Emulate3D's focus at IMTS will be the demonstration of the new CAD is the Model technology for machine builders, but we will also be showcasing Emulate3D Controls Testing for larger systems
Ian McGregor | Emulate3D
Tell us about your company.
Emulate3D develops engineering software designed to improve and accelerate automated system design and testing. Users create dynamic digital twins of existing or proposed projects in order to understand and improve throughputs and system operation, as well as reducing commissioning time and costs at implementation.
All models built with Emulate3D technology can be experienced, operated, and shared using virtual reality, augmented, and mixed reality devices.
Your company will be exhibiting at IMTS, what is it that makes this an important event for your company?
Emulate3D is launching Controls Testing for Machine Builders at IMTS this year - we've taken our powerful virtual commissioning technology and integrated it within SOLIDWORKS so that machine builders can mark up their CAD using a company-specific addin ribbon and generate a working emulation model from their familiar CAD environment.
This step shortens and simplifies the model build and makes the benefits of the technology available to a broader range of users. This technology is known as CAD is the Model, and enables users to continue to modify their design and generate the virtual commissioning model at the touch of a button.
Highlight a 2 or 3 products you will be showcasing at the event?
Emulate3D's focus at IMTS will be the demonstration of the new CAD is the Model technology for machine builders, but we will also be showcasing Emulate3D Controls Testing for larger systems, our widely employed flagship technology which takes controls debugging off the automation project's critical path and generates significant savings for users at the FAT and commissioning phases of their projects.
Emulate3D Virtual Reality technology will also be on show - it is an ideal way of familiarizing operators with the sequencing and timing of the machine or system, without disrupting real production. Wherever the operation of system prototypes need to be demonstrated to prospects, fully-interactive CAD-based Virtual Reality models are a cost-effective and rapid alternative to building a physical prototype. The Emulate3D booth will feature an interactive machine prototype that attendees can try out for themselves.
IMTS has many educational sessions & Demo’s, is your company involved in any of them this year?
The Emulate3D booth will be set up to demonstrate our products fully and educate attendees in the opportunities presented by our Dynamic Digital Twin and Virtual Reality technologies.
When you get a chance to walk the exhibit hall floor yourself, what is it you will be most interested to see? Any educational sessions you plan on attending?
I'll be looking for new machine and material handling innovations as well as useful IIOT implementations, and talking with exhibitors about successful implementations of their technologies.
When you book a booth for a tradeshow like this what are your expectations and what does your company hope to accomplish at the event?
At Emulate3D we find that trade shows are the best way to introduce our technology to new users - as our products are very visual and dynamic, we get extremely positive reactions from attendees experiencing them for the first time. Booth visitors bring their company perspective and experience to the show and often surprise us with their insight and implementation suggestions. Trade shows are a great place to initiate the long lasting relationships we create with our users.
A tradeshow of this magnitude is extremely busy and stressful for the staff of exhibiting companies. Any fun things or places your team can suggest in Chicago to help unwind?
We've been going to trade shows at McCormick for many years now, and we rent a house just north of the Lincoln Park area, which means we are well placed for the Kingston Mines, a great blues club where two bands take turns to play sets in adjoining rooms every night. So it doesn't matter what time you turn up, you can always get a seat at the front by waiting for the next set to start. Buckets of beers and other beverages are brought to you by very attentive staff, so you don't even need to line up at the bar.
Featured Product
Emulate3D Engineering Software Creates Your Advantage
Emulate3D software helps you model and test your AMHS solutions rapidly. Use Demo3D to create running models quickly, then generate videos, stills, or view the models in virtual reality at the click of a button. Sim3D enables you to carry out experimental test runs to select optimal solutions and the most robust operating strategy, and Emulate3D Controls Testing is the best way to debug your PLCs offline, and off the project's critical path. Connect to major PLCs, import CAD, and plug into HTC Vive and Oculus Rift to produce awesome models!
The content & opinions in this article are the author’s and do not necessarily represent the views of ManufacturingTomorrow
Comments (0)
This post does not have any comments. Be the first to leave a comment below.
Featured Product
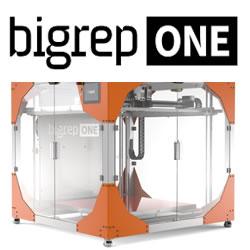