Examining the Integration of Hydrogen Fuel Cell Tech in the Manufacturing Supply Chain
Hydrogen fuel cells have gained rising popularity as sustainability efforts have grown. While much of this interest has been in the area of consumer transportation, hydrogen’s potential extends far beyond the everyday commute. Fuel cells also hold considerable promise for manufacturing supply chains.
Many, if not all, manufacturers today recognize the need to revamp supply chains. Improving sustainability, increasing efficiency and lowering operational costs are key elements of this change, and hydrogen fuel cells can help in each area.
Hydrogen Fuel Cell Applications in the Supply Chain
Before investing in hydrogen fuel cells, manufacturers must first recognize where they can implement them. While road vehicles may be the most obvious use case, fuel cells can drive value in several supply chain operations.
Zero-Emissions Transport
One of hydrogen power’s greatest strengths is its ability to enable zero-emissions transportation. Fuel cells convert hydrogen into electricity, emitting nothing other than heat and water. Considering how transport accounts for 80% of logistics emissions, that potential is difficult to overlook.
Many transportation sustainability solutions focus on battery-electric vehicles (BEVs), but these are not ideal for many supply chain operations. BEVs typically have limited ranges and long recharging times, rendering them impractical for long-distance shipping. Fuel cell electric vehicles (FCEVs) don’t share this obstacle.
FCEVs are even more efficient than combustion engines, making them optimal for long-range applications. Such efficiency means they could power ships and airplanes, not just trucks, making them a better big-picture solution for manufacturing supply networks. It will take time to shift all transport types to hydrogen power, but it’s at least possible.
Sustainable Port and Warehouse Operations
Manufacturers could also implement fuel cell technology in non-transport workflows. Port and warehouse processes typically rely on diesel power, too. Consequently, they could likewise see marked improvements from embracing zero-emissions alternatives.
Fuel cells have benefits beyond removing greenhouse gases (GHGs) from these operations. The EPA highlights how the technology can also reduce noise and lower maintenance requirements in busy ports. These advantages, in turn, would foster safer, more productive workplaces.
Hydrogen is particularly valuable as a diesel replacement in off-grid generators. Fuel cell generators can let port or warehouse equipment use electricity without requiring a connection to the national electric grid. Manufacturers can erect new infrastructure or set up temporary operations with less disruption as a result.
Carbon-Free Facility Power
Some manufacturing plants could apply hydrogen energy on a larger scale. Instead of merely powering mobile equipment with fuel cells, they could use the technology to provide entire facilities with grid-independent, carbon-free electricity.
Locally produced electricity is not a novel concept. Many factories already use rooftop solar to power at least some of their operations for sustainability or cost reasons. On-site hydrogen generators could fill the same niche without solar’s dependence on the weather.
Unlike wind and solar, fuel cells can provide energy on demand, including at night. This resilience is particularly promising in the context of emergency backup power. U.S. grids experience 5.5 hours of electricity interruptions annually, heightening the need for backups, which hydrogen can provide — regardless of outside conditions.
Benefits of Hydrogen Fuel Cell Integration
Across all of these use cases, manufacturers have much to gain from implementing fuel cells in their supply chains. The most obvious is a path toward greater sustainability. Manufacturing is responsible for 12% of U.S. GHG emissions, and experts predict this carbon footprint will grow in the future. Decarbonizing the supply chain is a critical step amid that trend, and hydrogen makes it possible.
Fuel cells are certainly not the only zero-carbon source of electricity, but they’re a particularly beneficial one in supply chain operations. Renewables like wind and solar still have roles to play, but they cannot sustain production because they’re intermittent. Hydrogen is not, so it can reduce GHG emissions without sacrificing around-the-clock productivity.
FCEVs’ extended ranges are another crucial advantage. Some commercially available hydrogen trucks can travel up to 450 miles without refueling. When they do need to refuel, they do so in minutes instead of the hours it takes a BEV to recharge. As such, FCEVs are a more practical replacement for diesel trucks than battery alternatives.
Hydrogen is also remarkably energy-dense. This quality could enable manufacturers to store large amounts of fuel on-site to power backup generators or primary electrical systems without much additional infrastructure. In addition to easing the green energy transition, that could reduce ongoing expenses by decreasing factories’ reliance on the grid.
Remaining Challenges in Fuel Cell Adoption
As beneficial as fuel cells can be in manufacturing supply chains, several obstacles remain. One of the most significant is the availability of hydrogen alternatives. While hydrogen trucks are slowly coming to market, there are relatively few models available, and fuel cell-powered planes and ships are mostly experimental for now.
Hydrogen refueling infrastructure poses a similar challenge. There are only 59 open retail hydrogen stations in the U.S. today. Consequently, even if a manufacturer or their supply chain partners use fuel cell trucks, they’d likely need to implement their own refueling stations, limiting the rollout of this technology.
High costs are another barrier. Fuel cells are an advanced technology and, as such, come with a price premium. While operational expenses may fall over time from increased efficiency and grid independence, the initial investment may slow adoption.
It’s also worth noting that not all hydrogen is 100% emissions-free. Because hydrogen does not occur on its own in nature, it requires separation from other elements, which takes energy. This process often involves fossil fuel-derived electricity, so fuel cell power still carries a carbon footprint, albeit a smaller one than direct fossil fuel use.
The Future of Hydrogen in the Manufacturing Supply Chain
Several changes are on the horizon that may offer ways around these barriers. The federal government allocated $9.5 billion in funding toward climate projects in 2022. Such a boost in financial support could lead to the expansion of hydrogen refueling stations or the development of more FCEVs.
Similarly, costs will fall as technology advances. Recent research suggests fuel cell expenses will fall even faster than battery prices over the coming decades. As this trend continues, it will become easier for manufacturers and their supply chain partners to justify investing in hydrogen power.
Manufacturers hoping to experience fuel cells’ benefits to the fullest should target green hydrogen specifically. This term refers to hydrogen derived using renewable power, making the fuel truly emissions-free. While it accounts for a relatively small percentage of fuel cell energy today, it could grow with increased investment.
Fuel Cell Technology Could Enable a Greener Industry
The path to sustainable manufacturing will likely require the implementation of several technologies. Hydrogen-powered vehicles and electrical systems may not be a complete solution, but they may play an important part in the overall puzzle. Learning how to apply this technology in supply chain operations is the first step in capitalizing on that potential.
Comments (0)
This post does not have any comments. Be the first to leave a comment below.
Featured Product
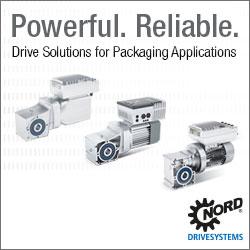