How software and technology are digitizing the manufacturing industry, and the benefits to business leaders.
Data, Digital Threads and Industry 4.0
Kip Hanson | Proto Labs
A decade before the American Revolution, Glasgow instrument maker James Watt was assigned with repairing a Newcomen steam engine. He quickly realized the design could be improved by adding an external condenser coil, which greatly increased thermal efficiency. The Watt steam engine soon saw widespread use in mining, textile and other industries. Mills and factories sprung up, workers moved to the cities, and the world's agrarian society was gradually transformed into one of mechanization. The First Industrial Revolution had begun.
Industrial growth was soon stymied, however, by a shortage of inexpensive steel. Once again, a simple invention — the introduction of compressed air into a furnace filled with molten pig iron — changed everything. English inventor Sir Henry Bessemer patented his new process in 1856, and began using it to produce steel far more quickly and at a fraction the cost of competing methods. The growing use of electricity and Henry Ford’s development of assembly line production methods during the early 1900s further bolstered this second phase of the industrial revolution, paving the way for our modern industrial society.
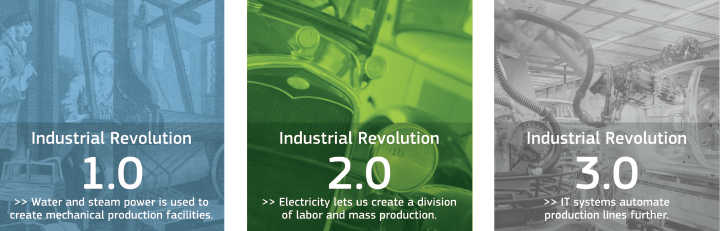
Fast forward to 1958. Jack Kilby, a new employee at Texas Instruments, is working through the company’s summer shutdown — he didn’t yet have the right to take a summer vacation — in search of a way to miniaturize the electronic components produced by his employer. His notion of combining these transistors, resistors and capacitors on a single piece of germanium would eventually lead to the integrated circuits that drive every appliance, automobile, computer, cell phone and television in use today. Computer numerical controlled (CNC) machine tools would not exist without them, nor would the software systems that manage our manufacturing plants. Kilby is truly the father of the Third Industrial Revolution.
The New Frontier: Industry 4.0
In 2007, German economist Klaus Schwab told an assembly of the World Economic Forum, which he founded, that the world was now entering a Fourth Industrial Revolution1, one that “has the potential to raise global income levels and improve the quality of life for populations around the world.” Schwab was referring to a digital shake up that stands to turn the past several decades of growth in electronics and computer technology on its head with unprecedented levels of low-cost data storage, artificial intelligence, mobile computing, Software as a Service (SaaS) and Cloud-based computer systems. Behind everything? The Internet of Things (IoT), which promises to tie it all together with smart devices that will collect data, make decisions and keep humans informed of potential problems.
German economist Klaus Schwab (Photo credit: Bertelsmann Stiftung)
Schwab also warned of dangers. As manufacturing technology continues to evolve, labor markets will almost certainly be disrupted. Legislative processes and governmental regulations may fail to adapt quickly enough for the exponential growth of digital innovation, leading to conflict between the businesses embracing such technology and the policymakers trying to understand it. And however positive the impact of the coming revolution may be, it raises even larger questions about national security, personal privacy, even autonomous weaponry and electronic cyber-attacks. These will become increasingly relevant topics as machines, devices and software begin to think and act independently. This revolution more than any other has the potential to change industry, yes, but it may also alter our very way of life.
Two of Schwab’s contemporaries, Siegfried Dais, deputy chairman of the board of management at Robert Bosch GmbH, and Henning Kagermann, president of the German Academy of Science and Engineering, first introduced the term Industrie 4.0 at the Hannover Fair in 2011. Two years later, their Working Group on Industry 4.0 presented recommendations2 to the German government on how the country’s manufacturing industry should leverage the Internet of Things and Services to increase national competitiveness, and that smart factories using “universal direct networking of smart objects via the Internet,” something that most refer to as the Industrial Internet of Things, or IIoT, is the next phase of the Industrial Revolution.
A Web of Intelligent Hardware
But what exactly is the IoT? How did it become industrialized, and when did objects become smart? These are important questions, at least some of which can be answered by your teenager or your company’s resident computer geek. Wearable fitness trackers, self-driving cars, learning thermostats — these are just a few of the everyday smart devices that use complex technology to make our lives simpler.
