Bridging the Gap: Overcoming the Barriers to Manufacturing Digitization
In an era where AI, simulations, and massive data collection are transforming industries, many manufacturers remain stuck in outdated, paper-based processes. Despite decades of technological advancements, a staggering 70% of manufacturers still rely on manual data collection in 2024.
Why? Cultural resistance, financial constraints, and operational hurdles keep many—particularly small and mid-sized manufacturers (SMBs) —tethered to legacy systems. While digital transformation is often framed as a high-tech revolution requiring massive investments, the reality is that modernization doesn’t have to mean a complete system overhaul. Manufacturers can build on existing systems to break down data silos, improve collaboration, and attract new talent—without disrupting major operations.
Disadvantages of Paper-based Processes
For most manufacturers, especially SMBs, making informed decisions on the shop floor remains difficult. Data is often collected manually, entered into disparate systems that don’t communicate with one another, and stored in ways that prevent real-time insights. This fragmentation creates significant inefficiencies:
- Siloed operations: Quality inspection, maintenance scheduling, shift performance reporting, and operational efficiency tracking often exist as isolated functions rather than interconnected processes.
- Lack of a common source of truth: When departments operate on different sets of data, inconsistencies arise, leading to inefficiencies, duplicated efforts, and even costly errors.
- Competitive disadvantage: Manufacturers who fail to modernize struggle to compete in a fast-moving market, as disjointed processes slow down production and decision-making.
- Talent retention struggles: The younger workforce, accustomed to digital tools, is often discouraged by outdated manual workflows, exacerbating the ongoing skills gap in the industry.
- Compromised quality and customer experience: Disconnected processes and manual data handling increase the risk of errors, rework, and inconsistencies in production. These inefficiencies not only reduce product quality but also lead to delays, defects, and a diminished customer experience.
The Hidden Costs of Manual Processes
Manufacturers who hesitate to digitize often find themselves in an uphill battle to remain competitive. Inefficiencies due to manual processes cost valuable time and money. Siloed data can actively damage an organization’s ability to bring new products to market, particularly when different functions compete for resources or shift blame when problems arise.
Sticking to manual processes can also hinder manufacturers' ability to attract and retain a well-equipped, effective workforce. In fact, nearly three-quarters of manufacturing executives consider workforce retention their primary business challenge. As experienced workers retire, their replacements expect modernized processes, not stacks of paper and disconnected systems.
Practical, Cost-Effective Steps Toward Digitization
The good news is that modernization does not have to be a costly, disruptive endeavor. Many manufacturers can achieve significant gains simply by better leveraging the data they already collect.
Go Paperless and Enable Real-Time Collaboration
Digital solutions that replace paper-based processes not only improve efficiency but also enhance sustainability. Cloud-based platforms ensure that all teams work from the same source of truth, reducing discrepancies and improving decision-making.
Eliminate Data Silos with Connected Workflows
A significant roadblock for manufacturers is the inability of different systems to communicate. Platforms like Nexus facilitate seamless collaboration by integrating existing workflows into a centralized system. This enables real-time data sharing, enhances efficiency, and reduces the likelihood of errors—without requiring a full-scale infrastructure overhaul.
Digitize Existing Machinery Instead of Replacing It
For SMBs, investing in entirely new machinery isn’t always feasible. However, modern digital solutions can be integrated into legacy equipment, allowing manufacturers to collect and analyze data without costly replacements. Retrofitting existing machines with smart sensors and IoT capabilities can provide real-time insights, predictive maintenance, and greater operational efficiency.
Standardize Processes with Automated Workflows
Inconsistencies in manufacturing processes can erode trust and decrease efficiency. Tools like Metrology Mentor, a Nexus App, help standardize workflows by automating processes, ensuring consistency and repeatability in measurement processes. This reduces the reliance on skilled specialists while improving accuracy and reducing errors.
Improve Workforce Training and Engagement
Modernizing manufacturing is also about empowering workers. Simplifying workflows, reducing training time, and implementing user-friendly digital tools can help bridge the skills gap. New employees, who may not have years of hands-on manufacturing experience, can quickly become productive contributors when armed with intuitive digital solutions.
The Future of Manufacturing: Incremental, Sustainable Innovation
The journey to digitization doesn’t have to be overwhelming. Instead of viewing modernization as an all-or-nothing leap into automation and AI, manufacturers can take a phased approach, integrating digital tools that build upon their existing infrastructure. By eliminating manual processes, reducing data silos, and embracing cloud-based collaboration, manufacturers can future-proof their operations and remain competitive in a rapidly evolving industry.
Digitization unlocks the full value of manufacturing data. By applying AI and advanced analytics, manufacturers can transform raw data into actionable insights, optimizing production, improving quality control, and enhancing overall operational efficiency.
Stephen Graham is Executive Vice President and General Manager of Nexus. He worked for over 25 years in the technology industry before joining Hexagon’s Manufacturing Intelligence Division as Vice President of Marketing in 2017. More recently, he led the Metrology and Production Software Business Unit before being part of the founding team for Nexus – our new cloud platform for digital engineering and manufacturing – which he now leads.
Comments (0)
This post does not have any comments. Be the first to leave a comment below.
Featured Product
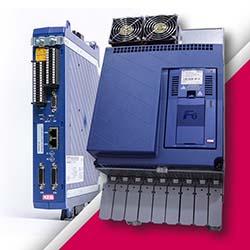