How Robotics and Energy Management Systems Can Collaborate to Achieve Zero-Energy Manufacturing
- Companies can achieve net-zero energy output by balancing energy produced and consumed through advanced robotics and energy management systems (EMS).
- Utilizing robotic automation in manufacturing increases production efficiency and energy savings, reducing overall energy consumption.
- Effective energy management systems optimize real-time energy use, integrate seamlessly with robotics, and ensure operational energy efficiency.
- Emerging technologies in robotics and EMS drive the evolution toward zero-energy manufacturing, enhancing sustainability and competitiveness.
Zero-energy manufacturing aims to create a balance between the energy produced and the energy consumed within a facility, ultimately achieving a net-zero energy output. As industries increasingly focus on sustainability, the intersection of robotics and energy management systems (EMS) has become crucial. This collaboration enhances manufacturing efficiency while playing a pivotal role in reducing energy consumption and minimizing environmental impact.
Unsurprisingly, the manufacturing sector is one of the largest consumers of energy worldwide, accounting for approximately one-third of global energy usage. Traditional manufacturing processes often exhibit significant energy inefficiencies, ranging from outdated machinery to poor system integrations that lead to excessive energy waste. Addressing these inefficiencies is essential for industries aiming to reduce operational costs and environmental footprints.
Modern manufacturing increasingly relies on robotics to improve production efficiency and quality. From articulated robotic arms to autonomous guided vehicles, these systems are pivotal in streamlining operations and reducing manual intervention. The benefits of robotics extend beyond labor substitution, offering precision and consistency which, in turn, can lead to significant energy savings when properly integrated with EMS.
Energy Management Systems (EMS) in Manufacturing
At the core of an effective EMS are components like smart sensors, real-time data analytics, and energy control units, all designed to optimize energy use. These systems provide a data-driven approach to monitor and adjust energy consumption in real-time, identifying areas where energy can be saved without compromising production output.
Integrating robotics with EMS allows for real-time energy monitoring and management of robotic systems. Adaptive control algorithms can dynamically adjust operations based on energy demand and availability, promoting energy-efficient manufacturing practices. Predictive maintenance facilitated by EMS can preemptively address potential malfunctions in robotic systems, which might otherwise lead to unplanned energy spikes.
The inclusion of oil and gas ERP systems in this integration supports the strategic deployment of resources, enhancing the energy efficiency of operations across the board.
A relevant, real-world example of robotics and energy management systems integration in manufacturing that showcases significant energy savings and efficiency improvements was highlighted in the Journal of Manufacturing Technology Management, which detailed the implementation of collaborative robots (cobots) in assembly processes in the automotive industry. This integration focused on optimizing production lines by balancing robot and human tasks, which effectively minimized total production costs while enhancing energy efficiency and resource utilization.
For instance, the integration of plug-and-produce (PnP) concepts, facilitated by Industry 4.0 technologies such as industrial IoT and big data, led to significant improvements. The application of these technologies enabled at least a 20% decrease in reconfiguration time, a 12.5% increase in resource efficiency, and a 15% reduction in costs. These benefits are directly attributable to the dynamic and efficient allocation of tasks and the automated adjustments of energy consumption, demonstrating the substantial potential for energy savings in a well-integrated robotic system
Challenges, Solutions, and Future Trends
Despite the clear benefits, integrating robotics with EMS presents several technical challenges, including compatibility issues and the complexity of retrofitting old machines with new technologies. However, solutions such as modular system design and phased implementation strategies can effectively mitigate these hurdles, enabling manufacturers to gradually integrate advanced technologies without disrupting existing operations.
The future of manufacturing lies in the continued evolution of both robotics and EMS technologies. Innovations such as AI-driven robots and more sophisticated energy predictive analytics are on the horizon, promising further advancements toward zero-energy manufacturing. These technologies not only aim to minimize energy consumption but also enhance the overall sustainability and competitiveness of manufacturing industries.
The integration of robotics and EMS represents a significant step forward in achieving zero-energy manufacturing. By harnessing the power of these technologies, manufacturers can significantly reduce energy usage, decrease operational costs, and contribute to a more sustainable industrial future. The journey toward zero-energy manufacturing is complex and challenging, but the potential rewards for competitiveness and environmental stewardship are immense.
Vince Dawkins, President and CEO of Enertia Software, has worked with industry-leading organizations, and he has been integral in developing the Enertia application into a resource used by over 150 leaders in the upstream oil and gas industry.
Comments (0)
This post does not have any comments. Be the first to leave a comment below.
Featured Product
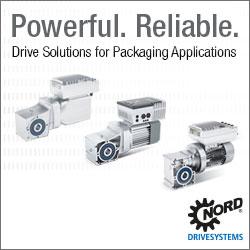