Some of these are little more than commercial gimmicks, while others have the capacity to drastically change our world. Taken to the regional or country level, the IoT empowers governments to automatically measure pollution levels, check for contaminants in our water supplies, track endangered species and arrest poachers, warn the public of earthquake, fire, or terrorist attacks, monitor infrastructure such as bridges and roads, and greatly increase the efficiency of electrical grids.
Somewhere between consumers and cities sits the engine that drives it all: commerce and industry. This is where the IIoT comes in. So great is the potential benefit in this area that a 2013 report by global networking technology provider Cisco3 predicted an additional $14.4 trillion of value (net profits) for private-sector companies by 2022, spanning improvements across five aspects of business: asset utilization, employee productivity, supply chain and logistics, customer experience, and innovation.The company also said there will be 21 billion networked devices by 2018, up nearly 50 percent from just five years earlier. That’s a lot of cash and a lot of connections.
Material Selection
By designing for the 3D printing process and adjusting the build orientation, anisotropism or inadequate material properties can be overcome. To do this, leverage the experiences from past projects or that of a qualified service organization to fill in the data gaps that exist because of the limited material properties data. When performance is critical, also consider independent lab testing of additive materials.
While success is dependent on material properties, they are not the only considerations. Each additive material and build process will also dictate characteristics such as maximum part size, dimensional accuracy, feature resolution, surface finish, production time and part cost. So it is advised to select a suitable material and then evaluate its ability to meet expectations and requirements related to time, cost and quality.
Follow the Digital Thread
Industry 4.0 and the IIoT revolution require far more than smart gadgetry and garrulous machine tools. Perhaps the biggest wave in this industrial sea change is “digital manufacturing,” a relatively new way of sharing data throughout the entire product life cycle, leading to lower costs, quicker turnarounds and improved part quality. Companies such as Siemens and PTC are busy developing integrated software platforms that link all aspects of manufacturing, from initial product design to factory layout to customer feedback after delivery. This “digital thread” eliminates the silos of information that have long hampered data exchange between disparate software systems, tying together each aspect of the manufacturing process, including 3D CAD modeling and visualization tools, design for manufacturability (DFM) analysis software, computer-aided manufacturing (CAM), computer-integrated manufacturing (CIM and shop floor data collection systems.
Properly integrated, this software alphabet soup encompasses the digital thread of information flowing from product conception, through design, prototyping, and manufacturing, and back to redesign. Add in all of the auxiliary threads tied into this process — sourcing, logistics, warehousing and financials to name a few — threads that are typically managed by the big brother of all acronyms — ERP, or enterprise resource planning — and the digital cycle is complete.
These software systems do more than trade data. They eliminate much of the human intervention that goes with managing them. This is called automation (we’re not talking about robots here), and is a big part of, if not the key driver behind, digital manufacturing. This is exactly what Larry Lukis had in mind when he started the rapid manufacturing company Proto Labs in 1999. At that time, Bill Gates was still CEO of Microsoft, Google was less than a year old and the closest thing to a smartphone was the Blackberry. Lukis’ goal? To produce injection-molded parts at a fraction of the cost and time of traditional methods.
Lukis knew he would need to significantly automate the process, but not in the way most people think. He needed a way to reduce the upfront time required for the complex quoting, mold design and toolpath programming, delays that had plagued him in his previous position with printer manufacturer LaserMaster. There were no software systems capable of such a task back then, so Lukis and his team developed custom software to achieve the task. He then developed a proprietary manufacturing process to go with it.
A Convergence of Software and Hardware Automation
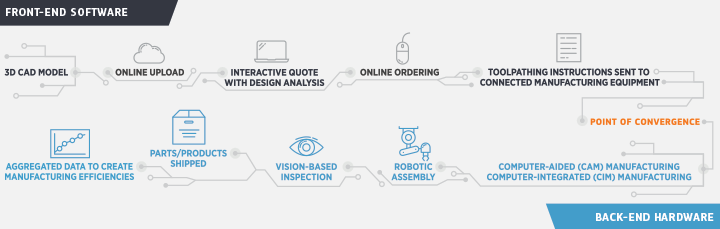
Proto Labs has since taken that original idea and run with it. Around the time the company launched its quick-turn CNC machining operations in 2007, the decision was made to bypass the company’s ERP-based scheduling system in favor of a homegrown system with digital manufacturing awareness. The information from the integrated part quoting and toolpathing systems was automatically shared with the production floor, where video displays allow workers to see real-time information on job queues, setup requirements, production and quality metrics. Likewise, status information is automatically collected as jobs progress through the manufacturing process, and then fed back into the MRP and inventory control systems.
