Issues Facing the Manufacturing Supply Chain & Their Fixes
Here’s the issue with the problems facing our manufacturing supply chains: Too often, we talk about them in isolation. Inventory management problems are distinct from poor contingency planning. Supply chain visibility is a different challenge than finding reliable suppliers. And logistical challenges are varied and many. These are all fundamentally different things.
But they’re so interconnected we can only truly address them in an integrated, holistic way.
“The global manufacturing supply chain is a single, integrated ecosystem of trade that requires an all-hands approach if it’s to operate efficiently and fluidly,” said Robert Parker, Director of Logistics at DP World Canada. “Technology is a critical part of the solution. But technology is just where it starts. Ultimately, suppliers, manufacturers, and customers all must commit to ongoing communication and collaboration for the manufacturing supply chain to operate as we all want it to.”
Let’s look at each of the five most common manufacturing supply chain challenges in turn, before we explore the path forward.
1 - Supplier Reliability
In recent years, concerns about political instability around the globe have led both North American and Western European countries (amongst others) to embrace near-shoring.
This has served to shrink the length of supply chains not just physically (e.g., the North American automobile industry expanding aggressively in Mexico) but socio-politically (e.g., with some Western companies relocating facilities away from political hotbeds to countries with reliably democratic systems of government).
Near-shoring makes it more likely we can address some of our stickiest supply chain issues. But as we’ll see, it alone is no guarantee of success.
2 - Supply Chain Visibility
Supply chain visibility problems compound all the other issues you might be facing.
Without an effective view of where your shipments are in the world – which carrier they’re with, what delays they’re facing, their expected arrival times, and what it all means for your inventory – it makes it next to impossible to address all your other common challenges.
This means that a manufacturer without visibility into its supply chain may lose control of its operations and, ultimately, fail. The company may be able to stagger along for a while, but the challenges are too great in our current environment to fly blind. That’s how important supply chain visibility is in 2023.
Happily, the solution here is relatively simple: technology. And manufacturers don’t need to go in it alone when it comes to supply chain visibility technology either. They can now work with an end-to-end service provider, which will give them full line-of-sight into their supply chain.
3 - Poor Inventory Management
Without the right software, effective inventory management is becoming increasingly impossible. Large companies already know this. However, there are still some smaller and medium size companies which still prefer to have people with pads and paper walking around a warehouse doing inventory instead of investing in a technology solution. But that won’t be sustainable much longer. With a move away from push-to-pull distribution, and the mainstreaming of a just-in-time approach to inventory, there simply isn’t enough slack in the system to effectively control inventory with an old-school approach.
The problem for small and medium size companies is usually cost (the relevant software is perceived as too expensive), complication (the software requires various workarounds to be effective) or culture (they’ve always managed inventory by hand) but those challenges will increasingly pale in comparison to the competitive disadvantage of poor inventory management.
That’s a couple of challenges now that can be partly or fully addressed by technology. But of course, in global trade, software alone won’t fix what ails us.
4 - Logistical Challenges
Logistical problems will never go away. Anyone in manufacturing will tell you that. Freight is routed and rerouted millions of times around the globe every single day due to equipment availability issues, mechanical problems, bottlenecks at ports and on roads and rail, weather-related events, political unrest, and dozens of other all-too-common challenges.
The sheer scope of a typical manufacturer’s supply chain – even one that’s been near-shored and optimized with the latest technology – creates significant opportunities for something to go wrong.
Which leads us – and manufacturers - to the next big issue.
What happens when something does go wrong?
5 - Contingency Planning
It’s fair to argue that the global supply chain has not optimized its ability to plan for contingencies. This is also true of individual companies.
This is intuitive when you think about everything we’ve discussed in this article up until now. If a manufacturer doesn’t have visibility into its supply chain (problem #2), how can it effectively plan for logistical challenges (problem #4)? And if that same manufacturer has a supplier reliability issue (problem #1) that will only be compounded by poor inventory management (problem #3).
A system-level problem requires a system-level solution.
While any single manufacturer can address *some* of these issues by implementing technology or seeking out reliable logistics providers, this is a system-level problem that requires a system-level solution.
“There’s no single silver bullet to solve this,” said Parker. “At DP World Canada, we see supply chains from every angle. Our footprint covers ports and terminals, and we’re making massive investments in innovative technology. But without our partnerships with the other players in the supply chain, without their commitment and collaboration, even an organization as large as ours can’t drive all the changes we need to make.”
“This is a global problem. Which means it’s a problem for the everyone around the globe.”
Comments (0)
This post does not have any comments. Be the first to leave a comment below.
Featured Product
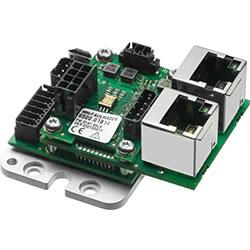