Experience Unprecedented Visibility With AI-Powered Production Monitoring
Manufacturing leaders increasingly deploy artificial intelligence in all facets of their business. Many find AI particularly valuable for production monitoring because it prevents downtime and ensures high product quality. How can and do people benefit from AI in medical device manufacturing?
Supporting Employees
Many of the most practical AI applications for manufacturing support people in their routine tasks, such as by helping them do inspection tasks faster or freeing up their time to do more value-added duties, while artificial intelligence handles the more repetitive ones.
Some companies use AI to analyze when people are overly tired and may need to take breaks. Wearable devices can track employees’ heart and respiration rates and then vibrate or otherwise alert people that they are overextending themselves and need to rest or engage in less-intensive tasks for a while.
Providing Real-Time Feedback
In one example, a manufacturer’s health and safety team tested a keyfob-sized wearable that detected when users adopted positions or movements that could cause strains or sprains if not corrected. Corporate leaders primarily wanted to reduce spine injury risks among warehouse team members.
The technology monitored for twisting, awkward bends, repetitive motion and more. Users then heard beeps or felt vibrations that urged them to correct those actions. That ongoing feedback encouraged them to learn from their mistakes and adopt healthier workplace practices. It took only a short time for executives to see impressive results. Within a few weeks, 62% of workers at one warehouse engaged in at least 50% fewer hazardous movements per hour.
Applying AI to such solutions can allow decision-makers to track trends and see specific details about individual employees. They could then use the insights to change aspects such as workstation heights or material handling training curriculums. Some artificial intelligence-driven solutions also detect if someone falls or otherwise needs emergency assistance.
In one medical industry example, a fall-prevention system flagged unaddressed events within 90 seconds, alerting all nurses to investigate. Manufacturers could adopt a similar system, particularly if many workers risk falling, getting crushed by machinery or similar dangers.
Leaders can later review the circumstances surrounding such events and determine if they must make production floor changes to prevent or reduce the chances of those cases happening again. In most cases, artificial intelligence does not replace people. However, it equips them to do their jobs better with fewer negative impacts.
Enabling Better Equipment Oversight
Faulty or worn machinery could cause quality control issues that people do not notice before products reach production. That is especially problematic in the tightly regulated medical device industry, including items that could risk people’s lives if they do not perform as expected. However, using AI in medical device manufacturing could substantially reduce the likelihood of substandard products.
One startup announced a $45 million funding round to increase its technology’s AI capabilities. The solution analyzes industrial equipment’s vibration and frequency patterns to detect production-halting issues before they happen. Company representatives say this approach can eliminate downtime and extend asset life spans.
Assessing Assembly Line Operations With a Color-Coded System
Assembly line downtime can be prohibitively costly for medical device manufacturers and those associated with other high-demand industries. However, AI can flag problems sooner, preventing stoppages or shortening their durations.
One example comes from an automotive manufacturer that creates color-coded heat maps with machine learning algorithms to visualize potential problems with assembly lines. That approach allows technicians to understand and respond proactively to several fault patterns.
The company monitors approximately 80% of its primary assembly lines this way, which prevents at least 500 minutes of assembly-related downtime per year. Savings are substantial since vehicles come off the enterprise’s line every 57 seconds.
Medical device manufacturers could oversee their assembly lines with similar methods, increasing the chances of those companies meeting client deadlines and other obligations that allow them to remain competitive in a challenging market.
AI is excellent for helping users extract value from large amounts of data. Many busy decision-makers do not have the time or background to interpret the information without help, but artificial intelligence directs their focus by highlighting potential abnormalities. Some tools make it easier to review key performance indicators and determine whether current operations are on track to meet goals.
Creating a Realistic Test Environment
Some medical device manufacturers are already familiar with testing various scenarios before implementing them in real life. Most do that by working with digital twins, mainly when experimenting with several designs and choosing the best ones to prototype.
One government agency is also creating an AI testbed to familiarize manufacturers with the technology's potential uses. NIST has constructed the Collaborative Robotic Operations Workcell and equipped it with various sensors and data loggers.
This initiative aims to improve process monitoring capabilities for manufacturers, allowing them to take advantage of options that strengthen their businesses. The setup includes two robotic arms that move glass pieces through the steps required to mark and erase them. Those involved with the project indicate the movements are similar to those used during welding and gasket extrusion. Once participants tweak the process and notice measurable gains, they may be more open to applying AI technologies in their medical device factories.
Becoming a High Priority for Today’s Manufacturers
Using AI in medical device manufacturing is an appealing prospect for many, but some leaders may hesitate to implement it. What are the possible consequences of such delays? A June 2024 study suggests decision-makers could find themselves behind peers who have already begun using the technology.
The results indicated 93% of manufacturers identified AI as a high-priority matter over the next year. The respondents comprised senior decision-makers and maintenance professionals in several countries. Using AI for predictive or proactive maintenance strategies was a major trend, with 76.5% of those polled hoping to eventually use them. However, only 8% currently do, showing there is room for significant improvement in the coming years.
Additionally, respondents indicated they will put 44% of their tech budgets toward AI in 2024, and 30% will allocate 51%-75% to it. Interestingly most participants anticipated it would take less than a year to meet their AI goals, with 61% planning on an 11-month timeline.
Any leaders who want to follow suit by prioritizing artificial intelligence this year or soon should begin by determining what they want to achieve with the technology and how they will measure progress. They must also figure out their budgets and whether they will roll out the AI gradually to see if it gives the desired return on investment.
Managers and others involved should also keep employees informed by explaining how their jobs or processes will change. Staying focused on the positives while addressing concerns is an excellent way to encourage workers to feel upbeat rather than nervous about the upcoming tech changes.
AI in Medical Device Manufacturing Supports Success
Artificial intelligence is a valuable technology for better production monitoring in medical device factories. The sooner leaders identify problems, the faster they can address them and prevent future occurrences. Although implementing AI into the production process may require significant upfront costs, the payoffs are often worthwhile because they save executives time and money while enabling improved quality control.
Comments (0)
This post does not have any comments. Be the first to leave a comment below.
Featured Product
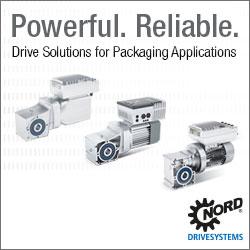