While those in additive manufacturing know that there are many technical aspects to their craft, they also realize training is necessary to manufacture quality parts.
The Pursuit of the Perfect Part
Paul Bates | UL LLC
Jointly run by UL and the University of Louisville, the UL Additive Manufacturing Competency Center (UL AMCC) has trained professional engineers, designers and technicians from civilian and military government agencies to universities and service bureaus.
While those in additive manufacturing know that there are many technical aspects to their craft, they also realize training is necessary to manufacture quality parts. These UL AMCC courses train students and address their concerns about the ability to repeatedly produce a part that meets certain specifications and standards.
The instructors begin a particular course with an in-depth review of metal powders, safety issues and processing considerations for a facility as well as the requirements for personal protection. Then, they move on to the overall additive process, starting at the beginning. The courses move from beginning to advanced design considerations and how to handle the build system to supporting strategies for part removal and post-processing.
Learning AM hands-on
For a completely hands-on experience, students build their own metal parts before training concludes, either by using designs developed by the center or bringing their own. Instructors review them to verify they are buildable and help the students think through support strategies for the manufacturing process that might include how to incorporate a support structure when building the material.
Trainees generally have some knowledge of additive manufacturing experience, either managing a team or using the equipment. They have been in traditional manufacturing for years and have been tasked with evolving their shops to include additive manufacturing capabilities. A basic understanding of computer-aided design tools is an essential pre-requisite of the training.
UL creates an encouraging environment, one in which students can take risks without worrying about a failed build. The UL Center trys to make the classes interesting because learning about this complex and technical manufacturing process can be a challenge.
Students learn to prepare the build plates, how to run the additive manufacturing machines and most importantly how to create a consistent process. The process is a challenging one and requires attention to detail in all aspects of the process. One mistake means that a part will not be completed properly.
Heating and cooling of the parts causes tremendous stress, and a part can curl up like a potato chip. UL shows them how to create parts the right way.
While producing quality parts is the primary concern for students, a key factor of the program explains the potential health and safety considerations for handling metal powders, which can pose a real danger. The UL Center guides students in understanding how to manage risks from pre-production to clean up, enabling the machines to be used safely.
Learn more about the UL AMCC’s Advanced Training on Metal Part Production, class schedules and registration details.
The content & opinions in this article are the author’s and do not necessarily represent the views of ManufacturingTomorrow
Comments (0)
This post does not have any comments. Be the first to leave a comment below.
Featured Product
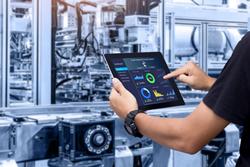