It’s a closed-loop system, one that requires less human intervention on the production floor and more in front of a computer. This reduces manufacturing costs, increases throughput and gives management the much needed data to make intelligent decisions. Because of this, Proto Labs has grown from a small startup into a 1,500-employee (globally), $264 million company specializing in quick-turn molding, machining and 3D printing, and more, capable of delivering plastic, metal and liquid silicone parts in days. This is the essence of digital manufacturing.
A Game-Changing Playbook
Larry Lukis isn’t the only one tugging on the digital thread. Siemens PLM defines digital manufacturing as a way to allow engineers to “create the complete definition of a manufacturing process in a virtual environment, including tooling, assembly lines, work centers, facility layout, ergonomics, and resources.” The result is greater throughput, removal of manufacturability constraints, and the ability of digital manufacturing companies to make better decisions more quickly. As proof, Siemens customer Waltonen Engineering, Warren, Mich., used digital manufacturing techniques to reduce dimensional-related costs by up to 50 percent. Furniture manufacturer Swerve joined forces with its machine tool vendor and Siemens to improve integration between its PLM and CAM system, resulting in business growth and greater ability to handle close tolerance work. Aerospace giant Pratt and Whitney revamped its various configuration management systems in favor of a unified CAD-driven data management solution from Siemens, one that decreased product development costs by 75 percent.
Compute cluster
These results aren’t unique. According to consulting firm CIMdata, digital manufacturing efforts can improve time-to-market by 30 percent, reduce process planning efforts and equipment costs by 40 percent and increase overall production throughput by 15 percent. In addition, Patrick Michel, Dassault Systèmes vice president of DELMIA industry solutions and marketing, says, “Companies that deploy digital manufacturing solutions enterprise-wide do so because they want to take virtual plant tours, mitigate the risks inherent in design planning, identify how plant designs will impact the workers who will one day be in them, reduce the need to redesign equipment, utilize resources more efficiently and eliminate prototypes. Digital manufacturing takes a slow, manual, resource-intensive process and brings it into the 21st century.”
Indeed, the velocity of digital manufacturing offers still other benefits: Cost savings in the product development phase because development cycles are shorter; greater efficiencies with on-demand or low-volume manufacturing, again enabled by the digitization process; and, accelerated design iteration that leads to greater innovation overall for developers, thanks to the speed of the front-end quoting and analysis process.
Change is scary for most companies. Disruptions in the supply chain or production output can spell disaster for manufacturers and consumers alike. How, then, can far-reaching modifications to industrial infrastructures and processes be accomplished? You can start by resetting corporate expectations. Charge your people with thinking differently. Collaborate with employees, customers and even competitors to examine the status quo, and then chuck it out the window. And work closely with digitally savvy suppliers. Leverage their nimble tactics and data-driven manufacturing techniques to improve your company’s own digital prowess. And know that the path to digital manufacturing is often an unconventional one. As anyone who has traveled into the digital frontier knows, there are no hard and fast rules out here. It’s only by accepting a new playbook and embracing change that a reinvention of the business can occur.
So great is the potential of digital manufacturing and the IIoT for improving the American economy that President Obama has gotten in on the action. Recognizing the threat of foreign competition and the outflow of U.S. jobs to low labor cost countries, he charged leaders of industry, academia and the government with finding ways to reinvigorate the country’s manufacturing sector. The National Network for Manufacturing Innovation, or NNMI, was born of those efforts. The organization has a broad charter, encompassing development of advanced technologies such as additive manufacturing, development of lightweight metals including magnesium and titanium, advanced composites manufacturing, nanotechnology, and more, but one of its chief focus areas is “creation of a smart-manufacturing infrastructure and approaches that integrate low-cost sensors into manufacturing processes.”
Many of these new initiatives center on additive manufacturing, or 3D printing. Proto Labs has embraced this technology with a spectrum of industrial 3D printing capabilities, including stereolithography (SL), selective laser sintering (SLS) and direct metal laser sintering (DMLS), which have the ability to create parts in virtually any shape imaginable. As with Proto Labs’ more traditional manufacturing processes, the digital thread is alive and well here as well. Data is shared between both ends of the manufacturing process and everywhere in between, from product conception and design upload to printing, finishing and delivery. And by incorporating technologies that have traditionally been at opposite poles of the industry — additive and subtractive — Proto Labs has substantially increased its flexibility and provided new ways to cut production costs and manufacturing lead times — a benefit reaped by companies rapidly developing new products and maintaining them beyond launch.
