With the U.S. now imposing about $25 billion in tariffs on Chinese imports, many companies are reevaluating outsourcing—and realizing that reshoring their manufacturing processes makes sense in more ways than one.
Bringing Manufacturing Back Home
Jason Middleton | Ray Products
Everyone in the manufacturing industry knows that historically, “Made in China” tends to be more cost-efficient than “Made in America.”
With inexpensive labor readily available and far fewer regulations, outsourcing to China has long been an attractive way to decrease costs for American-based manufacturers. But with the U.S. now imposing about $25 billion in tariffs on Chinese imports, many companies are reevaluating outsourcing—and realizing that reshoring their manufacturing processes makes sense in more ways than one.
Quality Assurance
A major consideration with outsourcing is quality assurance. Even with contractual quality clauses, it’s easy for quality to degrade over time, often incrementally enough that you don’t notice until it’s too late.
This is exactly what happened to famed British car company Aston Martin in 2014. Customers began complaining about broken throttle pedals in certain vehicles, and the company’s engineers quickly identified the problem: the pedals had been manufactured with counterfeit resin instead of the factory-specified material. Determining the origin of the faulty pedals ended up being nearly impossible. Though they had been assembled by a local UK company, the counterfeit material could be attributed to one of multiple sub-contractors, none of whom Aston Martin had dealt with directly (or even known about).
Aston Martin ended up issuing a recall for 17,950 of its vehicles, and while the financial implications of this recall were certainly not irreparable, it’s an excellent example of how a complex overseas supply chain maze can fundamentally impact the quality of a finished product. Generally speaking, it’s much easier to monitor quality and sub-contractors when they are operating in the same hemisphere (and under the same regulations) as you.
Hidden Costs
While the fixed costs of offshore manufacturing are often lower than the domestic alternative, there are a host of hidden costs that come along with outsourcing, including shipping and transport, legal fees, quantity penalties, and more.
Getting products from overseas to your company (or to consumers) can be unexpectedly costly and time-consuming (often 2-3 months). If not carefully researched, the added cost of transport, lag time or unexpected shipping delays can add up.
When it comes to the complexities of regulatory and trade standards, both here in the U.S. and abroad, manufacturers with considerable outsourcing experience highly recommend engaging a lawyer with international business experience. Some also advise working with a lawyer in the offshore manufacturer’s country to ensure compliance with those regulations. Both of these, while undoubtedly worthwhile investments, could easily add up.
Finally, cost savings from offshore manufacturing are often dependent on large quantity production, so manufacturers with a smaller production yield may see little in the way of cost savings.
Ultimately, at face value, offshore manufacturing can be less expensive than domestic manufacturing—but this is often only true initially. And, importantly, with that short-term gain comes an inevitable long-term loss: visibility around who is manufacturing your parts or products — and how they’re doing it.
The Current Climate
It’s unclear how the ongoing trade war with China will net out, but with the U.S. imposing approximately $250 billion in tariffs on Chinese imports, many manufacturers are discovering that it is no longer cost-effective to source products and materials from China. As these manufacturers begin to evaluate reshoring their manufacturing processes, they are learning what many of us already know: when it comes to manufacturing, less risk, more control and greater visibility are ultimately better for business.
The content & opinions in this article are the author’s and do not necessarily represent the views of ManufacturingTomorrow
Comments (0)
This post does not have any comments. Be the first to leave a comment below.
Featured Product
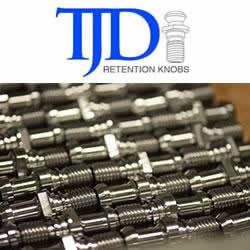