Waste not, want not – rapid identification of metals in scrap
The global demand for various metals is on the rise due to the expanding world population and rapid technological advances. Mining operations are under ever-growing pressure to extract more material from the Earth, but significant shortfalls are predicted. As a result, scrap recycling has gained momentum as a vital practice to address this issue. Recycling metals not only saves precious resources – addressing environmental concerns – but is also cheaper compared to mining new minerals, as less energy is required. Nonetheless, the success of recycling processes hinges on using efficient methods to determine the composition of materials to be recycled. X-ray fluorescence (XRF) is ideal for this; it can assist recyclers with the swift identification of metals and alloys, and is particularly useful for sorting and categorizing alloys in bulk scrap materials.
The need for scrap metal recycling
As populations increase, so too does the need for metals for use in infrastructure, housing and transport. Add to this the drive toward renewable energy and decarbonization – with around 90 % of the world now having established net zero carbon targets – and the range and scarcity of metals needed goes up. This includes switching from fossil fuels to electric vehicles (EVs), which operate on lithium-ion batteries and, therefore, require higher quantities of various metals – including cobalt, nickel, aluminum, and copper. Unfortunately, this spike in demand comes at a time when mining operations around the world face unprecedented challenges; energy prices are high, supplies of high-grade ore are scarce, and miners are frequently working with extremely low metal concentrations.
One solution to this challenge is to increase scrap metal recycling. However, it is extremely important that the exact chemical composition of any material for recycling is known, and that different alloy grades are accurately identified to prevent contamination in downstream processing. Swiftly identifying the most valuable materials within scrap can yield significant profits, justifying the upfront investment in analytical equipment. Handheld devices, such as XRF analyzers, offer recyclers tools to rapidly and accurately determine the composition and grade of incoming scrap. This eliminates the need to depend on traditional verification methods such as spark or chemical tests which involve material grinding and the handling of hazardous substances. Handheld XRF (HHXRF) analyzers can rapidly verify high-value elements in virtually all types of metal alloys, from trace levels to commercially pure metals. These analyzers are even capable of distinguishing numerous alloy grades that are nearly identical in composition to one another, such as 303, 321 and 347 grades of stainless steel which differ by the presence of elements at levels of detection lower than 0.5 %. So, how exactly do such handheld analyzers operate?
How do XRF analyzers work?
HHXRF analyzers – such as the Thermo Scientific™ Niton™ XL2 Plus – produce primary X-rays that are directed at the surface of a sample. The atoms at the surface absorb the primary radiation and each element in the sample to produce a set of characteristic secondary X-rays, also called fluorescence, which can be used as a unique ‘fingerprint’ to identify and quantify elements present in the sample. The detector collects the characteristic X-rays and converts them into electronic pulses, which are amplified, counted and processed in the device’s central processing unit (CPU). The CPU then uses this information to produce a detailed compositional analysis and grade identification of the material. This is a non-destructive process that has no impact on the sample being inspected, with results available within seconds.
[GP2] XRF analyzers produce X-rays that generate unique signals from different elements in a material. The CPU processes the signals received to provide detailed compositional analysis.
HHXRF analyzers are tried and tested in the world of scrap metal recycling, and are well established in many organizations as the best-known method for sorting scrap quickly and accurately. The technology is very useful for distinguishing between different grades of a family of materials, for example separating different stainless steels from incoming streams in different containers. However, XRF is unable to identify lighter elements – generally below magnesium in the periodic table – as the energy released by these low atomic number elements is too low to be detected. In these cases, alternative technologies such as handheld laser induced breakdown spectroscopy (LIBS) analyzers can act as a complementary solution to XRF.
Analysis of scrap metals often begins in environments with potentially harsh conditions, such as scrap yards which are often exposed to all kinds of weather. HHXRF analyzers are built to perform fast, accurate alloy grade identification in just such an environment. Improving the speed of analysis helps recyclers drive efficiencies, while accurate results help them optimize the trading value of the scrap. Steel mills and foundries also use HHXRF analyzers to detect tramp/trace elements that can contaminate downstream processes where bulk scrap is repurposed. When scrap material is transferred to enter into manufacturing and metal fabrication processes, the technology helps both the buyer and seller analyze the scrap to affirm both quality and value.
XRF analyzers such as the Thermo Scientific™ Niton™ XL2 Plus allow quick identification of pure metals and alloys, as well as detection of tramp elements.
Also, beyond the analysis of bulk metals, automotive and aerospace manufacturers rely on metal coatings to improve properties such as resistance to corrosion, wear and heat. Historically, measuring coatings involved either handheld technologies with special capabilities for testing conductivity and magnetism of the material, or destructive sampling and laboratory testing. However, now HHXRF can measure coating thickness on site, providing quick, reliable and non-destructive analysis. This ensures coatings are consistent and within the desired thickness range, preventing manufacturing issues and potential product failures. HHXRF is also widely used in the mining and exploration industries for on-site analysis of ore samples. It can accurately measure the composition of metals and alloys in real time, allowing manufacturers to verify that materials received from suppliers align with the desired specifications. Furthermore, HHXRF finds applications in archaeology, where it is used for non-destructive elemental analysis of artifacts, providing useful insights into their composition and origin.
Summary
HHXRF has transformed scrap metal recycling and QC processes in manufacturing, providing rapid and accurate metal analysis by bringing laboratory capabilities on-site and streamlining processes, while simultaneously ensuring compliance with strict specifications and regulations across different industries. Ongoing advancements – such as expanded elemental detection, increased accuracy, and potential integration with artificial intelligence – promise further improvements in the future, empowering scrap metal recyclers and manufacturers to maintain high-quality processes, reduce costs and enhance the overall efficiency in their operations.
Comments (0)
This post does not have any comments. Be the first to leave a comment below.
Featured Product
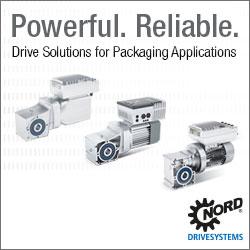