The growing number of industrialisation questions are indicative of a growing maturity in the marketplace. AM machines are moving out of prototyping applications and research laboratories and into mainstream production manufacturing.
The Business Case for Metal AM
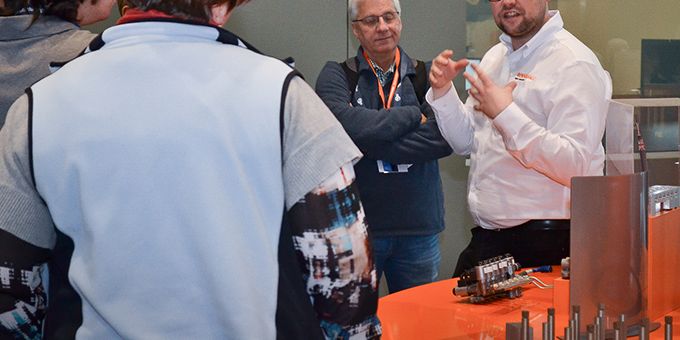
Contributed by | Renishaw
Every year, the additive manufacturing (AM) industry comes together for the Additive Manufacturing Users Group (AMUG) Conference, where attendees gain insight into the latest trends, exciting new applications and developments in AM technology. Here Stephen Anderson, Additive Manufacturing Business Manager at Renishaw Inc reflects on this year’s conference by discussing how far the AM industry has come and where it is set to go.
As AMUG was held in Chicago, USA this year, Renishaw had the opportunity to host 120 delegates before the show at its AM Solutions Centre in West Dundee, Chicago. This tour was a highlight, with very positive feedback from attendees. During AMUG another highlight for Renishaw was a Materials Parameters Development workshop, run by John Laureto and Kevin Brigden, Applications Engineers for Renishaw Inc, which was so oversubscribed that the organisers requested a third repeat. The session educated attendees on materials, process variables, scan path optimisation and how to conduct a Design of Experiments (DoE) program for best metallurgy using a laser powder bed fusion process.
A broad appeal
Renishaw also gave two main presentations. The first session, “Meticulous Machines for a New AM World,” examined how the demand for increased productivity and consistent high-quality output is driving the development of AM systems towards integrated technologies and systems. The presentation was given by Marc Saunders, Director of Additive Manufacturing Applications at Renishaw and included performance results from Renishaw’s RenAM 500Q multi-laser system.
The second, titled “To Boldly Go: Enterprising AM,” consisted of a guest panel of machine users, who shared their experiences of using Renishaw technology. This included Mike Corliss of Knust-Godwin, from the oil and gas sector and Vincent Palumbo from Mott Corporation, which specialises in using AM for industrial filtration products. It also included Khuu Phong from Dentsply Sirona, a provider of dental implants and Chris Beck from Innovative 3D Manufacturing, an AM contract manufacturer with a niche in medical tooling. This panel discussed the diverse use cases of AM, their AM successes and potential pitfalls. The audience particularly enjoyed the stories of their AM journeys and there were many questions on making AM production economics stack up.
Regularly attending AMUG has made it clear how quickly the AM industry is now moving to serial end use production. The ability to ‘grow’ a complex geometry is now well understood across the sector. The bigger conversations now are how to measure and understand the quality of parts and ensure quality is repeatable over multiple builds. This plays well with Renishaw’s core strengths and expertise in industrial process control and metrology. Renishaw is an expert in this area, pioneering developments in process monitoring technologies and software so that users can measure and understand the quality of every part.
Into the mainstream
The growing number of industrialisation questions are indicative of a growing maturity in the marketplace. AM machines are moving out of prototyping applications and research laboratories and into mainstream production manufacturing.
Where a few years ago the advice was not to print a part if you could machine it, productivity improvements now mean that many parts that could be machined are now viable for production using metal AM. This is partly because productivity advancements have made the economics more compelling, but it may be that the number of operations required for machining, compared with an all-in-one AM process, are uneconomical.
The industry must now clarify the economics further so that potential users can understand when to print and when to machine. This will help manufacturers to develop a clear business case for their application, be it for end use parts, tooling, a functional prototype or a one-off replacement part for which it is expensive to obtain tooling.
Traditional entry barriers to AM were the speed of production and variation in build quality between machines. However, the way Renishaw designs and manufactures its machines means users are growing in confidence that engineers can now expect a high degree of consistency when transferring build files from machine to equivalent machine.
AM technology is one of a number of manufacturing techniques for a manufacturer’s production line. The technology will sit alongside other manufacturing technologies and is used to produce highly complex parts, reduce mass, build hollow features, consolidate multiple components into one and to economically print parts that may be more complex to produce or require tooling, using a different method. AM has a bright future — it is now a case of opening up the market so that end users of components recognise the technology’s capability as a productive, high quality manufacturing method.
The content & opinions in this article are the author’s and do not necessarily represent the views of ManufacturingTomorrow
Comments (0)
This post does not have any comments. Be the first to leave a comment below.
Featured Product
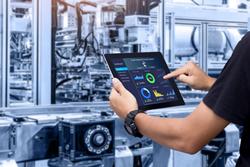