These Innovations in Telecommunications Are Elevating Manufacturing in 2025
Telecommunications have always been vital in the manufacturing sector. But in 2025, rapid advancements in connectivity and network technologies are taking things to new heights.
From 5G to edge computing, innovations are reshaping how factories operate and redefining smart manufacturing’s potential.
5G and Beyond
The rollout of 5G is accelerating smart factory deployments, providing a foundation for the next generation of manufacturing. With ultra-low latency and high data transfer speeds, 5G enables real-time communication among machines, sensors and workers. The immediate impact is most noticeable in automation. In the past, communication delays between devices could lead to errors or bottlenecks. Now, large production facilities can seamlessly synchronize processes.
5G’s massive device capacity is also a game-changer. With traditional networks, factories faced limitations in how many devices they could connect at once. 5G eliminates these restrictions, allowing thousands of IoT devices to communicate simultaneously without degrading performance. This ability is critical in smart factories that rely on communication among every machine, sensor and robot. Manufacturers can now monitor and control all aspects of their operations in real time, from inventory tracking to machine performance.
Another advantage is the ability to download and stream content within a few seconds without worrying about lengthy buffering times. Whether accessing large-scale CAD models or high-resolution training videos, 5G ensures manufacturers can instantly retrieve critical information.
The benefits of 5G go beyond the factory floor. The increased speed and reliability also allow manufacturers to deploy remote and augmented reality solutions. Technicians can access real-time guidance on machine repair or operations, improving accuracy and reducing downtime.
Edge Computing
Edge computing has emerged as an essential complement to the 5G advancements, addressing the need for faster data processing. In traditional cloud-based systems, data must travel to centralized data centers for processing, creating latency issues that can hinder critical decisions. Edge computing solves this problem by processing data locally, near the generation source — whether that’s a machine, sensor or robot. Doing so reduces dependency on cloud services, making real-time decision-making possible.
Edge computing allows for more reliable operations in manufacturing. Sensors integrated into machines can monitor performance continuously and in real time. If an edge device detects an anomaly, such as a malfunction or efficiency drop, it can immediately adjust processes or alert workers — without waiting for data to travel to a central cloud for analysis. This capability results in faster responses, less downtime and fewer production disruptions.
AI-Powered Communications
Artificial intelligence is rapidly changing how manufacturing facilities handle internal and external communication. AI-powered communication platforms are becoming central to optimizing production and improving efficiency. These platforms analyze data from machines, production lines and supply chains to offer actionable insights.
For example, AI can predict demand fluctuations, enabling manufacturers to adjust production schedules without delays or waste. Similarly, these tools optimize supply chains by identifying the most efficient routes or pinpointing the ideal inventory levels for specific products.
AI’s role in predictive maintenance is another influential area. By processing data from IoT sensors, AI can predict when machines are likely to need maintenance or repairs. Manufacturers use this information to schedule interventions before issues arise, minimizing downtime and reducing costly reactive fixes. AI can even assist in identifying patterns in production line data that human analysis might miss, enabling smarter decision-making.
Additionally, AI enhances communication on the factory floor. Workers now have access to AI-powered chatbots or virtual assistants that can provide real-time information about machine status, inventory levels or operational efficiency. These AI systems are becoming more adept at handling increasingly complex queries, making them invaluable tools for frontline workers. AI can also act as a liaison between departments, streamlining communication and making it easier for teams to stay informed and aligned.
Many industries use AI to safeguard their data and systems from cyber threats. AI can detect anomalies and prevent security breaches before they happen. In manufacturing, AI-driven cybersecurity can protect connected devices and production data from cyberattacks, ensuring the integrity of operations.
Private Networks
The need for robust cybersecurity grows as manufacturing becomes more connected. Public networks are more vulnerable to cyberattacks and network congestion, which is why many manufacturers use private 5G networks to gain control over their connectivity. By implementing dedicated, isolated networks, manufacturers can ensure sensitive data, such as production processes, intellectual property and employee information, remains secure.
Private 5G networks also offer the flexibility to prioritize traffic. For instance, critical applications, such as real-time monitoring systems or autonomous robots, deserve higher bandwidth to ensure consistent performance. This versatility is particularly valuable in industries where downtime can result in dramatic financial losses, such as automotive or aerospace manufacturing. It’s also possible to tailor private networks to meet the factory environment’s specific needs, offering a customization level public networks can’t provide.
Moreover, private networks enable manufacturers to reduce their reliance on external providers, improving their control over connectivity. The result is a more reliable network that offers faster speeds, increased security and consistent performance, all of which are crucial for maintaining modern manufacturing operations’ efficiency and competitiveness.
Digital Twins
The rise of digital twins is one of the most transformative innovations in manufacturing. These digital replicas of physical systems allow manufacturers to simulate, evaluate and refine processes in real time. By integrating telecommunications advancements like 5G, IoT and AI, digital twins can mirror entire factories, individual machines or even specific production lines.
In 2025, manufacturers use digital twins to detect inefficiencies, predict equipment failures and test process changes before implementing them in the real world. For example, a factory producing automotive parts can run simulations in a digital twin environment to see how changes in machine speed or material composition might impact quality. Instead of making costly adjustments to the production line, engineers can tweak variables in the digital model and implement only the best-performing changes.
Digital twins are also revolutionizing supply chain management. Manufacturers can create digital replicas of their entire supply chain with real-time data feeds, identifying bottlenecks before they cause disruptions. AI-powered models can predict the downstream effects of shipment delays and suggest alternative solutions to keep production on track.
Additionally, digital twins enhance collaborative work across global manufacturing teams. Engineers, factory managers and R&D teams can work together in a shared digital environment, testing new workflows and product designs without physical constraints. As more manufacturers embrace this technology, decision-making is becoming faster, smarter and more data-driven than ever before.
The Future of Manufacturing Is Connected
Telecommunications innovations are transforming manufacturing in 2025. The combination of faster, more reliable networks, advanced edge computing, AI integration and secure private networks is creating a new paradigm for factory operations. These technologies allow manufacturers to push the boundaries of what’s possible, from fully automated production lines to intelligent decision-making powered by real-time data.
As these innovations continue to evolve, hyperconnectivity and adaptability will characterize the manufacturing sector. In the future, automated factories will be smart, predictive and self-optimizing. Manufacturers who leverage these telecommunications advancements will stay ahead of the curve, achieving higher productivity, improved safety and better operational resilience.
Comments (0)
This post does not have any comments. Be the first to leave a comment below.
Featured Product
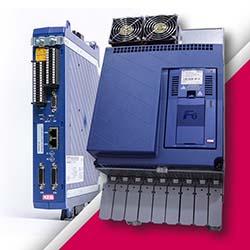