How manufacturers can apply smart buildings technologies to decarbonize operations
Industry 5.0, the Fifth Industrial Revolution, and the availability of digital and automation solutions such as artificial intelligence (AI), the Internet of Things (IoT) and Big Data, have given resource and emissions-heavy industries complete visualization and control over every stage of the value chain, empowering them to make smart, data-driven decisions that improve efficiency and sustainability.
The latter issue is especially pertinent as industry looks to decarbonize operations and reduce energy consumption in line with treaties such as the landmark 2015 Paris Agreement on climate change. At present, a fifth of the world’s CO2 emissions come from the manufacturing and production sectors1.
ABB’s technology and digital solutions are meeting the growing needs of customers making the transformation to decarbonized operations. ABB Ability™ Building Analyzer offers energy savings of up to 20% along with emissions reduction and maintenance cost savings. BACnet/IP Gateway connecting ABB’s Cylon® HVAC system with the ABB i-bus® KNX Room Automation system can reduce energy consumption by up to 25%, lower energy costs and CO2 emissions while preserving thermal comfort and air quality. Our InSite energy management system makes any energy distribution board smart and enhances energy efficiency through improved load management, scalability and predictive maintenance.
However, in the race to decarbonize, businesses must not ignore another environmental imperative, that of recycling and zero waste to landfill.
States of play: US industrial waste legislation
As the world’s largest economy and one of the largest producers of waste worldwide, the US has a leading role to play in establishing stringent yet realistic guidelines around the circular economy.
The US Environmental Protection Agency (EPA), which regulates industrial and manufacturing solid and hazardous wastes under the Resource Conservation and Recovery Act, reports that each year approximately 7.6 billion tons of industrial solid waste are generated and disposed of in the US3.
The EPA estimates that the US has a combined recycling rate (industrial, commercial and residential trash) of just 32% for materials including glass, plastic, cardboard and paper4. The situation is further challenged by a somewhat fragmented regulatory framework governing industrial waste; for example, the definition of ‘zero waste’ can vary from state to state and from entity to entity5.
However, there are encouraging signs that companies are being proactive around the environment. In 2022, the EPA reported over 3,400 pollution prevention activities at 1,674 manufacturing facilities to reduce toxic chemical use and waste creation. Interestingly, the most commonly reported type of pollution prevention activity was process and equipment modifications. The EPA cites an example of a fabric coating mill that implemented a new enterprise resource planning (ERP) system in 20225, improving onsite inventory management and helping reduce the amount of waste being managed.
ABB’s mission to decarbonize operations
As a supplier of digital and engineering technologies , ABB is committed to simplifying and optimizing industrial waste management and recycling.
In 2019, ABB launched Mission to Zero™, which began as a pilot concept at the company’s plant in Lüdenscheid, Germany, to make operations more sustainable. Mission to Zero™ is a blueprint for smart building solutions, bringing together technologies using ABB digital solutions and renewable energy to increase efficiency and reduce emissions. Powered by people passionate about driving a more resource-efficient future, Mission to Zero supports ABB’s commitment to reach net zero by 2050 and customers’ Scope 3 emissions reduction targets.
Investing in the circular economy
ABB Electrification Smart Buildings recently celebrated sustainability successes with three manufacturing facilities achieving the highest ‘platinum’ rating from UL Solutions for zero waste to landfill operations, reflecting the company’s commitment to send zero waste to landfill from its own operations by 2030.
The rating under the UL 2799A Environmental Claim Validation Procedure, for Zero Waste to Landfill Operations was awarded to facilities in Rakovski, Bulgaria, Santa Palomba, Italy and Beijing in China, which manufacture low-to-medium voltage products, among other solutions. They now divert 100% of waste from landfill, meaning all generated waste is reused, recycled, composted or repurposed.
The Platinum rating follows the Santa Palomba and Rakovski sites’ Mission to Zero™ achievement. These achievements not only underline the ability of digitalization to improve sustainability and production, but also the importance of fostering a company culture that prioritizes sustainability at every level.
Each of the ABB sites conducted a comprehensive lifecycle analysis of raw materials, covering all phases from production and use to waste disposal. As a result, a range of waste reduction, reuse and recycling initiatives were implemented at every operational stage, including optimizing chemical use, reducing hazardous waste and increasing the recycling of plastic packaging. Some of the waste is also thermally processed and recovered for use as energy within ABB’s production lines, contributing to a more sustainable manufacturing process9.
These sustainability wins demonstrate that real change is possible when it comes to accelerating the transition to a circular economy. With meaningful investment in digital, electrification and automation technologies, manufacturers in the US and around the world can reduce their carbon footprint, comply with evolving environmental legislation and contribute to a cleaner, safer world.
Sources:
1. https://www.weforum.org/impact/carbon-footprint-manufacturing-industry/
2,7,,9 Global waste generation - statistics & facts | Statista
2 https://www.epa.gov/transforming-waste-tool/how-communities-have-defined-zero-waste
3 https://www.epa.gov/sites/default/files/2016-03/documents/industrial-waste-guide.pdf
5 https://www.epa.gov/transforming-waste-tool/how-communities-have-defined-zero-waste
6 US EPA
Comments (0)
This post does not have any comments. Be the first to leave a comment below.
Featured Product
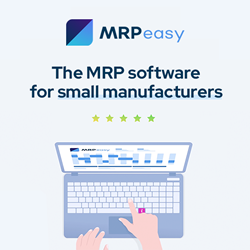