The manufacturing industry is facing a hiring crisis. According to Deloitte, by 2025, the manufacturing skills gap will result in a need for 3.4 million skilled workers, and 2 million of those roles will go unfulfilled.
AI's Role in Overcoming the Manufacturing Hiring Crisis
Prateek Joshi | Plutoshift
Is there a hiring crisis/shortage in manufacturing?
The manufacturing industry is facing a hiring crisis. According to Deloitte, by 2025, the manufacturing skills gap will result in a need for 3.4 million skilled workers, and 2 million of those roles will go unfulfilled.
These numbers are the result of 2.7 million of the current manufacturing labor force retiring by 2025, in addition to the 700,000 jobs that will be created by growth in the manufacturing industry.
Why might Millennials and Gen Zers not be interested in working in manufacturing?
The manufacturing industry will attract Millennials and Gen Zers, but the job profiles to which they will be drawn will be very different than factory floor management. The younger workforce is used to getting everything on demand, including the information needed to perform their jobs. Digitization of various parts of the manufacturing business is a step in this direction.
There exists a widespread misperception that manufacturing jobs are at risk due to automation and robots, which is just not the case. We still need humans to digest the large amounts of data generated from manufacturing processes to figure out how to do things faster, better and cheaper. In order to digest this data, we need to convert it into human readable information.
Is there truth to the notion that AI will replace jobs in manufacturing? How can AI in manufacturing save jobs rather than replace them?
No. According to recent data from AT Kearney/Drishti, 72 percent of manufacturing jobs are still performed by humans and those humans drive three times more value than their automated counterparts. While more parts of the manufacturing process are becoming automated, nothing will replace human judgement and intuition.
AI, Machine Learning (ML) and automation will create jobs because of the specialized skill sets required to support these technologies. Just because a factory implements these technologies, doesn’t mean that they just run by themselves. We need employees who can use this information and take action. In fact, a PwC report from this past summer stated that AI and robotics will create a net gain of 200,000 jobs in the U.K. by 2037.
How can working with AI actually attract younger candidates?
Younger generations are growing more interested in careers in science and engineering. According to the National Science Foundation, a third of bachelor's degrees earned in 2012 were in science and engineering majors, in addition to 58 percent of doctorates awarded in those fields.
With more students showing an interest in science and engineering, pursuing careers in advanced technologies is a logical progression. As AI and ML continue to mature, we can expect to see them become mainstream components of technology-focused college curricula.
AI and ML are seen as cool, new innovations that draw the interest of a generation of young adults, most of whom have grown up with modern technologies that have already played a large role in their daily lives.
Do you have any thoughts on how we will educate people for the new roles with Robotics and AI? Trade schools, universities or the manufacturers themselves?
This transformation is similar to the industrial revolution where a host of repetitive and hazardous jobs were replaced by a larger number of ones across various departments designed to increase throughput and visibility.
AI converts large amounts of raw data into something a human can read and interpret. In the absence of that, the human has to learn how to gather data from multiple database systems, connect them together, know what insights to look for, extract them manually using spreadsheets, and then interpret the results. This whole process is tedious and error-prone. By the time they get there, they won’t have any time or patience to analyze what can be done with that information.
In the presence of AI software, the same human can instead spend that time interpreting the information extracted from that data. They can now figure out ways to ensure smooth operations and get ahead of potential issues that will disrupt the production process. Manufacturers should educate their employees on how to interpret information extracted from data. This will prove a key driver of this transformation.
Why is AI a critical part of manufacturing’s future?
The sheer volume of data generated by the manufacturing industry is immense. There is no point in gathering data if you’re not going to gain actionable intelligence from it. It is imperative that organizations know if their machines are consuming too much power, or are trending toward a malfunction - as indicated by conditions such as pressure, temperature and velocity - resulting in costly downtime. However, there is just too much data for any person or team of people to analyze and this is where AI is very much needed. AI and ML were made to analyze seas of information and identify the trends within them that help business leaders make more informed decisions.
Organizations are constantly looking for ways to improve efficiency. The intelligence generated by AI solutions is critical to operating a lean running facility and addressing issues proactively. The longer an issue persists, such as a machine running at less that optimal capacity, the more money a manufacturer wastes. AI is already helping organizations stay ahead of their assets’ performance and make a meaningful impact on their bottom lines.
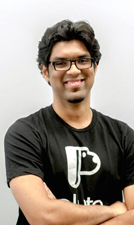
Prateek Joshi is the founder and CEO of Plutoshift, which provides asset performance management solutions to process industries including water, food, beverage, and chemicals. He is an Artificial Intelligence researcher, the author of eight published books, and a TEDx speaker. Prateek has been featured on Forbes 30 Under 30, CNBC, TechCrunch, and more.
The content & opinions in this article are the author’s and do not necessarily represent the views of ManufacturingTomorrow
Comments (0)
This post does not have any comments. Be the first to leave a comment below.
Featured Product
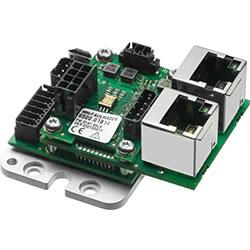