7 Emerging Solutions for Reduced Manufacturing Downtime in 2025
Downtime is a perennial problem for manufacturers. While the industry has made significant strides in boosting uptime, unexpected hiccups still happen, and their costs keep climbing. Thankfully, technology continues to offer novel solutions.
Manufacturers hoping to reduce downtime more effectively in 2025 should pay attention to several emerging trends. Here are seven such technologies and strategies for greater uptime this year and beyond.
1. Prescriptive Analytics
Predictive maintenance (PdM) has been the most significant downtime-related tech trend for several years now. As it reaches mainstream adoption, though, manufacturers can go further. Cutting-edge artificial intelligence (AI) applications enable prescriptive analytics to follow up on predictive solutions.
Whereas predictive analytics indicate what may happen in the future, prescriptive models suggest appropriate responses to such predictions. Incorporating this functionality into a PdM solution could have substantial benefits. Instead of simply alerting technicians of an issue, AI would tell them what the optimal fix may be, streamlining the repair process.
Nearly half of all major manufacturers now use PdM. As such, the technology has reached a point of maturity where there’s enough data, expertise and experience to develop more advanced functions. Prescriptive insights are the logical next step.
2. Edge Computing
As manufacturers embrace PdM and other Internet of Things (IoT) technologies, they may run into higher, difficult-to-manage data volumes. Analyzing and responding to so much real-time information quickly enough to prevent malfunctions is challenging with conventional setups. Edge computing may hold the answer.
In an edge environment, IoT devices distribute computing tasks among themselves instead of processing data in a remote data center. The result is faster performance and the ability to perform complex calculations despite hardware lacking significant onboard power. In some scenarios, edge computing can reduce latencies by up to 30%, bringing needed agility to Industry 4.0 functions.
PdM will be far more reliable with such power and speed gains, as there’s minimal delay between a warning sign and the IoT device’s alert. Applications like AI quality control and robotics also benefit. The edge ensures they can respond to changing circumstances faster, avoiding potential errors that may cause downtime.
3. Green Backup Power Solutions
Even the most robust manufacturing process may be vulnerable to downtime from external factors. Power outages and similar grid reliability issues are a prominent example, especially as the nation’s electrical infrastructure ages. Manufacturers in 2025 can mitigate this threat through green backup solutions.
Backup power is essential to keep running in a blackout, but conventional generators are falling out of favor. Hydrogen fuel cells are a promising alternative. In addition to producing no harmful emissions, hydrogen is remarkably energy-dense, so fuel cell generators can run for longer before needing refueling.
Switching to higher-efficiency equipment can also help, as it lets facilities run with less backup capacity. While these upgrades carry high upfront costs, their long-term savings are worth noting. For example, the purchase price of an electric motor is often just 1% of the total cost of ownership, so a less efficient version ends up costing more over time thanks to energy waste.
4. Cobots
Skill shortages are another pressing issue driving downtime in modern manufacturing. The nation faces a shortage of 495,000 automotive technicians alone, not counting other specialists. With fewer workers available, mistakes and bottlenecks are increasingly likely, leading to excess downtime. Collaborative robots (cobots) can help.
Most manufacturers already automate some tasks, but conventional robotics have limits. Notably, they may endanger workers, and they don’t adapt well to changing circumstances. Cobots, by contrast, are designed to work safely and efficiently alongside humans, offering a balance between efficiency and adaptability.
Opting for cobots instead of conventional automation helps production lines run smoothly, avoiding downtime that inflexible robots may cause. Newer cobot models with modular components and plug-and-play programming offer additional uptime potential, as they’re easier to implement and maintain.
5. Product Passports
Manufacturers in 2025 must also turn their eyes to the supply chain. Geopolitical tensions, weather-related disruptions and other supply-side issues have caused downtime throughout previous years, so adaptation is necessary. It should be no surprise, then, that 85% of CTOs and engineering heads say next-generation supply chains will be one of the biggest tech trends of 2025.
Tracking solutions — specifically, digital product passports — are among the most impactful of these technologies. Product passports provide a digital record of their origins, ownership and official scans throughout their life cycle. While they’re primarily a sustainability-focused innovation, manufacturers can use them to store supply chain data for more insightful tracking.
Product passports carrying data on their origins and each shipping stop help fight fraud and maximize transparency. As a result, supply chains will be able to adapt and function with fewer disruptions by responding to such insight.
6. IoT Security
Cyberattacks are another cause of downtime deserving more attention in the coming years. The manufacturing industry experienced 25.7% of all cybersecurity incidents in 2023, making it the most-attacked sector for the third consecutive year. Consequently, advanced security controls have become a critical downtime prevention measure.
The IoT deserves special attention. Smart devices are common weak points, and cybercriminals can use them as gateways to more sensitive endpoints and data. Manufacturers can address this concern by encrypting all IoT traffic, segmenting networks and using multi-factor authentication on all smart endpoints.
Sophisticated protections like automated network monitoring may also be necessary. AI cybersecurity tools can recognize potential breaches and contain them immediately, preventing an IT-related downtime event before it can do much damage.
7. Data Governance
Similarly, manufacturers can maximize uptime by taking greater care of their data. While it often goes unnoticed, low-quality or unsecured data has significant implications for overall productivity.
Duplicate or unreliable information in an AI application like PdM will limit the solution’s accuracy, potentially leading to false positives or missed warning signs. Likewise, poor-quality data will hinder the reliability of any digital twin analysis or supply chain tracking. Consequently, manufacturers can avoid frequent missteps and related downtime by ensuring higher data quality standards.
Automated data cleansing processes are a good first step. In some cases, manufacturers can avoid the limitations of real-world data by using a synthetic dataset, which sometimes makes AI models even more accurate than authentic information. Greater visibility into data storage locations and access permissions will help further by informing needed cybersecurity improvements.
2025 Could Be a Landmark Year for Manufacturing Uptime
The manufacturing industry still suffers from downtime incidents, but recent technology trends have helped many organizations minimize such disruption. Continuing to look for opportunities to improve and staying at the forefront of Industry 4.0 tech will ensure manufacturers keep going in the right direction.
These seven solutions showcase how capitalizing on emerging tech can reduce downtime more than ever before. The sector could set new standards of productivity and cost-effectiveness if enough facilities embrace such changes.
Comments (0)
This post does not have any comments. Be the first to leave a comment below.
Featured Product
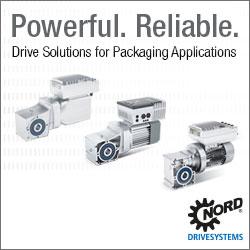