In the next 10 years, 4.6MM manufacturing jobs will become open and only 2.2MM are likely to be filled. As this skills gap widens for manufacturing firms, it's going to be critical to run their organizations as efficiently as possible.
Interview with FactoryFour Co-Founder & CEO Param Shah
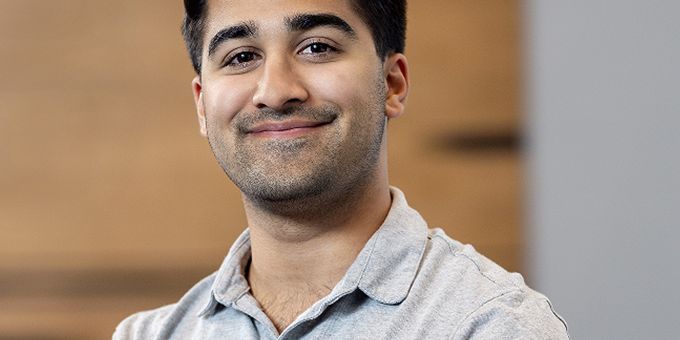
Param Shah | FactoryFour
You recently announced a $5 million Series A round led by August Capital, how will this money be used?
We plan to use this money to further expand our world class engineering team, bring more robust support operations to clients across the US and Europe and expand our product offerings. This investment is a great opportunity for us to solidify our position as an industry leading tech provider for manufacturers across all industries and product types.
Why do you feel it is so important for manufacturers to better streamline, track and manage their production?
In the next 10 years, 4.6MM manufacturing jobs will become open and only 2.2MM are likely to be filled. As this skills gap widens for manufacturing firms, it's going to be critical to run their organizations as efficiently as possible. In addition to dealing with hiring issues, a clear inefficiency in many manufacturing firms, both small and large, is the lack of ability to track real time data across their production environments. Being able to reliably track progress towards corporate goals is also a vital tool in optimizing production processes and operations.
Tell us about FactoryFour and how it came to be. What inspired you to start your own company? What does it take to build your own startup?
FactoryFour came about when our founder was running a nonprofit to build and distribute orthotics to children in third world countries. He noticed that there was a significant lag between getting the required measurements, creating the needed item and getting it to the patient. Out of solving this issue, FactoryFour was born.
Give us your best piece of advice for someone looking to launch a startup?
When you’re thinking about launching a startup, the best thing to do is to just get started. Actually, committing time and energy to your idea is the most difficult part of founding a startup. Anyone can think of the next great idea, but taking the next step of building on it is what matters. You have to trust yourself and take the leap. Once you do, hold on to that confidence in what you’re building because that’s what will carry you through the inevitable tough times and allow you to inspire your team to push themselves harder in the good times.
What makes FactoryFour unique from all other manufacturing companies? What are you doing differently?
FactoryFour is different from everything else in the manufacturing space because we can create value and efficiencies across all forms and types of manufacturing. From eyewear to orthopedics, we are able to quickly integrate with existing processes and workflows to generate data and insights to improve your manufacturing environment from Day 1.
What’s something you want our readers to know, not only about your company, but about manufacturing in general?
Manufacturing has steadily become more advanced with innovation in technology occurring constantly. While that opens up the possibilities for goods to be produced more efficiently, it dramatically increases the complexity of the modern manufacturing ecosystem. While manufacturers are eager to adopt new machines and techniques, there has been little to no progress in what tools manufacturers can use to manage their production, leading to much of manufacturers being tracked with basic tools like pen and paper or spreadsheets. FactoryFour brings this data under control and allows managers to gather useful insights on their production.
Where do you see the company in the next 5 years?
Right now we focus highly on order intake and work in progress since they are often the most complex yet neglected aspects of a manufacturer’s business. Over the next 5 years we expect to grow beyond our current scope to other parts of the manufacturing ecosystem. We will take our same innovative approaches to user experience and data to places like inventory, accounting, and workshop IoT technology, becoming the hub for all manufacturing management.
The content & opinions in this article are the author’s and do not necessarily represent the views of ManufacturingTomorrow
Comments (0)
This post does not have any comments. Be the first to leave a comment below.
Featured Product
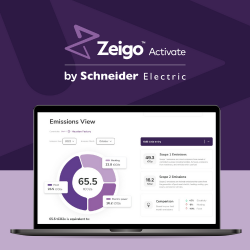