Not investing in the right lubricant is clearly a costly mistake especially if you are buying old machinery for business use. This is because a good lubricant can maximize the returns on your investment by ensuring that your old machinery runs at optimal efficiency...
Seven Key Considerations When Choosing the Right Equipment Lubricant
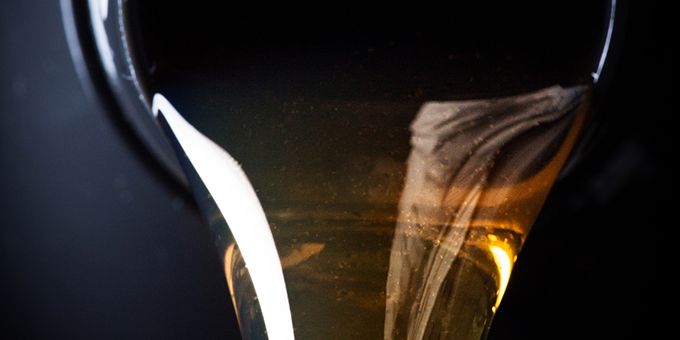
Avi Patel | Ezy Trader
The choice of lubrication plays a crucial role in maximizing equipment efficiency and it needs to be determined according to the application and environmental conditions in which the equipment is being operated, especially if you are using old machinery. Selecting the right equipment grease for maintenance functions has far-reaching benefits that include increased productivity, enhanced equipment reliability, longer service life, reduced downtime, fewer repair issues, and reduced risk of application-induced failure even if you are using second hand machinery. Made using a precise combination of formulations and ingredients, different equipment lubricants have different uses and so, a number of factors need to be taken into account when selecting the right lubricant.
Here are 7 important things to look for in a good equipment lubricant:
Cost
Cost is the single most important decision-making factor for most organizations, but the implications of selecting an inefficient lubricant far outweighs the cost savings in the long haul. Using premium-quality lubricants may be an afterthought in production facilities but choosing the right product has a positive long-term effect on the business. By selecting an affordable lubricant, operators often run the risk of shortening the oil-drain intervals which in turn reduce the service life of machinery whether it is brand new or second-hand machinery. It also increases maintenance costs, invites expensive repairs and results in unexpected downtime. Apart from this, the use of low-cost lubricants also leads to operational losses that adversely impact the bottom line of the business.
Application
The application of equipment lubricant is the second most crucial determining aspect because it takes into consideration the metals involved in the operation, the highest temperatures reached, the duty cycle and the environmental conditions. It is important to refer to the OEM manual before determining the specification of fluids (hydraulic fluid, SAE grade of engine oil, power steering fluid) used in different vehicles. It is also important to consider ambient temperatures and wet applications that require the equipment lubricant to be water resistant.
Inherent Attributes
Different equipment lubricants are specifically formulated for certain applications and so they boost equipment performance in the long run while keeping frequent component breakdowns at bay. Well-formulated lubricants are an accurate blend of additives that ensure peak efficiency even under extreme temperatures, pressures and in adverse conditions. Developed for different applications including mining, manufacturing, marine and transportation, high-performance lubricants are anti-rust, waterproof, anti-wear, and corrosion-resistant. They are chemically engineered to offer excellent stability and molecular uniformity for improved performance.
Performance Properties
Lubricants are of two types – Synthetic and mineral-based. While synthetic lubricants are formulated to hold up over longer service intervals, flow easily even at cold temperatures and maintain their viscosity during extreme weather conditions, mineral-based lubricants are easily soluble with additives, compatible with seals and relatively less costly. However, the decision should not be based on which is a better lubricant; rather it should be based on the best combination of desired properties.
Compatibility
When you mix incompatible equipment lubricants, it results in lubricant cross-contamination and this is bound to impact equipment performance adversely. You need to be extra careful with the product selection if your facility employs second hand machinery. The lubricant you choose should not only be compatible with other lubricants but also with components and seals if you want your old machinery to work well and last long.
Supplier
Now that you know how to select the right lubricant, selecting the right supplier with a good reputation is equally important. You can request the supplier for documentation that reflects the product’s performance or you can run field trials to know the best option for your business. You also want a product that is competitively priced and does not compromise on the quality. Your chosen supplier should be able to deliver products without any delay and provide prompt support for any application questions that you may have.
Operational Cost
Once you have calculated the cost of lubricant and maintenance, you need to consider the most substantial cost – the cost of operations. Any losses incurred due to unplanned downtime should be taken into account when selecting a lubricant as it can put considerable strain on the operations without making it evident. All the moving parts of the machinery must be regularly lubricated to ensure protection against a wide range of potential problems like accumulation of sludge, formation of cavities, filter blockages, pumping issues, a frequently sticking valve or premature component failures.
Not investing in the right lubricant is clearly a costly mistake especially if you are buying old machinery for business use. This is because a good lubricant can maximize the returns on your investment by ensuring that your old machinery runs at optimal efficiency without inviting unexpected repairs and expensive replacements which is often the issue faced by excess inventory buyers. Even if you are selling used machinery, the right lubricant will help keep your equipment up-to-date and fetch you a good price.
About Avi Patel
Avi Patel is an engineer by heart and a digital marketer by trade. He works for Ezy Trader and creates content on topics related to engineering, technology, marketing and trading. He has a passion for innovation and loves to share what he learns with his readers. When he's not working or writing, he can be found binge watching comedy shows.
The content & opinions in this article are the author’s and do not necessarily represent the views of ManufacturingTomorrow
Comments (0)
This post does not have any comments. Be the first to leave a comment below.
Featured Product
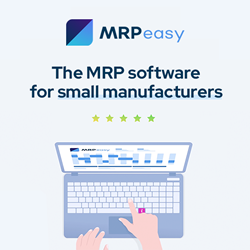