Foundations for Success In Industrial Automation: A Guide for Small to Medium Manufacturers, Part II
Previously, we discussed how small and mid-sized manufacturers can prepare to successfully deploy industrial automation by identifying a clear objective for your automation journey. Once the objective has been established, a team has been assembled and management has bought into the initiative, it’s time to evaluate which part of your operation to automate first.
While there are many factors to consider, here are a few recommendations:
Identify and select a low-risk, quick win
Experts agree you should start small, with a low-risk, “quick-win” project and expand gradually from there. The first automation project will not generate the largest return on investment (ROI), but it should be significant enough to make an immediate impact.
Automation projects that can be easily replicated across multiple functions or locations are an easy way to achieve a quick win. For example, automating a common quality inspection process could significantly improve efficiency. Once successfully deployed in one area, the automated inspection can be rolled out to other lines or facilities. Compared to a larger, singular automation project, this type of incremental approach reduces risk and allows for gradual adoption as comfort levels increase.
Starting with a well-defined, bite-sized project creates momentum and enthusiasm for expanding the rollout of automation more broadly. Quick wins build confidence and help secure buy-in for subsequent initiatives. They also provide an opportunity to refine your implementation approach, helping pave the way for smooth future deployments.
Choose a “productized” application
From the projects identified as low-risk, quick wins, manufacturers embarking on their automation journey should choose a productized application. Productized applications are fully vetted, extensively tested solutions with demonstrated viability and high success rates. Choosing this type of application significantly reduces the risks associated with technology feasibility such as challenges with integration, concerns about reliability or immature ecosystems.
Common “productized” industrial automation use cases fall into five functional categories:
- Manufacturing - bin picking, gantry systems and path following, machine tending, robot 7th axis, robot pedestal,
- Assembly - jigs and fixtures, workstations, shelves and racks
- Packaging - cartesian palletizer, cobot palletizer
- Material handling - automated guided vehicle (AGV) top modules, conveyors, industrial carts
A successful deployment will have a combination of well-productized applications like palletizers as well as applications with manageable deployment risk, such as robot pedestals or jigs and fixtures. These types of diverse use cases and complexity typically result in a low-risk, quick win and a safe place to start with automation.
Perform a factory walkthrough
Once you’ve identified the criteria for your first automation project, it’s time to perform a walkthrough of the facility to determine the right process to automate.
A factory walkthrough involves physically going through the facility area-by-area to directly observe workflows and production processes. The goal is to identify automation opportunities that meet the criteria of a low-risk, quick win. Consider bringing in an experienced automation partner to lend an expert eye. They will be able to spot potential automation areas that might be overlooked by internal staff who are accustomed to standard operating procedures.
For example, we recently conducted a two-day onsite assessment at a client’s manufacturing floor. During the visit we completed an in-person walk-through of their operation and experienced firsthand the automation challenges and pain points facing them. At the end of the visit, we presented our recommendations for a process that would be automated within their established framework - in other words, a low-risk, quick win.
Based on the recommendations, we focused on specific applications the client saw as the “best fit” and presented capital expenditure (CapEx) requirements, level of technology and process complexity, estimated time-to-deployment, ROI calculations, and similar deployment success stories. This type of in-person scoping is invaluable for companies just starting to deploy automation. Ensure your chosen automation partner is able to provide similar services before moving forward.
“Foundations for Success in Industrial Automation: A Guide for Small to Medium Manufacturers” is the second in a three-part series on “How to Kickstart Your Automation Journey.” The final article will discuss establishing an automation roadmap and building a business case for your project.
Comments (0)
This post does not have any comments. Be the first to leave a comment below.
Featured Product
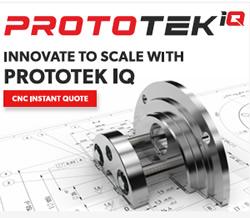