Breaking Barriers, Leveraging Data
Subtractive equipment manufacturers stand to benefit from the IIoT and digital manufacturing processes as well. In 2013, machine tool builder Okuma Corporation opened its DS1 (Dream Site 1) plant in Oguchi, Japan, showcasing the company’s lights out manufacturing and automated production control capabilities. Since then, productivity has doubled, delivery lead-time has been cut in half, and electrical costs are down 30 percent. The following year, competitor Mazak announced its iSMART4 factory concept, the “complete digital integration” of its 10 manufacturing plants with state-of-the-art equipment and advanced manufacturing practices. Both companies stand poised to share much of this forward looking technology with customers in the form of machine tool integration and M2M (machine-to-machine) communications, driving greater productivity and part quality down to even the smallest shop floor.
Much of the communication capability among this and other equipment is fueled by a more recent development in communications known as MTConnect. This open source protocol is to the factory what HTML is to websites. Without it, sharing information between the dozens of different control builders would be exceedingly difficult, and the Industrial Internet of Things — that subset of the IoT concerned with manufacturing — would come to a screeching halt.
One company leveraging the massive amounts of data available from the shop floor is industrial communication technology provider MEMEX Inc., a business partner with Cisco, Okuma, Mazak and others. As CEO David McPhail points out, multinational management consulting firm Accenture estimates that capital investments in IIoT and the productivity gains that should follow could add $6.1 trillion to the United States’ cumulative GDP by 2030. “That’s a huge number, and we believe the IIoT represents no less than the next Industrial Revolution.”
General Electric’s “Brilliant Factory” initiative implemented a perpetual data-sharing loop.
A compute cluster that helps power GE's gas turbines. Image credit: GE Power
Drinking the Electric Kool-Aid
Another company that’s busy reinventing itself is General Electric. President and CEO Jeff Immelt points to the Industrial Internet as a five-legged stool of hyper connectivity, brilliant machines, data democratization, predictive algorithms for improved analytics, and people hard at work using, all of this technology. Because of GE’s commitment to these concepts, the company was the first to use 3D-printed components in jet engines, challenged the additive manufacturing “maker” community with redesigning one of its aircraft brackets, and routinely invites technology proposals from third-party companies for alternative manufacturing techniques. It also gave a big thumbs-up to the IIoT movement with its introduction of Predix, an “operating system for the Industrial Internet.”5
As part of its Digital Alliance Program, GE has opened the Predix development platform to system integrators, machine builders, telecommunications suppliers and pretty much anyone with a hankering to develop secure software solutions for use in an industrial environment.
One of the words in that last sentence — secure — is especially important as manufacturers step through the digital doorway. The vast majority of machine shops and small manufacturing firms today don’t even have a dedicated IT person on site, let alone an expert on network security. Yet the possibility of hackers disrupting the shop floor becomes increasingly likely as more and more shops “get connected.” That’s why Cisco and others are working on ways to simplify the infrastructure needed for safe industrial computing, so shop owners don’t have to lay awake at night wondering about the security of their shiny new network-aware factories.
Digital manufacturing at Proto Labs
The Factory of the Future
Steel, steam engines, assembly lines and integrated circuits — the pillars of previous revolutions could be seen, touched and smelled. Not so with the IIoT and the digital thread, a virtual confluence of data, software and sensors where various networks of technology work together to streamline existing design and manufacturing processes. However, the IIoT and Industry 4.0 share one big thing in common with earlier industrial revolutions — the promotion and betterment of that most basic modern institution: the factory. Without manufacturing, any country will flounder, and it’s up to those manufacturers to provide the best capabilities and most efficient processes in which companies can leverage to produce products.
About Proto Labs
Proto Labs is a digital manufacturer of rapid prototypes and on-demand production parts. The technology-enabled company uses 3D printing, CNC machining, and injection molding processes to produce parts within days. The result is an unprecedented speed-to-market value for designers and engineers, and a manufacturing resource throughout a product’s life cycle. Visit protolabs.com for more information.
Sources:
cisco.com, dmdii.uilabs.org, ge.com, memex.ca
1 weforum.org/agenda/2016/01/the-fourth-industrial-revolution-what-it-means-and-how-to-respond
3 cisco.com/c/dam/en_us/solutions/industries/docs/gov/everything-for-cities.pdf
The content & opinions in this article are the author’s and do not necessarily represent the views of ManufacturingTomorrow
Comments (0)
This post does not have any comments. Be the first to leave a comment below.
Featured Product
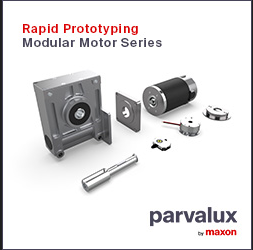