Too much data, little of which can be accessed and used effectively. From tuggers, AGCs (Automated Guided Carts), and AGVs, there is a real need to include IIoT monitoring.
IIoT Monitoring Finally Included with AGVs
John Hayes | Vecna Robotics
There is a frequent complaint of Industry 4.0, Big Data, and the Industrial Internet of Things (IIoT). Too much data, little of which can be accessed and used effectively. From tuggers, AGCs (Automated Guided Carts), and AGVs, there is a real need to include IIoT monitoring.
All those sensors on AGVs (Automated Guided Vehicles) which prevent collisions (with people, equipment, or building structures) are collecting data. Until recently, no AGV manufacturer has found a way to concretize these data and make them actionable, predictive, and fundamentally useful.
IIoT Impacting Throughput in Manufacturing and Distribution
Without IIoT monitoring, plant managers, operations managers, logistics coordinators throughout manufacturing and distribution sectors lack the data collected offering real-time continuous vehicle status and health information of the vehicle.
Vecna Robotics sends these data directly to a highly skilled team of support engineers; corrective actions are executed and/or recommended before down-time occurs. This translates into bottom-line throughput improvement. Manufacturing throughput time is the amount of time required for a product to pass through a manufacturing process, thereby being converted from raw materials into finished goods. The concept also applies to the processing of raw materials into a component or sub-assembly. One important distinction of throughput in distribution centers is that a warehouse is usually used to store goods for longer periods of time, while distribution centers concentrate on faster turnover (or throughput) of goods.
IIoT Data Directly Impacts Safety
OSHA statistics indicate that there are roughly 85 forklift fatalities and 34,900 serious injuries each year, with 42 percent of the forklift fatalities from the operator being crushed by a tipping vehicle. The Industrial Truck Association reports that the average life of a forklift is nine years, and there is a 90 percent chance of a serious accident over the course of its life. Seventy to eighty percent of the accidents impacts pedestrians around the truck. Going fork-free immediately changes these dire and dangerous prognoses. Plants that implement fork truck free zones, or partially fork truck free implementation, realize significantly improved safety data, lower insurance rates, fewer workers’ compensation claims.
One of the unique differentiators and critical value propositions of IIoT monitoring includes a video feed from vehicles allowing for remote access to all vehicles AND the ability to immediately address situations that are not safe. While other AGV vendors may have the data collected via sensors, it is the disruptive leadership of Vecna Robotics that determined the critical, even life-saving, need for IIoT monitoring with all their vehicles.
While there is absolutely an ROI (Return on Investment) calculation in this IIoT monitoring service, one qualifiable data point is peace of mind. Knowing that the operation of these vehicles and their interaction with the plant floor is monitored 24/7 by factory engineers represents of first-of-its-kind industry breakthrough in utilization of data to produce the safest and most efficient operation.
IIoT and Vehicle Maintenance
Maintenance is not a sexy topic when it comes to AGVs or tuggers. Few AGV vendors want to discuss the costs associated with maintenance, yet it cannot be ignored or neglected. Maintenance issues often occur with competing systems rendering the vehicle inoperable; plant floor managers then must notify maintenance of the issue, locate the vehicle in the facility, travel to the vehicle, assess and address the issue. This additional cost, combined with down-time, is never part of other vendor ROI calculations. Omitting this real cost is naïve at best and irresponsible at worst. It is precisely why Vecna Robotics includes IIoT monitoring so the error can be assessed and addressed thereby reducing maintenance labor costs associated with nuisance errors and providing significant savings to the company.
IIoT Drives Operational Efficiency and Improved OEE
The inclusion of IIoT monitoring ensures increases in operational efficiency. Eliminating the ripple effect caused by stopped vehicles is a metric of Overall Equipment Effectiveness (OEE). The widely utilize data point, OEE, evaluates how effectively a manufacturing operation is utilized. The results are best used to identify scope for process performance improvement, and how to get the improvement. When the cycle time is reduced, the OEE will increase (more product is produced for less resource). More changeovers (set-ups) will lower the OEE and this includes down-time from tuggers and AGVs not operating during production times.
OEE measurement is used as a key performance indicator (KPI) in conjunction with lean manufacturing efforts to provide a quantifiable measurement of success.
A single vehicle stopped on a high traffic area has the potential to block ALL vehicles behind it. This means that a 15-minute stoppage for one vehicle could be 150 minutes of move time if there are ten vehicles in the system. With an average move time of six minutes, that equals 25 moves in a 15-minute period! Not to mention that many systems are NOT sized to catch up after system error of that magnitude. With the IIoT monitoring service solution, these types of errors have an immediate corrective action implemented and product continues to move in a smooth and efficient manner.
IIoT from a Different Perspective
Vecna Robotics discovered importance of IIoT in logistics and manufacturing production from a different lean manufacturing perspective than any other AGV vendor. In conducting an in-depth root-cause analysis, the leadership of the Cambridge, MA technology company was not saddled with a commitment to a specific technology solution, allowing for an authentic Value Stream Mapping (VSM). The current state (and future state) of most AGV vendors keeps them tied to a technology or a paradigm. If changed, those vendors would experience too costly and irreparably negative ripple effects to support existing equipment as well as lower margins due to technology ramp up time. They are stuck in their old technology. Vecna Robotics is not and this agility combined with non-stop IIoT data collection ensures the future state of customers can be modified and adapted to the needs as they arise.
Vecna Robotics RT4500-DO is built to automate the point-to-point transport of flatbed cars or carts.
This different view (one of robotics, not forklifts) has driven the use of a sensor suite, rather than an individual guidance type. This means that many different sensors can be used to achieve the best and lowest cost solution to the customer. The sensor suite allows for the system to be used in a manner that takes the best of both high cost AGV type systems and lower-cost cart type systems.
This sensor-based IIoT approach ensures the new solution is flexible and capable of complex systems (such as with high cost traditional AGV solutions), and cost-effective (such as with low-cost cart type systems). The high-level, non-stop real-time monitor technology defines materials handling as a gamechanger. Now, for the first time, an AGV is a mechanism by which best-in-class software communicates with the vehicles for traffic control, order generation, and routing locally and remotely.
Part of the data transferred from the vehicle is local vehicle status information with respect to system anomalies. This data is also transferred directly to the clients for immediate action, providing the maintenance and support team the ability to fix issues and keep efficiencies high.
The most significant advancement is that local maintenance or support persons may never have to see these issues; with Vecna Robotics’ use of IIoT and the data transferred directly to their service facility. Vecna Robotics assesses and addresses issues before they become visible to the end-user. This nearly eliminates all user error handling and leaves these potential issues IMMEDIATELY in the hands of the manufacturer.
These are vital data that even expensive AGVs are lacking, demonstrating the leadership role of IIoT within the materials handing sector.
About John Hayes
John Hayes, Vice-President of Sales and Logistics for Vecna Robotics, is a widely-respected thought leader for the manufacturing, distribution, and materials handling industries. For more than twenty years Hayes has been evaluating, designing, developing, and implementing innovative software and hardware solutions, with a particular focus in the AGV (automated guided vehicle) space. Hayes is a Supply & Demand Chain Executive "Pros to Know" recipient.
The content & opinions in this article are the author’s and do not necessarily represent the views of ManufacturingTomorrow
Comments (0)
This post does not have any comments. Be the first to leave a comment below.
Featured Product
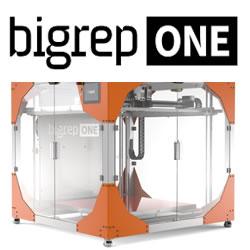