to the company’s server systems, which can then manage all the machines remotely
-
At workstations to communicate with other team members
-
In shipping departments to connect the document processing machines for labels and pick-up tickets
Technology is moving quickly, how will Azulle keep its products relevant and evolving in this rapidly advancing environment?
One of the best things about Azulle is that our work is inspired by the needs of real people and their issues. We’re truly dedicated to developing and introducing practical innovations for businesses to use. “Technology Inspired by Real People” results in the development of practical and innovative products at reasonable prices. Azulle is dedicated to developing innovative solutions and versatile technology that fits the needs of all businesses. Our goal is to help customers reach their fullest potential by providing customizable solutions.
Based on this, our team and products uniquely nimble: if someone comes to us with a recommendation or adjustment that must be made to our products to better fit their needs, we can quickly make those adjustments for them and keep moving forward. Then, we can offer that to another customer as an additional selling point in the future. We don’t make a one-size-fits-all product. We make products to specially match what a business needs in order to be successful.
We have many relationships in the industry, like Microsoft and Intel. We are a part of their ever-evolving innovative technology, so every time something new in the industry launches, Azulle is a hardware manufacturer that has a solution. We’re also constantly meeting and creating new relationships, and I’m thrilled to see the challenges that we can face and overcome in the future with IIoT.
The content & opinions in this article are the author’s and do not necessarily represent the views of ManufacturingTomorrow
Comments (0)
This post does not have any comments. Be the first to leave a comment below.
Featured Product
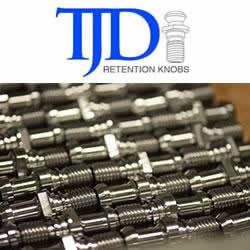