NASA has successfully tested its first rocket engine component made through 3D printing. The 3D printed component produced a breathtaking 20,000 pounds of thrust.
Top Article from 2019 - Can a 3D Printer Build a Rocket?
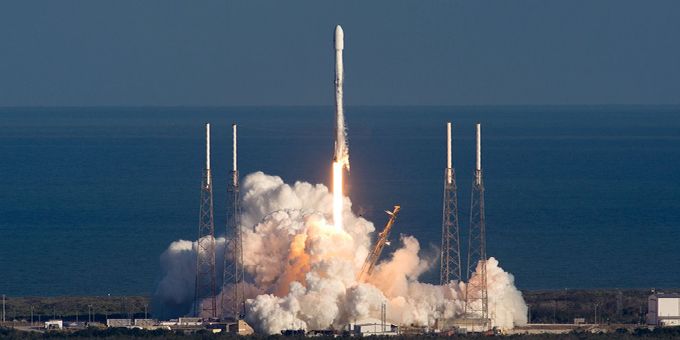
Len Calderone for | ManufacturingTomorrow
3… 2… 1…Blast off! The rocket slowly lifted from the pad and picks up speed as it soars into the cerulean blue sky.
Rocket Lab, a Silicon Valley-funded space launch company, launched the maiden flight of its battery-powered, 3-D printed rocket from New Zealand’s remote Mahia Peninsula. Space was its objective and it made it.
This successful launch used a low cost, 3D-printed rocket. The objective was an important phase in the commercial race to lower financial and logistical barriers to space. The company claims its service is a way for companies to get satellites into orbit consistently.
Their emphasis is to develop a reliable launch vehicle that can be manufactured in high volumes with the goal to make space obtainable by providing exceptional frequency of launch opportunities, using their Electron vehicle.
Electron, a two-stage orbital expendable launch vehicle, uses two types of engines. Rocket Lab’s Rutherford liquid-propellant engine asserts two unique firsts. The first being an oxygen/kerosene engine, which uses 3D printing for all of its primary components, and a battery-powered rocket engine, which is a first.
The engine is pump-fed liquid fuel by dual electric motors and a lithium polymer battery, which reduces the need for heavy pressurized fuel tanks. Because of this, and the particular 3D-printed processes of the engine, it weighs only 77 pounds without fuel, reducing the cost of a launch. The engine is used both as a primary and secondary stage engine.
The second engine is the Curie, which drives the launch vehicle's specialized "kick stage”. The kick stage reorients the rocket once it has reached the highest point in its elliptical orbit, allowing it to launch its multiple satellites with extreme accuracy into their desired orbits. The engine can reignite multiple times to let the launch vehicle place its payload so that they orbit at a safe distance from each other.
Relativity Space, a L.A. company, has built the world’s largest 3D metal printer called Stargate. Stargate uses sensors and function-based learning to print rockets made of stronger, reliable alloys. This 3D printer is giving Relativity Space an advantage in conjunction with an in-house metallurgy and material characterization lab. This new process to build rockets will redefine how we go into space. They can build rockets and launch them in days instead of years.
The advantage of using a 3D printer to build a rocket is a lower cost and the ability to build rockets much quicker. Relativity takes only 60 days to develop an entire rocket while it usually takes other companies 24-48 months. The company is entirely self-sufficient printing 95% parts of the rocket in-house, while the other 5% consists of electric cables, chips, or rubber parts.
Presently, it takes around $100 million to manufacture and send a rocket into orbit. In the next four years, Relativity plans on reducing the cost to $10 million by utilizing the power of 3D printing.
3D printing is good at producing highly complicated shapes. This establishes the opportunity to produce improved, lightweight parts that were formerly impossible to manufacture economically using more traditional techniques.
3D printing can also reduce the amount of material wasted during manufacturing. The components used in rocket manufacturing are made from extremely expensive and often rare materials. 3D printing can also build whole systems non-stop rather than from many assembled parts.
Once in space, replacement parts may be needed but it is too difficult to keep an inventory or send these parts into space. Therefore, we will see 3D printers used in space, such as in the International space station where if something breaks, engineers on earth can send up a design for a replacement and the astronauts can print it out.
Recently, we've seen an enormous amount of private money being spent on small satellites. Until now, space was solely the domain of governments, but now it's moving into private commerce.
NASA is being enticed to embrace 3D printing because of lower costs and shorter production times. An engine injector made with conventional fabrication techniques of molding and welding costs around $250,000. 3D printing will reduce that cost to about $25,000. Production time can be reduced from six months to just weeks.
A conventional injector design contains around 300 parts, but 3d printing could build it as a single unit. Production would not only be faster and cheaper, but safer. It reduces the number of individual parts that could have manufacturing defects. It also saves time inspecting for such flaws.
The injector was manufactured using selective laser melting. This method built up layers of nickel-chromium alloy powder to make the complex, subscale injector with its 28 elements for channeling and mixing propellants. Because the new rocket injector was made using laser sintering, designers were able to reduce the number of parts.
SLM components will not have to be welded together. Normally, welds are a weak point, therefore, the elimination of welds is a good thing. NASA will test the new components to see how they hold up against extreme heat and vibrations.
NASA has successfully tested its first rocket engine component made through 3D printing. The 3D printed component produced a breathtaking 20,000 pounds of thrust.
In little more than a month, NASA engineers at the Marshall Space Flight Center in Huntsville, Alabama built two subscale injectors with a specialized 3D printer and completed 11 mainstage hot-fire tests, accumulating 46 seconds of total firing time at temperatures nearing 6,000 degrees Fahrenheit while burning liquid oxygen and gaseous hydrogen.
They saw no difference in the performance of the 3D printed injectors as compared to the traditionally manufactured injectors. Two separate 3D printed injectors operated magnificently during all hot-fire tests. The post-test inspections indicated that the injectors remained in excellent condition and performed so well that the team will continue to place them in the line of fire.
Satellites have dramatically become smaller as technology has improved. They are no longer the size of a truck, but more like a toaster. As a result, there has to be smaller rockets so that these satellites can be placed where they need to be when they are needed, instead of being a subordinate passenger on a larger rocket. At present, there is a huge backlog of these small satellites; so, 3D manufacturing of rockets is off to a good start.
The content & opinions in this article are the author’s and do not necessarily represent the views of ManufacturingTomorrow
Comments (0)
This post does not have any comments. Be the first to leave a comment below.
Featured Product
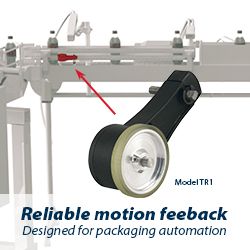