VR Welding and the Future of Metal Fabrication
Virtual reality (VR) might still be a new and improving technology, but it has already made a positive impact in many industries — healthcare, education, supply chain management and even metal fabrication.
Here’s how VR can assist with welding and many other metal fabrication applications to make the industry more streamlined.
Benefits of VR in Metal Fabrication
VR is a realistic three-dimensional environment generated by a computer that allows people to interact within a fictional world called the “metaverse.” This environment is often a depiction of a real-world setting such as a home or workplace. Users can walk around, touch and even move objects. This immersive experience isn’t just for entertainment.
The basic components of VR include a computing device, headset, motion sensors, input devices, an audio system and 3D animation software. Users wear the headset and often have sensors on their arms and legs. The most advanced VR tools even have walking platforms that allow people to move around while staying in the same place in real life.
VR can bring several game-changing benefits to the world of metal fabrication.
1.Enhanced Visualization and Design
For starters, VR’s 3D modeling can provide enhanced visualization and extremely detailed prototypes, which enables welders, fabricators and other metalworking professionals to adjust their designs before they do any real work. They can use the software to create an almost identical version of their current project and experiment within the metaverse.
VR can also provide accurate simulations of complex structures and replicate metal fabrication workflows. Although VR will never exactly replicate the real thing, it’s more than accurate enough to help metalworking professionals address deficiencies virtually. In this way, VR makes it possible to achieve a perfect design for every project it simulates.
2.Greater Efficiency and Productivity
Metal fabricators are already using computers to complete precise tasks such as forming, punching, bending and laser cutting metal products. They simply have to give the computer the proper commands and specifications, and the computer repeats its assigned task with no errors or wasted time.
VR makes these computerized tasks even more efficient. Workers can virtually assemble and disassemble complex metal components in the metaverse, saving time and reducing the chance of an error. They can also learn how to maintain and troubleshoot machinery with VR-powered training programs instead of learning on the fly in a high-stress environment.
VR eliminates the need to sort through traditional blueprints or lengthy computer databases. Everything the user needs is inside the 3D model. Co-workers can interact in the metaverse and provide instant feedback. This streamlined set-up leads to fewer miscommunications, minimal downtime and maximum productivity.
3.Risk Mitigation and Workplace Safety
VR simulations can also make major improvements to workplace safety in metal fabrication jobs. Molten metal has no issue reaching temperatures of 2,500F or higher for welding and forging applications, which makes for an extremely dangerous work environment. VR can help workers monitor temperature and other hazards, thus preventing accidents.
VR also provides a more immersive environment for various safety training methods, including hazard recognition, emergency response and even fall protection. It’s an all-in-one risk assessment tool that allows professionals to maximize the safety of every step of the metal fabrication process.
Real-Life VR Applications
There are already numerous real-world examples of VR improving metal fabrication, especially in welding and metal cutting. Many companies and research centers are using virtual welding simulators to provide accessible and customizable training for aspiring professionals. Classes and instructions have never been more hands-on.
Young novices can go through flame-free simulations without any risk of damaging equipment or injuring themselves. The skills they learn in the metaverse have proven to translate to real-world environments. The United States is facing a shortage of welders and other metalworkers, so VR can play a huge role in rebuilding the industry’s labor force.
Training will only become more immersive as VR evolves. For example, the Massachusetts Institute of Technology recently developed a VR headset with X-ray vision that allows users to identify items hidden from view. In the context of metalwork, this technology can help professionals spot the smallest defects in metal products that can’t be seen with the naked eye.
This training experience isn’t just exclusive to the world’s top universities or Fortune 500 companies. Louisiana-based company SSE Steel Fabrication is adding a fleet of collaborative welding robots that interact with employees in a virtual setting. These “cobots” assist workers with pre- and post-welding tasks, including material handling, parts manipulation and final inspections.
VR also helps companies test and optimize their assembly lines by providing a digital twin for experimentation. They can test different line configurations, deploy workers at different stations and identify potential bottlenecks without sacrificing any time or resources. Once they discover the most efficient configuration, they can make the necessary adjustments in real life.
Similarly, VR is a perfect quality control tool. Workers can conduct thorough virtual inspections and form a detailed analysis of complex metal structures, discovering the smallest defects. It’s especially useful for non-destructive testing when companies need to inspect expensive products such as cars and aircrafts.
Challenges That Lie Ahead
Although virtual reality has already made a big splash in metal fabrication, there are some challenges that industry professionals need to consider. The most pressing issue is the cost and availability of VR technology. The initial investments for VR equipment and software can be significant, making it inaccessible to small-scale metalworking companies.
Integrating VR within existing metal fabrication workflows is another hurdle. Businesses might experience compatibility issues with their existing computer-aided design (CAD) software and other digital tools. This problem could get worse as VR technology continues to advance and other softwares get left behind.
Integrating VR with other technologies such as cloud computing and Internet of Things (IoT) could also complicate things. Investing in one new technology is a big commitment by itself, so businesses might be hesitant to buy in if they need to completely overhaul their existing software.
Finally, the general public is concerned about VR’s effect on our long-term health. Nobody denies that it’s a useful tool for training employees and optimizing workflows, but it could cause painful side effects if used too frequently. People have reported symptoms such as eye strains, headaches, nausea and disorientation.
VR is a Key Part of Metal Fabrication Moving Forward
The concerns about VR integration and its health consequences are valid, but it has already proven itself in the world of metal fabrication. It will remain a key part of this industry moving forward, from training new employees to identifying metal defects to making the workplace safer.
It doesn’t have to be an all-encompassing solution for these tasks that people use every day. It can just be a valuable resource that companies can use when they see fit.
Comments (0)
This post does not have any comments. Be the first to leave a comment below.
Featured Product
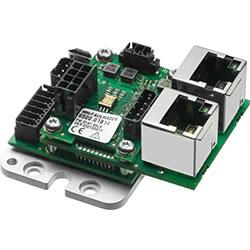