Artificial Intelligence: The Game-Changer Manufacturers Can't Afford to Ignore
In today’s rapidly evolving manufacturing landscape, Artificial Intelligence (AI) is emerging as a transformative force with the potential to revolutionize productivity, efficiency, and innovation, while maintaining customer satisfaction as the guiding principle for every decision.
Companies embracing AI-powered machine learning (ML)and data analytics are already seeing significant benefits including streamlined operations, improved predictive maintenance and optimized supply chains. In fact, 73% of manufacturers report reduced costs and improved efficiency after deploying AI technology. Additionally, AI-driven automation is enhancing production lines with robotics and smart machinery boosting both precision and output.
Yet, despite its promise, AI adoption within the sector continues to lag behind other industries, as the “if it ain’t broke, don’t fix it” mentality continues to reign supreme. This is, in addition, to persistent industry challenges such as the need for skilled talent, hesitation around accuracy and potential risks, fear around what AI means for the jobs market and integration with legacy systems. And most recently, the introduction of Generative AI (GenAI) is adding more fear and confusion to the manufacturer wondering how to approach AI.
This hesitation, while understandable, risks leaving the US manufacturing industry behind in an increasingly competitive global market. So how do manufacturers break the cycle and tap into the power of AI?
Main Challenges to AI Adoption
One of the primary concerns for domestic manufacturers is integrating AI with existing systems. Most manufacturing plants operate on legacy equipment and software that have been in place for decades. Upgrading or connecting or integrating these systems to work with AI can be a complex, costly, and time-consuming process, often requiring downtime – a luxury many manufacturers feel they can't afford in today's competitive market. Additionally, ensuring seamless integration between new AI systems and existing ERP or MES can present additional technical challenges.
Data quality and availability also pose significant challenges. AI systems are only as good as the data they're fed, and many manufacturers struggle with data silos, inconsistent data formats, or simply a lack of sufficient historical data to effectively train AI models.
The introduction of AI also necessitates substantial workforce upskilling. Employees need to adapt to new ways of working, which can be daunting, particularly in regions where skilled workers are already in short supply. That said, it's not just about training workers to use new technologies; it's about fostering a culture of continuous learning and adaptability, which can be a significant shift for traditional manufacturing environments.
Finally, the upfront investment required for AI implementation, coupled with uncertainty about return on investment and access to skilled data scientists, can be a significant barrier, especially for small and medium-sized enterprises.
Tapping into the AI goldmine
Despite these challenges, the potential benefits of AI are too significant to ignore. AI-powered predictive analytics, for instance, can anticipate equipment failures before they occur, minimizing downtime and reducing maintenance costs. This capability alone can have significant impact to a manufacturer in dollars saved annually and boosts in productivity.
Robotics and automation, enabled by AI, are streamlining production lines across the country. These technologies are increasing efficiency, improving product quality, and allowing for greater flexibility. AI-driven robots can work around the clock, perform tasks with incredible precision, and adapt to new production requirements much faster than traditional manufacturing methods.
Beyond the factory floor, AI is transforming supply chain management. By analyzing vast amounts of data from multiple sources, AI/ML can optimize inventory levels, predict demand fluctuations, and even suggest alternative suppliers in case of disruptions. This level of insight and adaptability is crucial in today's volatile global market.
Future Directions
But the true potential of AI goes beyond these applications. By injecting intelligence into every part of the business, manufacturers will see an increase in productivity and flexibility in production processes and better planning in an unpredictable business landscape.
To break the cycle of hesitation, manufacturers need to start small but think big. Begin with pilot projects in areas where AI can deliver quick wins, such as predictive maintenance, product recommendations, price optimization or forecasting. Use these successes to build confidence and gather support for additional AI or GenAI initiatives.
Invest in workforce development. Partner with local educational institutions to develop programs that will create the skilled workforce needed for an AI-driven future. Remember, AI is not about replacing workers; it's about augmenting their capabilities and freeing them to focus on higher-value tasks.
Finally, don't try to go it alone. Partner with the right technology experts and their expertise and data scientists to leverage the experience of early adopters. The future of US manufacturing lies in embracing AI – not as a threat, but as a powerful ally in the quest for innovation, efficiency, and global competitiveness.
Imagine a manufacturing plant where every machine, every process, and every decision is informed by real-time data and predictive analytics. Such a facility could dynamically adjust production schedules based on incoming orders, market demand, and available resources. It could optimize energy usage, reduce waste, and even predict and prevent potential quality issues before they occur.
The message is clear: the future of manufacturing isn’t just smart – it’s artificially intelligent.
Comments (0)
This post does not have any comments. Be the first to leave a comment below.
Featured Product
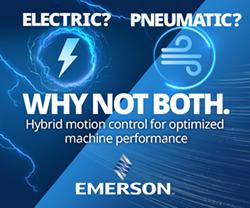