Top Manufacturing Trends Looking Into 2025
The manufacturing industry thrives on competition. If you can keep up with the digital transformation, emerging technology, and workforce changes, you can leverage opportunities to boost operational efficiency and put competitors in your rearview mirror. Here are the latest manufacturing trends to help you start the journey to machine shop excellence.
Digital Transformation in Machine Shops
Data insights, robotics, and process-built automation — digital transformation is the name of the game for machine shops. Applying these modern manufacturing practices has drastically helped shop floors meet ambitious production quotas, put mundane manual processes on autopilot, and serve dynamic customer needs with precision. So, how are digital transformations reshaping production machining cycles in the manufacturing world?
The Role of Data and Analytics
Data plays a huge role in achieving machine shop excellence. It's the knowledge you need to innovate and evolve production lines — ensuring continuous improvement and customer satisfaction. As one Hexagon customer put it, "The more data we gather from every step of the process, the better we can refine and improve it."
It's why so many modern manufacturers are embracing data-centric technology:
- IoT sensors for real-time production monitoring
- Artificial intelligence (AI) for improved data analysis on production machining cycles
- Integrated production machining software to tear down data silos between teams Shared quality and process reporting tools
Data-centric infrastructure ultimately produces real-time analytics for machine shops. The result: Enhanced operational efficiency across the whole value chain.
- Faster, more informed decisions to innovate for smarter manufacturing
- Easier to spot and fix bottlenecks in the production machining program
- Quality teams can quickly detect deviations from standards for swift remediation
- Real-time insights for predictive maintenance to avoid production downtime
- Machine shops can stay agile to customer needs for better flexibility and product customization through predictive data
Automation and Robotics
Machine shops are plagued with nuanced operational roadblocks: Labor shortages, skills gaps, high production quotas, and rigorous quality standards — the list goes on and on. The good news is that automation is coming in to save the day. It's the X-factor for cutting out tedious manual processes, enhancing productivity, and reducing errors in production machining cycles. Here are a few real-world examples of the power of automation:
ADFL generates faster, more precise job quotes by deploying an automated system for time analysis, production cost estimation, and quote generation. Omega Enterprises reduces cycle times by 50% by using CAD/CAM software to automate manufacturing preparation rather than manually tracing parts.
Wabtec cuts quality costs by 35% with automated reporting and insights that spot process defects faster.
We also can't overlook the latest advancements in robotics. They've enabled machine shops to free up personnel for more creative and complex work. For example, manufacturers can deploy robotic systems for packing, loading, and unloading inventory or materials. There are also automated guided vehicles (AGVs) to help transport parts across facilities and collaborative robots that can help teams with quality inspection, tracing, and other activities requiring precision.
Advanced Manufacturing Technologies
Every machine shop thrives on fostering innovation and improving production efficiency. And thanks to some of the latest technologies, including 3D printing, IoT sensors, and integrated production machining software, manufacturing processes have never been so agile.
Additive Manufacturing (3D Printing)
Additive manufacturing through 3D printing has completely changed the way machine shops operate, particularly during the preparation and setup phases. It's both cost-friendly and sustainable for rapid prototyping — allowing for seamless lightweighting and part consolidation. 3D printing even supports operational agility as shops can quickly prototype personalized products for on-demand production.
In one great success story, Omega Enterprises was able to trim part duplication in half (from 40 hours to 20 hours per duplication) by creating and printing 3D replicas of glass bottles — letting them start machining sooner and accelerate the entire production machining program.
Additive manufacturing and digital simulation continue to impact the industry tremendously. Thanks to 3D printing, companies can streamline setup through dynamic fixture and jig creation. And the technology itself is only improving. You're now seeing enhanced capabilities like large-scale 3D printing for producing huge components at scale and machines able to produce parts faster and more efficiently without compromising quality.
Internet of Things (IoT) and Smart Factories
IoT devices, integrated sensors, and data analytics are unlocking excellence on machine shop floors. Imagine getting real-time monitoring capabilities on production status, quality deviations, energy usage, materials, and system bottlenecks. Or being able to predict precisely where your production cycle is about to break down. Or have access to order, design, and inspection data on a mobile device from anywhere in the facility.
That's precisely what today's smart factory looks like. It has unmatched visibility on the entire value chain and enables an interconnected operation between sales teams, designers, engineers, production lines, quality managers, and other personnel.
Workforce Transformation and Skills Development
Technology advances and production systems evolve, but has the workforce caught up? Modern manufacturing demands continuous learning to keep pace with industry changes. The result: Machine shops have made hefty investments in upskilling, reskilling, and digital training programs.
Upskilling and Reskilling Programs
When emerging tools make their way into machine shops, you need a workforce who knows how to use them. Hence the need for upskilling and reskilling programs. Your new, shiny tools are obsolete if the machine shop team can't operate or troubleshoot issues with them. So manufacturers are investing to close potential skills gaps and empower workers to stay productive and adapt to new tech. It's estimated that over $26 million was spent by manufacturers in 2023 on training programs.
In an industry plagued by labor shortages, adopting cutting-edge technology and automation is a great way to attract and retain talent. Most people don't want to get stuck doing mundane work all day when a robot or production machining software can take the burden off.
Embracing Digital Tools for Training
Digital platforms empower workers with fast and safety training. Investing in digital twin technology, for example, lets users simulate operations and day-to-day activity in a virtual setting without physically impacting the manufacturing process. Virtual reality (VR) is making headway with immersive, hands-on training experiences that let operators hone their skills in a safe environment. Embracing digital tools is not only more cost-effective for training but also more efficient.
Alpha Precision saw firsthand how digital tools streamline training. When they struggled with small-detail finishing, they adopted CAD/CAM software with built-in training modules and had help from Hexagon virtual training programs to put operators on the path to success.
Will Your Machine Shop Fall In Line or Fall Behind?
Your machine shop has a choice. Embrace the latest manufacturing trends for sustained business growth and competitive advantage, or fall behind and see your bottom line deteriorate. Luckily, you can start your journey to modern manufacturing and enterprise success by closely following and keeping up with the latest manufacturing trends in the new year.
Comments (0)
This post does not have any comments. Be the first to leave a comment below.
Featured Product
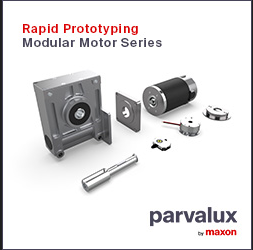