What Are The ISO Standards For Barcode Verification?
Barcodes serve as an essential tool across multiple industries, streamlining processes and enhancing traceability from manufacturing to point-of-sale. Their role in inventory management, logistics, and supply chain highlights the necessity for accuracy and reliability in barcode systems.
To ensure each barcode meets predefined standards of quality and readability, a standardized barcode verification process is essential. This verification process relies heavily on ISO standards to maintain consistency and interoperability on a global scale.
Understanding ISO Standards
The ISO, short for International Organization for Standardization, is an independent, non-governmental organization with membership from national standards bodies from over 160 countries. Established in 1947, ISO is dedicated to developing voluntary, consensus-based, market-relevant international standards that support innovation and provide solutions to global challenges.
ISO standards are developed through a consensus-driven process involving experts from national standards bodies in different countries. This collaborative approach ensures that the standards reflect a balance of interests, are globally relevant and can be implemented across various markets.
The ISO standard development process is methodical and often spans several years. It involves multiple stages, from the initial proposal to the final publication. Each stage involves rigorous scrutiny and multiple rounds of revisions, aiming to make the standards comprehensive and forward-thinking.
Key ISO Standards for Barcodes
Barcodes, whether one-dimensional (1D) or two-dimensional (2D), must comply with specific international standards to meet global compatibility and readability requirements. The International Organization for Standardization has developed three primary standards for barcodes.
-
ISO 15416 for 1D barcodes
-
ISO 15415 for 2D barcodes
-
ISO/IEC TR 29158, or AIM DPM for Direct Part Marking (DPM) barcodes
ISO/IEC 15416
The ISO/IEC 15416 standard applies to linear (1D) barcodes like UPC and EAN. It evaluates barcodes based on six critical parameters, which contribute to the overall effectiveness and readability of the barcode. These parameters include:
-
Minimum Reflectance: Measures the darkest bar and lightest background on the barcode to ensure sufficient contrast for scanning.
-
Edge Contrast: Assesses the sharpness of transitions between bars and spaces.
-
Modulation: Evaluates the uniformity of the light and dark elements within the barcode.
-
Defects: Identifies any printing imperfections like dirt in the bars and spaces that might hinder scanning.
-
Decodability: Measures the precision of the barcode against its intended size and design.
Barcodes are graded on a scale from A to F, with A being the best and F the worst. This grading system is crucial for determining a barcode's usability in practical scenarios.
To determine a barcode's grade, the ISO/IEC 15416 standard requires 10 individual scan lines to be taken across the height of the code via a barcode scanner, with each scan line independently graded.
If a scan line fails in minimum reflectance, decode, or minimum edge contrast, the barcode automatically receives an "F" grade.
If all three initial tests are passed, the software then assesses additional parameters: modulation, defects, and decodability. After each scan line has been graded, the 10 scans are averaged to produce an overall grade for the barcode.
ISO 15415
The ISO/IEC 15415 standard is explicitly tailored for two-dimensional (2D) barcodes, such as QR codes and Data Matrix. It evaluates these barcodes against eight distinct parameters, critical for ensuring high readability and reliable data encoding. These parameters include.
-
Successful Decodation: Ensures the barcode can be decoded correctly.
-
Symbol Contrast: Measures the contrast between the dark and light modules of the barcode.
-
Modulation: Assesses the uniformity of the light and dark elements within the modules.
-
Reflectance Margin: Evaluates the minimum reflectance difference between the darkest and lightest modules.
-
Fixed Pattern Damage: Checks for damage to the fixed patterns, which are critical for decoder algorithms.
-
Axial Non-uniformity: Measures the deviation from the ideal grid alignment along the barcode's uneven scaling.
-
Grid Non-uniformity: Assesses the consistency of the grid pattern across the entire barcode and measures the deviation from the grid.
-
Unused Error Correction: Evaluates the amount of error correction capacity that remains unused, indicating the robustness of the barcode against distortions.
The ISO/IEC 15415 standard also grades barcodes on a scale from A to F, with A being the best. However, the grading system is stringent, as the lowest individual grade on any of the parameters becomes the overall grade for the barcode.
The grading process initiates with a pass/fail test focused on decodation using a 2D barcode scanner. If the barcode decodes correctly, it passes; if not, it is automatically assigned an "F" grade.
Once the barcode passes the initial test, it is then evaluated for the remaining parameters such as symbol contrast, modulation, and fixed pattern damage, among others.
ISO/IEC TR 29158 (AIM DPM)
ISO/IEC TR 29158, also referred to as AIM DPM, sets quality parameters and a grading process for Direct Part Marking (DPM) barcodes. This standard, while similar to ISO/IEC 15415 used for evaluating 2D barcodes, introduces specific modifications tailored to the unique challenges of DPM.
A key difference in AIM DPM is the method for determining the global threshold, which is the dividing line between light and dark cells in a barcode. The position of this line is vital as it dictates whether a cell is interpreted as light or dark.
Unlike ISO/IEC 15415, AIM DPM employs a more sophisticated algorithm to calculate the global threshold, accommodating a diverse range of background surfaces, which often vary in texture and colour in DPM applications. This adaptation generally enhances the modulation quality of the barcode, improving its readability.
Additionally, AIM DPM expands the lighting options for barcode verification, allowing the use of 30°, 90°, and dome lighting configurations in addition to the standard 45°. This flexibility is crucial for accurately verifying barcodes on curved, reflective, or marked parts using dot peen techniques, ensuring reliable readability under varied and challenging conditions.
Importance of Barcode ISO Standards
Adopting ISO standards for barcodes is not merely a procedural formality; it holds significant practical implications for industries worldwide. Here are the key reasons why adhering to these standards is crucial.
-
Enhanced Compatibility and Interoperability: ISO standards ensure that barcode labels can be scanned and interpreted correctly across different systems and countries. This global compatibility is essential for international trade, where products often move across various regions and need consistent tracking.
-
Improved Efficiency and Accuracy: By meeting ISO standards, barcodes achieve high readability levels, which minimizes the risk of errors during scanning. This accuracy is critical in high-speed manufacturing and distribution environments, where even minor errors can lead to significant disruptions and financial loss.
-
Regulatory Compliance: Many industries are subject to stringent regulatory requirements concerning product labelling and tracking. Compliance with ISO barcode standards helps companies meet these legal mandates, avoiding potential fines and legal issues.
-
Cost Savings: Implementing standard-compliant barcodes on labels reduces costs associated with returns, misshipments, and non-compliance fees. Businesses can operate more smoothly when they adopt universally accepted standards that do not require custom solutions for different markets.
Conclusion
ISO standards for barcode verification play a key role in ensuring the efficacy and reliability of barcode systems globally. These standards establish clear, comprehensive guidelines for barcode quality, facilitating smoother operation across various sectors.
Adhering to these ISO standards cannot be overstated. They enhance interoperability and efficiency and support compliance with international trade regulations, thereby fostering a more connected and efficient global marketplace.
Comments (0)
This post does not have any comments. Be the first to leave a comment below.
Featured Product
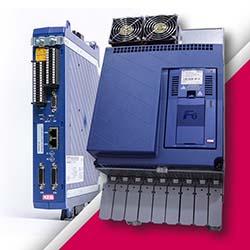