Flexible hone provides fine surface finish for internal bores, along with edge breaking of undercuts and deburring of intersecting drilled holes.
Versatile Abrasive Tool for CNC Machining Decreases Cycle and Finishing Time
Contributed by | Brush Research Manufacturing
For contract part manufacturers, the ability to produce tight tolerance parts at a faster rate is the key to remaining profitable in a crowded, highly competitive market. To do this, machine shops constantly seek out creative ways to improve on overall cycle time, including speeding metal finishing operations.
Although machine shops may have some auxiliary finishing equipment, the primary focus is on the machining. As a result, many shops must send parts out for secondary finishing steps such as thermal deburring, tumbling and burnishing.
However, for job shops like Wolfram Manufacturing, a company that machines metal parts with complex geometries on 4 and 5-axis machines, sending out parts for secondary finishing not only adds to the cost, but can impact quality and increase the time it takes to deliver the parts to customers.
“There’s the additional time, not to mention the additional cost of having someone else do the work time. In the competitive environment today, we’re often faced with short lead times from customers,” says Tim Urano, Quality Manager. “Having to send parts to an outside vendor eats into our lead time and takes significant planning.”
A better alternative for many machine shops, says Urano, is to incorporate machine tools that can complete the finishing tasks within the machining process.
“Any time we can incorporate secondary operations right into the machining process, we save time, money, and reduce our work in progress,” adds Urano.
In one example, Wolfram Manufacturing was charged with making a unique part for a sliding valve assembly with complex internal geometries that require a high surface finish on the internal bore and the elimination of any sharp edges from drilled holes.
Sliding valves, which are movable elements in a system, are used to direct the flow of a working fluid into the proper channel. The assembly is part of a larger product used in pressurized down-hole drilling tool.
To operate properly, the valves utilize O-rings that must be seated properly and maintain tight contact with the bore without getting cut by any sharp edges from intersecting holes or undercuts.
“The customer’s primary concern is that the O-ring seal is protected from being cut or damaged by any sharp edges or burrs,” says Tim Urano, Quality Manager at Wolfram Manufacturing. “It is one of the main reasons we use the Flex-Hone Tool.”
The Flex-Hone, from Brush Research Manufacturing, is a highly specialized abrasive tool characterized by the small, abrasive globules that are permanently mounted to flexible filaments. Available in many sizes, abrasive types and grits, the tool is used for deburring, edge-blending, cross-hatching, and removing cut, torn or folded metal.
“It’s very easy to put the flexible hone in a toolholder, give it a simple toolpath cycle and let it run. With some of the other in-machine deburring tools it can take complex 4-5 axis paths to be effective,” explains Urano.
To satisfy the customer’s requirements, Wolfram Manufacturing had to reliably remove burrs and sharp edges in cross-drilled holes and other difficult-to-access areas such as undercuts.
“The part has some undercuts and some intersecting cross-holes so we use the tool to edge break and help blend the chamfers at the same time,” says Urano. “The hone is one of the only tools that can reach that edge. It doesn’t alter the feature geometry, but it rounds it enough that it won’t damage the O-ring.”
A high surface finish is called out on the internal bores where the valve assembly actuates. As part of a multi-step process, Wolfram Manufacturing utilizes a coarse grit Flex-Hone to smooth out any irregularities left during drilling and finishes the bore with a fine grit hone.
“Final finishing operations don’t accommodate much variation, so they need the uniform surface preparation that the flexible hone provides,” explains Urano. “By using these tools, we can achieve more consistent results.”
While FlexHones are often used with automated production equipment, they can also be used for offline deburring. If during post-processing or inspection any damage occurs to the bore finish, Wolfram is able to go back in with the hone and clean it up.
Urano adds that Wolfram Manufacturing will continue to use the brush, “Whenever we see applications with intersecting holes, or particular surface finishing requirements in a bore, it’s one of the first tools we will go to.”
The content & opinions in this article are the author’s and do not necessarily represent the views of ManufacturingTomorrow
Comments (0)
This post does not have any comments. Be the first to leave a comment below.
Featured Product
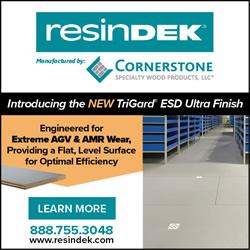