A typical application of insert molding is to include one or more threaded metal inserts in a plastic part when that part is intended to mate to another part in an assembly.
Insert Molding vs Traditional Injection Molding
Becky Cater | Proto Labs
Tell us a little bit about Proto Labs.
Proto Labs is the world’s fastest manufacturer of custom prototype and low-volume parts. The company’s proprietary software and automated systems translate 3D CAD models into instructions for high-speed manufacturing equipment that 3D print, machine and mold parts in a matter of days. Proto Labs’ additive manufacturing service can build highly complex prototypes and end-use parts from a selection of plastic and metal materials. Its CNC machining service can mill and turn from one to 200+ engineering-grade plastic and metal parts in three days or less. For larger quantities, Proto Labs can injection mold up to 10,000+ parts made from a full menu of thermoplastic resins, including liquid silicone rubber, in less than 15 days. The catalyst is an automated quoting system that provides design analysis and pricing information within hours of uploading a 3D CAD model.
You recently added insert molding services to your offerings (Press Release), why now?
We launched insert molding in response to high customer demand. We work closely with our customers to understand how we can help them accelerate their product development cycle and stay ahead of their competition. The need for molded-in inserts was a frequent request. In keeping with Proto Labs’ digital manufacturing business model, we took the time to develop software automation for our front end quoting and manufacturing processes to enable us to offer on-demand insert molding services to our customers at unprecedented speed.
What does the manufacturing process look like for insert molding?
Insert molding is the process of molding thermoplastic material around a preformed component (an insert) to create a finished part that incorporates multiple materials. The inserts are typically metal parts that are used to reinforce the mechanical properties of the plastic part. The inserts are placed into the mold and thermoplastic is injected into the mold to form the part. As compared to installing inserts into a plastic part in a post-molding process, the use of molded-in inserts eliminates the need for secondary installation of the inserts and thereby reduces costs.
What industries commonly use insert molded parts?
Insert molding is commonly used in a broad range of industries, including medical, automotive, consumer products and electronic components. Common applications include electronic housings, knobs and dials and hand-held devices.
Give us some advantages of using insert molding vs traditional injection molding?
A typical application of insert molding is to include one or more threaded metal inserts in a plastic part when that part is intended to mate to another part in an assembly. Plastics alone may not have sufficient mechanical properties to withstand the forces required to fasten two parts together. For example, threads in a plastic part can become worn over repeated usage which can result in a failed part. Metal inserts help reinforce the properties of the plastic and ensure reliable fastening over repeated use of the part. This combination of plastic and metal allows designers to take advantage of the weight reduction of plastics and the strength of metal.
What are the major design guidelines to follow when designing an insert molded part?
As with any molded part, the typical moldability design guidelines also apply to insert molded parts, like adding draft to help the part release from the mold and maintaining consistent wall thickness. In addition, there are some unique considerations to take into account when designing a part for insert molding. For example, designing in undercut features can help enhance the retention strength of the inserts within the molded part. Because the inserts must be placed into the mold, it is also important to make sure the insert is located in an accessible area of the mold. Making sure the inserts are not too deep within the part and have a way to be held in place in the mold during the molding process will also help ensure successful results.
What materials can be used for insert molding?
Most moldable thermoplastic resins are compatible with the insert molding process. The inserts are most commonly made of metal, typically brass, aluminum or stainless steel. Threaded inserts are readily available in a number of standard sizes. Bushings, sleeves and other simple metal forms are also used.
Anything else interesting coming down the pipeline from Proto Labs that you can share?
We officially launched PolyJet 3D printing on March 29th at the Advanced Manufacturing Expo. PolyJet provides product designers and engineers with the ability to manufacture elastomeric and overmolded prototypes without investing in tooling. You can view the Press Release here.
The content & opinions in this article are the author’s and do not necessarily represent the views of ManufacturingTomorrow
Comments (0)
This post does not have any comments. Be the first to leave a comment below.
Featured Product
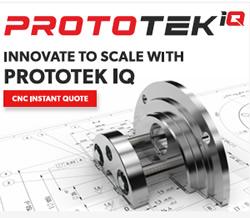