Why the U.S. is Poised to Lead a New Era of Manufacturing
The return of manufacturing to the United States has often been dismissed as a pipe dream. Pundits cite high labor costs, supply chain complexities, and insufficient technological readiness as insurmountable barriers. Yet these arguments miss a critical truth: the U.S. business and labor climate is not only ready to welcome a resurgence of manufacturing but is uniquely suited to thrive in a new era driven by innovation, customization, and resilience; companies just need to do better at identifying and seizing the opportunity. As Protocase embarks on its U.S. expansion—beginning with our new state-of-the-art production facility in Wilmington, NC—we’re seeing firsthand how favorable conditions align perfectly with modern manufacturing methodologies like our proprietary High Velocity Mass Customization (HVMC) approach.
Overcoming Labor Costs with Skill and Technology
Critics argue that high labor costs in the U.S. make it difficult for manufacturers to compete with countries offering cheaper wages. However, this perspective overlooks the strides the U.S. has made in workforce development and technological integration. American workers bring unparalleled expertise and a growing emphasis on technical education and upskilling—a foundation for the precision and agility required in advanced manufacturing.
Protocase’s High Velocity Mass Customization (HVMC) approach, which focuses on producing small quantities of highly customized parts quickly and efficiently, thrives in environments with skilled labor. This methodology doesn’t depend on low-cost, repetitive manufacturing, but on workers who can operate advanced machinery and collaborate in multidisciplinary teams. The U.S.’s renewed investment in vocational training and STEM education ensures a steady pipeline of talent ready to embrace this model.
Moreover, companies like Protocase benefit from the U.S.’s ability to attract international talent. As we scale our operations, we’ve seen how the country’s highly trainable, innovative workforce enriches our ability to deliver complex, precision-engineered solutions.
Supply Chains: From Vulnerability to Resilience
The COVID-19 pandemic exposed the vulnerabilities of global supply chains, and critics cite these disruptions as a challenge for reshoring efforts. Yet the U.S. is uniquely positioned to transform this perceived weakness into a strength. With its vast network of domestic suppliers, robust logistics infrastructure, and focus on localized production, the U.S. enables companies like Protocase to source materials locally and reduce lead times.
Our experience at Protocase illustrates this advantage. By strategically selecting the U.S. for our new production facility, we’re able to tap into a diversified supplier base while shortening supply chains. This setup enhances our ability to meet tight deadlines—a cornerstone of HVMC—and ensures we can pivot quickly in response to customer needs or market shifts. Additionally, by manufacturing domestically, we’re reducing our reliance on international shipping, which has become increasingly volatile and expensive.
Infrastructure and Energy: A Competitive Edge
Concerns about aging infrastructure and high energy costs are often cited as deterrents to manufacturing in the U.S. However, recent federal initiatives such as the Infrastructure Investment and Jobs Act have catalyzed significant improvements in transportation, broadband, and clean energy. These upgrades are particularly advantageous for advanced manufacturing facilities that depend on reliable logistics and power.
Protocase’s U.S. facility benefits directly from these advancements. Enhanced infrastructure facilitates the seamless delivery of materials and finished goods, while investments in renewable energy and energy efficiency help mitigate operational costs. For manufacturers like us, the U.S. is becoming an increasingly attractive environment to innovate and grow sustainably.
Take North Carolina specifically, manufacturers are successfully leveraging access to modern port facilities, which play a crucial role in their ability to efficiently move specialized materials and equipment. The state’s commitment to upgrading infrastructure ensures they can meet the demands of customers in a wide array of industries.
A Favorable Business Climate
Another common critique is that regulatory hurdles and corporate taxes deter manufacturing investment in the U.S. Yet recent policy changes, including tax incentives for domestic production and initiatives to boost semiconductor and clean energy industries, have created a pro-business environment. These measures align perfectly with Protocase’s expansion goals and demonstrate the government’s commitment to fostering a thriving manufacturing sector.
Moreover, the U.S.’s stable political and economic environment provides a level of certainty that is hard to find in other markets. For companies employing cutting-edge methods like Mass Custom manufacturing, this predictability is invaluable for long-term planning and investment.
The U.S. also benefits from robust intellectual property protections, a critical factor for companies innovating in advanced manufacturing. Protocase’s customers, many of whom operate in sensitive industries like aerospace and defense, value the confidence that their designs and technologies are safeguarded under U.S. law.
Embracing a New Era of Manufacturing
Far from being a liability, the U.S. labor and business climates are prime for driving a renaissance in manufacturing. Companies like Protocase are leading the way by leveraging advanced methodologies that align with the strengths of the American workforce and infrastructure. Our High Velocity Mass Customization approach, which emphasizes speed, flexibility, and efficiency, thrives in the U.S. because it capitalizes on the very factors critics claim are barriers.
The conversation about reshoring manufacturing has been dominated by outdated paradigms. It’s time to recognize that the conditions have fundamentally changed. The U.S. is no longer competing on the metrics of low-cost, high-volume production; it is excelling in innovation-driven, high-value manufacturing. Protocase’s expansion into the U.S. underscores this shift, and we’re excited to be part of a new chapter in American industry—one defined by resilience, ingenuity, and opportunity.
With over 35 years immersed in the realms of technology and innovation, Steve Lilley has steered the creation and expansion of numerous tech-driven enterprises. Presently, he serves as the President of Protocase Incorporated, a pioneering manufacturing venture he co-founded in 2001, and as the director of 45 Drives Limited, another technology-focused business established in 2012. In 2023, Protocase launched ProtoSpace Manufacturing, a division dedicated to serving engineering and innovation in aerospace and defense.
Protocase Inc. is a leading innovator in the rapid manufacturing and prototyping industries, specializing in the production of custom electronic enclosures and precision metal components for sectors including aerospace and defense. Founded in 2001, Protocase has been at the forefront of providing cutting-edge solutions for a diverse range of industries, including science, engineering, and technology. The company's unique mass custom manufacturing process is fast, flexible, and easy, offering precision sheet metal fabrication, CNC machining, and 3D printing services under one roof. With a clientele spanning more than 18,000 clients worldwide, including renowned organizations such as NASA, Stellantis, Massachusetts Institute of Technology, Tesla, and Amazon Web Services, Protocase continues to set the standard for excellence in the manufacturing sector. Protocase is the parent company of 45Drives, a leading open-source data storage company, and to ProtoSpace Mfg, and Protomentum.
Comments (0)
This post does not have any comments. Be the first to leave a comment below.
Featured Product
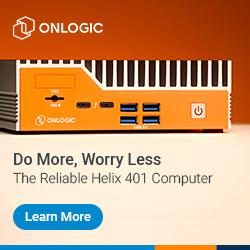