Dealing with the Aftermath of M&A via Configuration Management
Merger and acquisition (M&A) activity in the manufacturing sector is starting to pick up following a slight lull, with the latest EY-Parthenon Macroeconomic outlook anticipating a 13% increase by the end of 2024 and a 10% increase in 2025.
Manufacturers can use deals to leverage new technology capabilities and diversify their supply chains. However, as businesses grow and merge, the need to manage complexity becomes greater. As different systems and departments come together, aligning product data across multiple, sometimes duplicate, systems end-to-end becomes a major challenge.
Configurable options and rules are defined at every step in the process and must be aligned end-to-end to ensure consistency and avoid errors. Misalignment often leads to offering options that cannot be delivered, delivering the wrong solution and fire-fighting by expensive expert resources.
Configuration Lifecycle Management (CLM) can help companies navigate the changes that follow an M&A and the increased product complexity that almost all companies face today.
M&A: A slow-burning consolidation problem
Most manufacturers have hundreds of applications in their IT landscape. Business IT teams are charged with reducing the number of applications as much as possible, which can be difficult. M&A activity typically adds hundreds more applications that are often duplicates of what is already installed. Consolidation thus becomes a major focus.
The merging of systems and applications typically occurs after the corporate M&A is completed, sometimes two years or more after the event.
Business IT need to systematically assess each application overlap in the IT landscape to determine what to keep and what to discard. This is a difficult task as two applications addressing the same need, such as ERP or PLM systems, will have pros and cons. What is more challenging is that the data available in both applications are similar but not the same. Different data formats, architectures and underlying assumptions make it difficult to compare or merge the data into a single solution.
It can, therefore take considerable time before a true consolidation of the IT infrastructure can take place.
Consolidating with CLM
Suppose you and another company merged a year ago; now it’s time to consolidate the systems. You've got multiple PLM and Enterprise Resource Planning (ERP) systems, and you're trying to figure out how to manage them all. You've got new brands, divisions and departments that have come into your universe. And you have to handle all of this without letting production slip or otherwise impact customers.
This is where Configuration Lifecycle Management can play a key role. CLM is a systematic approach to managing a product's configurations at every step in the process across the product lifecycle, ensuring consistency, traceability, and alignment with business requirements to improve efficiency and reduce errors.
With a CLM approach, it is possible to extract configurable options and rules from existing applications and create a standard product model spanning engineering, manufacturing, sales and service. The CLM approach consolidates the configurable product data from all applications and ensures that everything is aligned. The product model data can be synchronized with key systems like PLM and ERP to ensure the product model is always up-to-date. This creates a “shared-source-of-truth” that is accessible to all, making the information easy to consume.
CLM is a new, cross-functional approach
Inconsistencies between different functional processes can be identified by providing an end-to-end, cross-functional view of all configurable options and rules. This offers the opportunity to identify potential errors early before they are released to customers.
Part of the value of CLM is that when you consolidate the product configuration data and establish a “shared-source-of-truth” with a common format, it is possible to ensure that data is aligned both end-to-end across functions but also across multiple versions of the same application. This allows multiple instances of the same application from different vendors to co-exist while providing a mechanism for identifying gaps and inconsistencies between product models, BOMs and other configurable product data in these different applications. This facilitates and accelerates the overall consolidation effort.
Federated PLM, for example, tries to create a common backbone for multiple PLMs to align and communicate with each other. That’s certainly an option, but for the configurable aspect, you can interface to all the PLMs and bring all the information into one product model. You can eliminate redundant systems once you’ve aligned the various systems and captured the needed information.
CLM provides traceability and analysis capabilities
CLM not only establishes a “shared-source-of-truth” product model that captures all of the configurable options and rules for the configurable product portfolio, it also captures all configurations made by users at every step of the process.
When a user configuration is made, for example, a sales configuration, this configuration is centrally saved together with meta-data that captures the state and type of configuration along with other relevant workflow information. This enables the establishment of a “digital configuration thread” linking user configurations at every stage of the process over time. Digital configuration threads thus provide traceability on how individual product configurations change over time, linking back to the product model on which the product configuration is based.
The availability of digital configuration threads provides multiple benefits. The traceability provided by digital configuration threads enables better governance and compliance with regulations. The information in digital configuration threads enables more efficient manufacturing and service of configurable products.
The central storage of digital configuration threads provides an overview of which configuration options were chosen by specific customers over time. This enables the impact of any changes or supply chain shocks on specific customers to be quickly ascertained. It also enables product portfolio optimization, comparing what is being sold versus what is being offered over time.
From a consolidation point of view, digital configuration threads can provide feedback on how to assess which duplicate applications to retain or discard based on an understanding of which product configuration capabilities and options are most valuable to customers.
CLM: Enabling more efficient consolidation after M&A
Consolidation of IT infrastructure is a challenge at any time, but especially after an M&A. By adopting a CLM approach for managing configurable product options and rules across the enterprise, IT professionals in manufacturing organizations can manage and plan consolidation of pillar IT systems like PLM and ERP. The CLM approach enables the coexistence of duplicate systems by establishing a “shared-source-of-truth” where data can be aligned and validated before exposure downstream. This ensures operations can continue more efficiently while eliminating errors and improving end-user experiences. A win-win-win situation.
Daniel Joseph Barry is vice president of product marketing at Configit, the global leader in Configuration Lifecycle Management (CLM) solutions and a supplier of business-critical software for the configuration of complex products. He has over 30 years of experience in the Telecom and IT industry, working in various technical and commercial roles.
Educated as an electronic engineer, he progressed from research and system development roles to leadership roles in business development, sales, product management, marketing and strategy in global multinationals like Ericsson, as well as startup and growth companies. After several years as an independent consultant, he joined Configit in 2023 in a role that leverages all his experience in articulating the value that CLM and Configit can provide, as well as providing insight into market needs.
Comments (0)
This post does not have any comments. Be the first to leave a comment below.
Featured Product
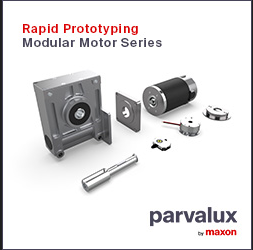